Longitudinal joints are one of the first parts of a pavement to fail. As a road’s most permeable location, air and water seep into voids at the construction joint, leading to premature cracking, potholing and delamination of the surface.
However, there is a materials-based approach to protecting longitudinal joints. J-Band® is an engineered asphalt membrane that keeps out air and water and offers better density and compaction around the joint so it can stand the test of time.
US-51 Project History
The 2002 J-Band application on US-51 was one of J-Band’s first major demo projects. Two years prior, the Illinois Department of Transportation (IDOT), Asphalt Materials, Inc. (AMI) and Heritage Research Group (HRG) worked together to find an alternative solution for the recurring issue of longitudinal joint failure. HRG developed a new asphalt technology, the void reducing asphalt membrane (VRAM), which Illinois refers to as a longitudinal joint sealant (LJS). As the premier VRAM, J-Band significantly reduces voids and permeability in the longitudinal joint from the bottom up — literally.
For this experimental project just south of Decatur, Illinois, J-Band was sprayed in four 100-ft test sections. These test sections were interspersed with clearly marked control sections, so the joint’s performance could be evaluated year over year.
Project Details
- Owner: IDOT
- Prime Paving Contractor: Illinois Valley Paving
- J-Band Applicator: Emulsicoat, Inc.
- Location: US Route 51, Elwin, IL in Macon Co.
- Date Constructed: September 2002
- Dates Reviewed: 2013, 2017, 2019, 2022
Application Process
J-Band is applied as part of the normal HMA construction process. It is sprayed before HMA paving in a band, usually 18” wide, on the existing binder course where there will be a longitudinal surface joint or rumble strip. It can be applied thick without running and is non-tracking within 30 minutes, allowing construction traffic to keep moving. The heat from the final lift of HMA pavement and the pressure of the rollers cause J-Band to migrate up into the voids at the longitudinal joint. This significantly reduces permeability so the joint can last as long as the rest of the pavement.
Project Review
When US-51’s test site was reviewed in 2013, the impressive condition of the joint with LJS/VRAM prompted IDOT to develop a specification adding LJS/VRAM to future paving projects. AMI’s VRAM product, J-Band, meets this specification.
The US-51 project has also been reviewed in 2017, 2019 and 2022. Even 20 years after the initial application, the difference in performance between the J-Band and control test sections can be seen in the images below. Without J-Band, the centerline experienced severe deterioration, with prevalent potholes that were filled on multiple occasions.
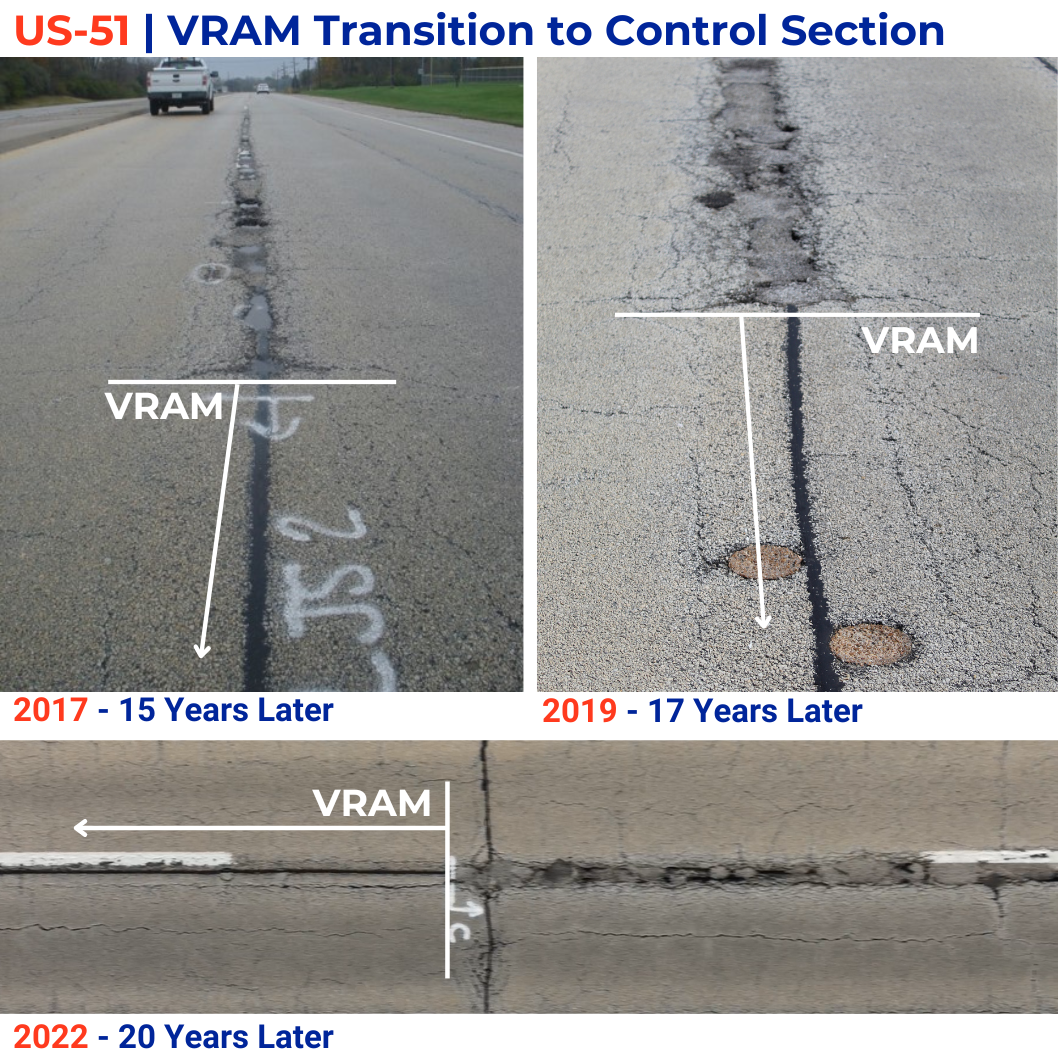
The Proof is in the Pavement
Lab testing of cores taken from the US-51 centerline showed that the use of a VRAM decreases pavement permeability by increasing the asphalt content. Density was measured at an average of 3-5% higher for cores from the VRAM test sections. Additionally, I-FIT testing found that VRAM cores had about 28 times higher cracking resistance than control cores.
From lab tests to visual evaluation, the US-51 project is proof of how J-Band can preserve longitudinal joints for over 20 years. With a VRAM in place, agencies can eliminate their typical longitudinal crack sealing every 3-5 years, which is safer for workers and the motoring public. By extending the life of pavement and deferring maintenance costs and risks, J-Band is saving time, money and lives.
Resources
- To see how J-Band has been incorporated across more than 25 states, visit our interactive project map: Project Map – J-Band (thejointsolution.com)
- To get a better idea of how J-Band compares against traditional treatments, try our ROI Calculator tool: Calculator – J-Band (thejointsolution.com)