In a time when drivers are more distracted than ever, rumble strips are a necessity to save motorists from head-on collisions and road departure crashes. The Federal Highway Administration reports that, “milled centerline rumble strips provide statistically significant reductions in injury crashes of 38-50% on rural two-lane roads and 37-91% on urban two-lane road” (Research conducted by NCHRP).
Rumble Strip Noise Research
Rumble strips alert drivers of lane departure by increasing internal vehicle noise and vibration when vehicle tires traverse the corrugations. As a byproduct of these driver-alerting benefits, rumble strips increase external noise. This external nuisance-noise has led residents near roadways with rumble strips to complain about excess noise pollution.
The problem of noise pollution has become significant; TRB’s National Cooperative Highway Research Program (NCHRP) funded project 15-68: Effective Low Noise Rumble Strips to investigate whether noise pollution generated from rumble strips could be reduced by optimizing rumble strip geometry, while maintaining functionality of the rumble strip.
The final report, published as NCHRP Report 1107 in July 2024, presents both a standard method to assess rumble strip functionality against external noise generation and a recommendation for agencies on geometries that minimize external noise generation. The authors recommend a sinusoidal rumble strip geometry (sometimes referred to as “mumble strips”). Sinusoidal rumble strips are a type of continuous corrugation in which the depth of corrugation takes the shape of a sine wave.
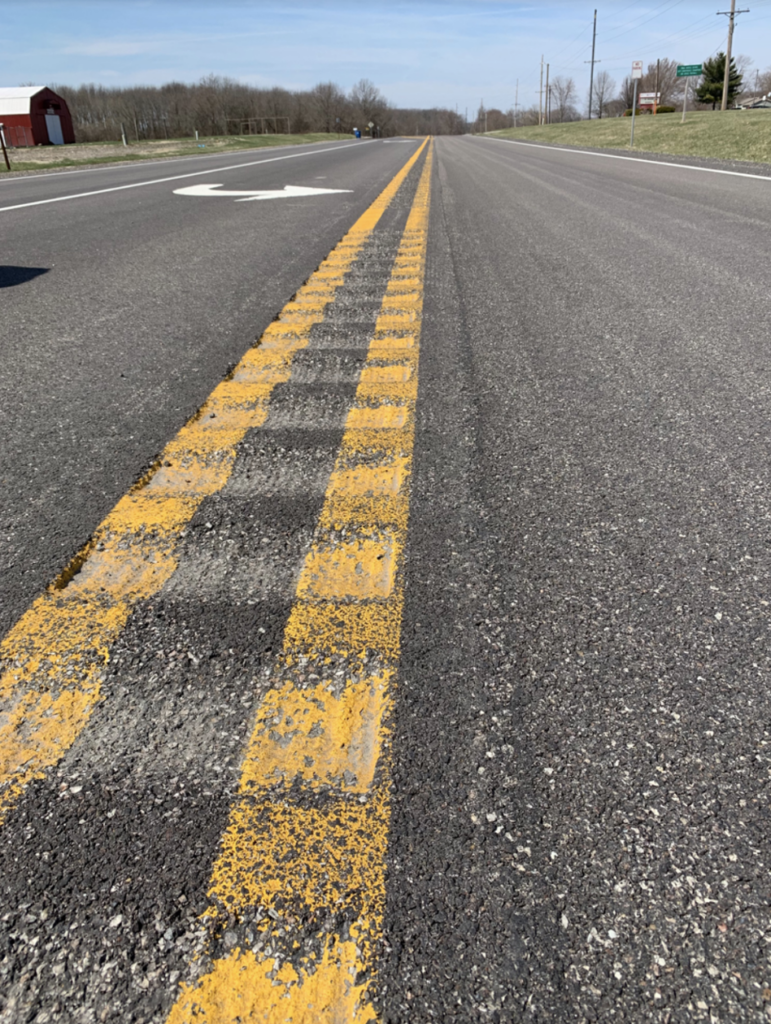
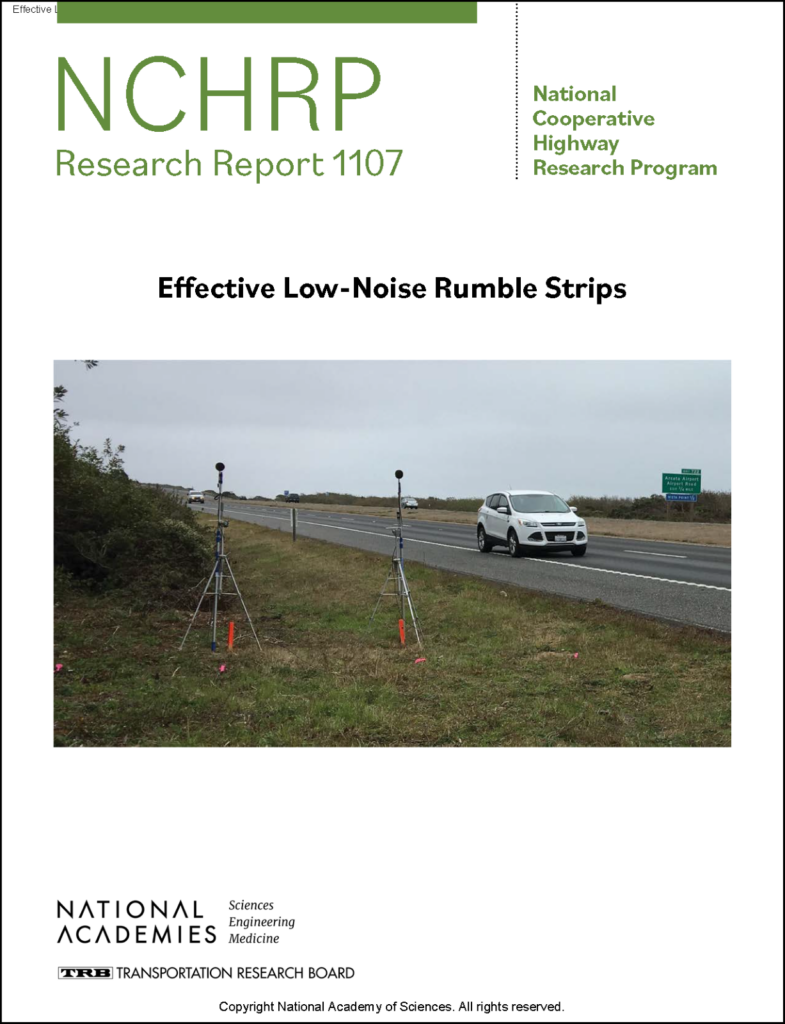
Sinusoidal rumble strip, NCHRP’s recommended rumble strip geometry
The authors also concluded that rumble strip geometry is strongly linked to both effectiveness and nuisance noise. In two Indiana field sites used in the study, the sinusoidal rumble strips were chip sealed before evaluation for noise. The researchers found that because the chip seal significantly altered the rumble strip geometry, the chip seal produced higher background (off-strip) noise, and the treatment actually reduced rumble strip effectiveness as a safety tool. Chip seals are a very cost-effective preventive treatment to be sure, but chip seal’s impact on the surface profile must be considered in the case of roads with rumble strips. Nevertheless, preserving rumble strips and the surrounding joint is a primary concern to highway engineers.
Rumble Strips’ Weakness
While rumble strips save lives, they also add a vulnerability to pavement. Longitudinal joints are typically the first part of a pavement to fail for a variety of reasons. Centerline and shoulder rumble strips, by nature of their grooves, collect water at the most permeable part of the pavement, which may accelerate joint deterioration and reduce the effectiveness of the rumble strip.
A Materials-Based Solution
As an alternative to top-down pavement treatments, there is a bottom-up solution applied at the time of construction. Many states are using a void reducing asphalt membrane (VRAM) to protect their longitudinal joints and rumble strips just before paving. VRAM is a polymer modified asphalt, added at the location of the longitudinal joint just before the surface course construction, reducing permeability and providing measurable cracking resistance.
Ongoing research funded by the National Road Research Alliance (NRRA) is working on understanding how VRAM, among other treatments, may be able to preserve rumble strip functionality while increasing longitudinal joint performance.
With a VRAM, longitudinal joints last longer, far above 15 years, reducing the need for crack filling and other joint maintenance. This keeps workers off the centerline, which is safer for everyone involved.
No matter the type of rumble strip, with VRAM, agencies can have rumble strips and longer-lasting, safer roads.
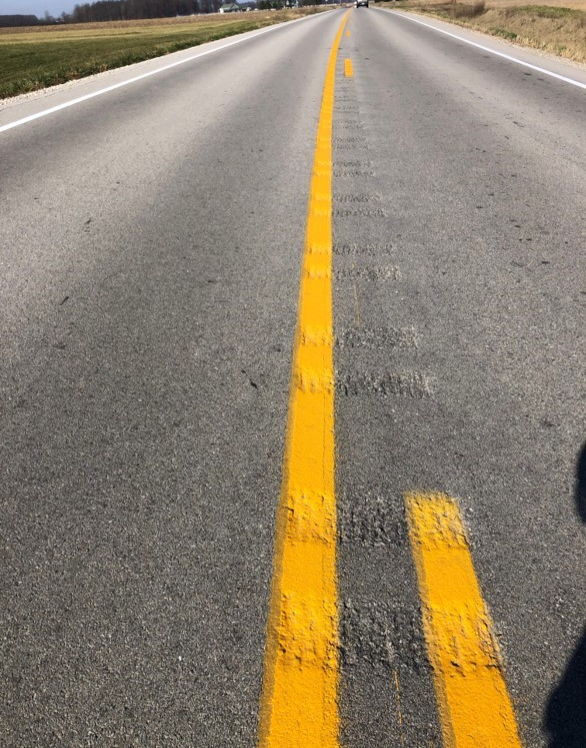
SR-26 with VRAM, Indiana, No cracking has appeared at the paving joint after 4 years
Curious about VRAM?
Across the U.S., hundreds of miles of rumble strips have been reinforced with VRAM. And it is doing more than saving lives. As one of the first states to add VRAM as a state specification, the Illinois Department of Transportation’s return on investment ROI has been 3-5 times the cost of the material.
Learn how you can save time, money and lives by adding this asphalt technology to your projects. thejointsolution.com/calculator/
Reference the full study here:
National Academies of Sciences, Engineering, and Medicine. 2024. Effective Low-Noise Rumble Strips. Washington, DC: The National Academies Press. https://doi.org/10.17226/27861.
Editor’s Note:
J-Band®, the premier VRAM, was created in the labs of the Heritage Research Group (HRG) and is a product of Asphalt Materials, Inc. (AMI).