Road construction can be dangerous. Vehicles zoom past field workers at hazardous speeds. One of the riskiest places to be is near the centerline of a busy road. Quality control technicians have lost their lives when performing density tests at the joint. Unfortunately, density testing of the center longitudinal joint is often a requirement.
Asphalt pavement roadways must achieve the target density of 92-94% on the mat and 1-2% lower at the joint for long-term pavement performance. Pavements, or sections of pavement, that have lower density have higher permeability. This causes durability issues resulting in premature cracking and degradation of the pavement.
What if there was a way to avoid density tests at the centerline while still gaining assurance of exceptional performance? This is where a revolutionary product called J-Band enters the scene.
What is J-Band?
In response to the issue of longitudinal joint performance, a product was developed by Heritage Research Group and produced by Asphalt Materials, Inc. called J-Band. It is the premier void reducing asphalt membrane (VRAM), also known as longitudinal joint sealant (LJS) in Illinois, which uniquely reduces the permeability of the pavement joint area, protecting the joint from destructive air and water damage. Unlike other joint treatments, J-Band is placed beneath the intended pavement area during construction, rather than over the joint after construction.
How Does a VRAM/LJS Work?
VRAM fits into the normal hot mix asphalt (HMA) construction process by being applied prior to the HMA at the location of the longitudinal joint or rumble strip, typically in an 18” wide band. Through the heat of the HMA and the compaction of the rollers, the VRAM migrates upward, filling voids in areas of the longitudinal joints from the bottom up. VRAM reinforces the joint and prevents water from entering the voids.
Laying J-Band on Wheeling Pike Rd. in Grant County, IN
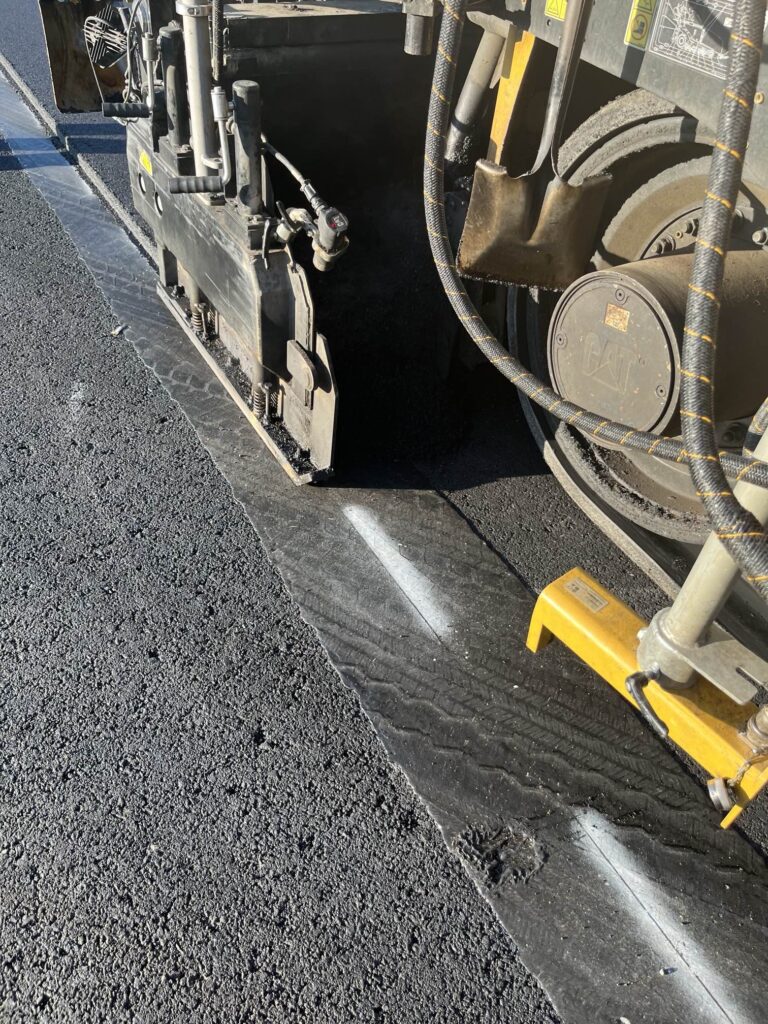
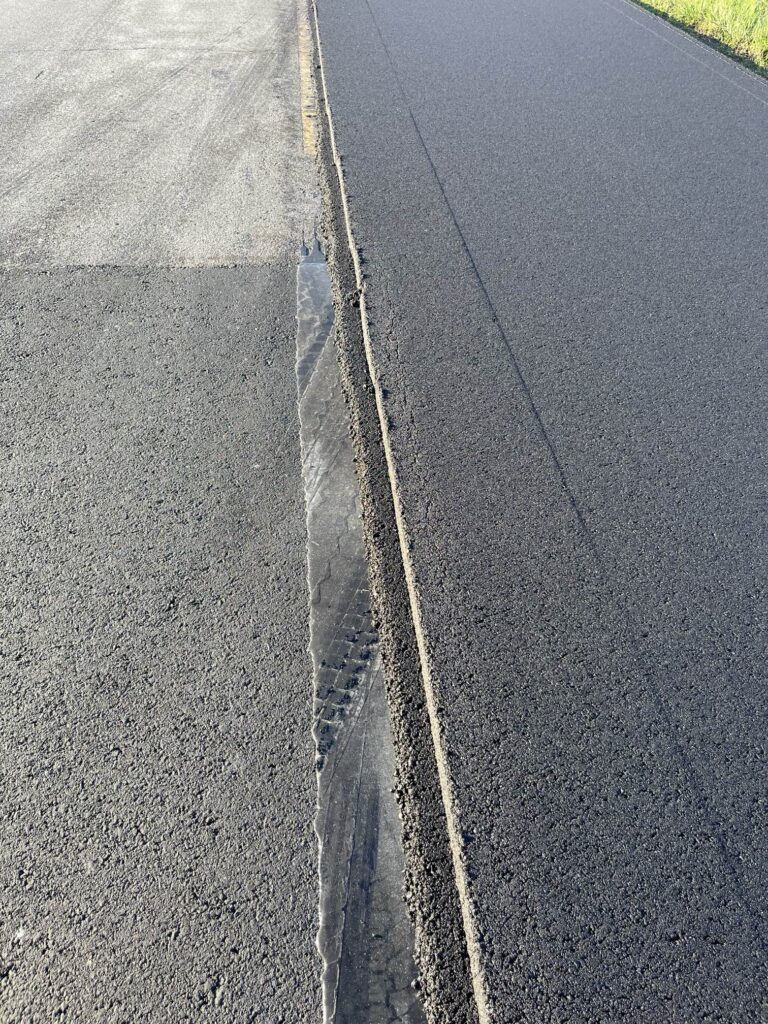
Paving on top of J-Band
Testing the Efficacy
While J-Band has proven itself across hundreds of projects, lab tests also support how it enhances pavement durability. Many tests have been developed to evaluate the quality of pavement mix designs. Using these same tests, the effects of J-Band on a pavement mixture can be evaluated. By filling air voids in and around the longitudinal joint, the VRAM J-Band reduces the risk of water penetration into excessive air voids, which leads to cracking. The following studies demonstrate this crack-preventing quality.
I-FIT
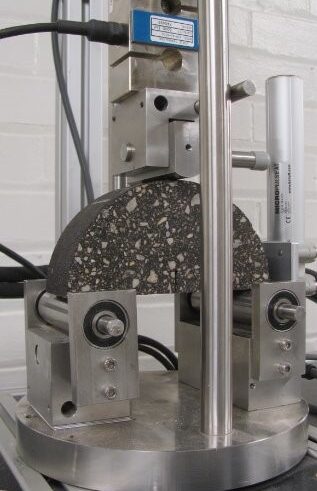
The Illinois Flexibility Index Test (I-FIT) determines the cracking potential of an asphalt mixture. The higher the FI value, the better the cracking resistance.
County/Year Laid/Road | Average FI with J-Band | Average FI Control Section | % FI Increase with J-Band |
Clinton County, Iowa – 2021 Old Highway 30 | 128 | 40 | 220% |
Dakota County, Minnesota – 2021 Highway 61 | 258 | 90 | 187% |
Platte County, Wyoming – 2018 Interstate 25 | 254 | 57.1 | 335% |
I-FIT Results
These results were produced by sampling multiple cores from sections of the centerline with and without J-Band. The average FI values indicate longitudinal joints with J-Band have significantly better cracking resistance than joints without J-Band.
IDEAL-CT
Indirect Tensile Asphalt Cracking Test (IDEAL-CT) is another test used to determine the cracking potential of a given asphalt mixture. It utilizes a fracture mechanics-based parameter, the Cracking Tolerance (CT) Index. The higher the CT-Index value, the better a mix is at resisting cracking.
Heritage Research Group conducted the following testing of VRAM under rumble strips, published in a report for the Transportation Research Board (TRB) 2023 Annual Meeting. In addition to longitudinal joints, VRAM is also used to preserve rumble strips. While rumble strips are an essential feature for road safety, they can lead to reduced pavement life. This study investigated the impact of rumble strips on longitudinal joint pavement performance.
The CT-Index Results
The study found that “In the case of the Lowell Plant test sections that included VRAM (with or without rumble strips), The CT-Index was an average of 250% higher for sections that contained VRAM, demonstrating an increase in cracking resistance of the asphalt mixture.” Joints without VRAM had poorer crack resistance, as measured by this test.
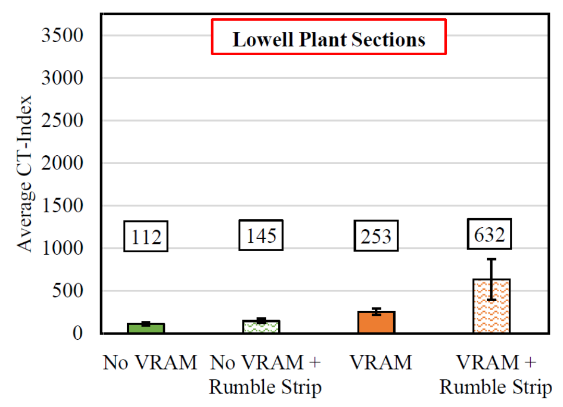
The study concluded, “The bottom-up approach of using a VRAM to seal the centerline joint prior to the installation of rumble strips was effective in mitigating permeability concerns. Test sections that contained VRAM showed minimal to no permeability and therefore durability of the longitudinal joint would be expected to improve.”
Density Testing at the Joint is Not Required with a VRAM
Density is a measurement of pavement compaction, but achieving density at the longitudinal joint by mechanical means has been elusive for decades. Increasing density is about reducing permeability, which increases performance. By applying a VRAM below the joint, pavement permeability reaches zero or near zero, translating to good performance. For roads with a VRAM, if the joint is compacted with the same required roller pattern as the rest of the mat, agencies do not need density testing at the joint. J-Band ensures the centerline will have at least the same performance as the rest of the road.
As part of the specification developed for VRAM, the following is stated. “The area 1.0 ft on either side of the longitudinal joint will be excluded from density measurement and pay adjustment.”
IDOT has also determined that, “When the LJS is specified, the longitudinal joint density testing will not be required on the joint(s) with the LJS.”
Safety First
With no need for centerline density testing, crews can avoid hazardous work that has claimed lives. Additionally, there is no need for a surface joint sealant when J-Band is being used. As joint sealants are often applied by hand, this keeps additional crew members away from the center joint.
Finally, by preserving rumble strips, J-Band preserves this additional safety measure for motorists without risking the accelerated degradation of the pavement from center or shoulder rumble strips.
The proof is in the pavement: an investment in J-Band is an investment in safety.
Curious to learn more? Calculate your return on investment when you add J-Band to your next road project.