Whenever asphalt pavement is laid along a concrete surface, such as a concrete lane, shoulder or curb, it is crucial to obtain a good bond. Bonding hot mix asphalt (HMA) to concrete is challenging as the HMA can pull away from the concrete creating an opening at the interface. These openings collect water, leading to cracking, sub-surface erosion, potholes, and failure of the pavement structure.
The Minnesota Road Research test facility reported that “Sealing the edge joint on concrete pavements with bituminous shoulders is shown to reduce the total volume of water entering the pavement system by as much as 85% for a given rain event”. In pursuit of optimal preventative pavement maintenance, they recommend sealing the longitudinal edge joints of concrete pavement.
There are a couple common approaches to sealing these asphalt-concrete interfaces after paving.
Traditional Asphalt-Concrete Joint Sealing and Filling Methods
Rout and Seal
- Process: This method involves routing (cutting) a notch over the joint and filling it with a sealant. It is most effective for wide joints and provides a durable seal that accommodates the slight movement between asphalt and concrete.
- Considerations: While highly effective, routing is time-intensive and often more expensive than other methods.
Clean and Fill
- Process: For narrow joints where the concrete curb or gutter pan cannot accommodate routing, this method is used. The joint is thoroughly cleaned to remove dirt, dust, vegetation or moisture that could hinder adhesion. After cleaning, the joint is filled with a sealant such as a rubberized or silicone joint seal. This approach is simpler and quicker than routing.
- Considerations: Precise preparation is essential for success. Due to pavement stress and movement, there is a higher risk of sealant failure over time.
An Alternative Joint Treatment
There is an alternative approach to joint treatment that occurs before the HMA is laid. A void reducing asphalt membrane (VRAM) is sprayed at the HMA and concrete interface, as well as below the new HMA, prior to paving. This results in the concrete face being “painted” with an asphalt membrane, creating a better bond at the interface. By treating the joint from the beginning, water does not have a chance to infiltrate, reducing maintenance due to joint deterioration.
When applying VRAM prior to paving, the material must possess a high viscosity in order to remain in the intended location. J-Band, a VRAM, is a proven solution for reinforcing asphalt pavement longitudinal joints. As a specially engineered highly-polymer-modified asphalt, VRAM also excels in bonding the asphalt mix interfaces along concrete lanes and curbs.
How J-Band Works
For longitudinal joints, J-Band is typically applied as an 18-inch band at the future joint’s location, or 9-inches of either side of the joint. Once the HMA is paved over the VRAM, the heat from the asphalt and pressure of the rolling operation causes the VRAM to migrate up, filling voids in the pavement. This means, in addition to bonding the asphalt and concrete together, voids along the interface are filled with enough engineered asphalt to prevent or slow damage.
J-Band has been shown to extend the life of joints three-fold, saving agencies at least $2 on deferred maintenance and repairs for every $1 they invest in VRAM.
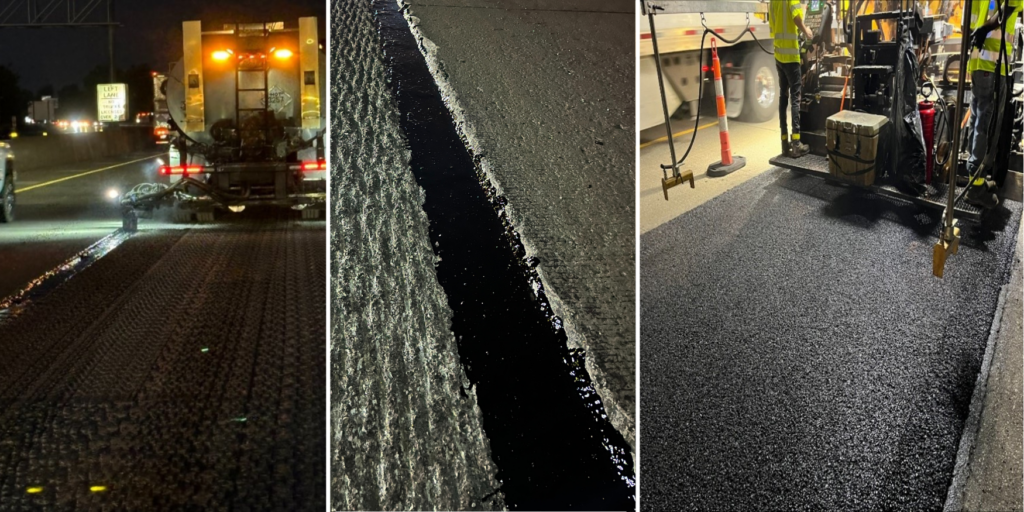
J-band Applicator Truck Hot Mix Asphalt Paving
Using a Void Reducing Asphalt Membrane Along Concrete
Agencies in Illinois, Missouri and Arizona have elected to include a VRAM in their specifications when dealing with a concrete-pavement interface. For these use cases, a “half-width” 9-inch VRAM application is specified along the gutter reveal of a concrete curb or concrete pavement adjacent to a HMA layer.
Additionally, the applicator sprays VRAM on the vertical face of the concrete, getting good adherence. When the asphalt pavement is placed, the VRAM migrates up into the asphalt, sealing the joint at the time of paving and mitigating permeability concerns on the outer edge of the HMA mat where compaction is difficult to achieve.
An Example of Proactive Bonding
A notable example comes from a 7.19-mile project on Interstate 44 in St. Louis County, Missouri. Here, VRAM was applied in a 9” band at the longitudinal joint over a milled surface adjacent to a concrete lane. After the VRAM application, a 2-inch asphalt mix was paved atop the milled surface.
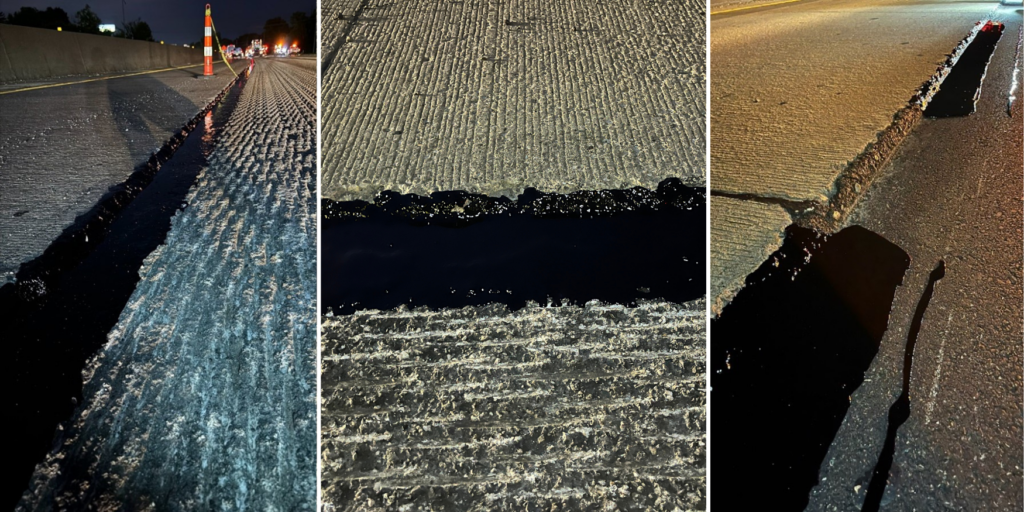
9-inch J-band Application Along the Face and Edge of a Concrete Lane on I-44
Material Removed for Quality Assurance Testing
Streamlining Joint Bonding with J-Band
By incorporating a VRAM like J-Band, agencies can achieve a simple, yet quality, joint construction process during paving operations. Unlike traditional sealants, J-Band not only seals openings but also fills HMA air voids in and around the longitudinal joint, reducing the risk of water penetration. Testing consistently demonstrates that longitudinal joints with J-Band have significantly better cracking resistance and lower permeability than those without.
With a VRAM protecting vulnerable roadway joints, agencies can focus their time, energy and funding on other essential infrastructure investments.
Are you interested in using J-Band to preserve your roads? Get in touch with our team today.