When it comes to road construction, it is important to ensure that roads are safe, durable, and sustainable. However, the longitudinal joint can be the Achilles’ heel of a paved road.
Left unprotected, road managers know that the longitudinal joint is the first part of the pavement to fail. As a road’s most permeable part, this joint is susceptible to the elements. Air and water work down through these interconnected voids, causing the joint to deteriorate, crack, and pothole.
And when the longitudinal joint fails, the rest of the road soon follows—triggering the need for even more maintenance. Negative outcomes from deteriorating pavements due to longitudinal joint failure may include higher costs, lost time, and lost lives.
The challenge is to find a joint solution to air and water permeability.
How can roads be constructed with a bulletproof longitudinal joint?
Research shows that the use of a Void Reducing Asphalt Membrane (VRAM) and a Rapid Penetrating Emulsion (RPE) at the centerline is essential to the construction process and can add to the longevity of a pavement.
What is VRAM?
VRAM is a specially formulated polymer modified asphalt membrane that migrates upwards filling voids that can be penetrated by water and air; this prevents damage before it starts, extending road performance and durability. Used since 2002, VRAM has a proven track record of delivering longer lasting, safer, more sustainable roads.
Historical data from previous VRAM projects shows that an investment in protecting the longitudinal joint helps roads last up to 5 years longer and delivers a return on investment of 3 to 5 times its cost.
What is RPE?
A Rapid Penetrating Emulsion, or RPE, is a specially formulated emulsion made to penetrate quickly into the asphalt surface. The penetration into the pavement makes it possible for the emulsion to carry additional asphalt residue into the smaller interconnected voids in the pavement. This helps fill the voids and reduces permeability, which in turn reduces the amount of water that can seep into the road and cause damage.
The science of the RPE’s penetration is explained by the surface tension, a property that causes a liquid to be attracted to itself, which is why you can fill a glass above its rim. If the surface tension is too strong, the liquid will not ‘break’ the surface tension and therefore will not flow into a porous material like an untreated pavement.
Example of the effect of surface tension
The formula used in AMI’s RPE is designed to break surface tension so that the liquid will move into the small crevices at and voids within the road. (This is the P, Penetrating part of RPE). This unique formulation makes it possible for RPE to quickly cover large areas with minimal disruption, allowing drivers back on their route more quickly after repairs are made. (This is the R, Rapidly part of RPE).
What are the Differences of VRAM and RPE?
VRAM
|
RPE 1. Neat asphalt binder emulsion. 2. Applied to a pavement surface AFTER the final HMA is placed. 3. Penetrates into the pavement; not on the pavement. 4. Extends pavement life by reducing permeability from the top down. 5. A topical treatment that may slow the aging effect. |
Why Utilizing Both VRAM and RPE Are Important to Protecting Your Pavements
By using both a Void Reducing Asphalt Membrane and A Rapid Penetrating Emulsion TOGETHER, you are creating an even stronger, more durable, longer-lasting, safer road.
Safety Considerations
As concerns for road safety increase, more and more transportation departments are investing in rumble strips as a solution to decrease traffic accidents. Centerline rumble strips (CLRS) are textured grooves milled into the center of a pavement which provides a warning to drivers that they are deviating from their lane.
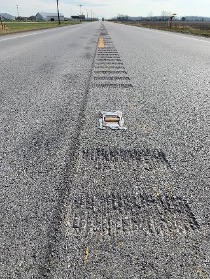
CLRS have been proven to save lives. However, the installation of rumble strips can increase permeability at the surface which can cause damage to the road, leading to a different type of safety concern.
Centerline rumble strips, which can reduce head-on collisions by up to 50%,
can be installed without compromising road life when VRAM is applied.
Unprotected, CLRS add additional stress to an already vulnerable area of the pavement as shown by the picture above.
VRAM is an investment to protect your roads while rumble strips are an investment to protect drivers. When both solutions work together there is protection for roads and drivers. Applying VRAM at the time of construction, under the surface where centerline rumble strips will be installed, will reduce permeability in this most critical area.
But Can You Do More to Protect CLRS?
Based on published data and a review of case studies, implementing, and evaluating Void Reducing Asphalt Membrane (VRAM) during the construction process is recommended. Post-construction, it is recommended to use penetrating asphalt emulsions as a preventative and remedial treatment for longitudinal joints.
The Road Manager’s Equation For Safer Roads
VRAM + HMA + CLRS + RPE = Longer Lasting, Safer Roads
RPE – in the Pavement. Not on the Pavement. Traditionally, fog seals applied to joints have been used to strengthen rumble strips, but this method can create a film over the road that reduces macrotexture, making it difficult for lane stripes to adhere properly. This presents significant safety risks, as well as a costly issue with frequent replacement of the stripes. This is where RPE can be a solution. With RPE’s protection, it doesn’t compromise the macrotexture of the rumble strips, because a penetrating emulsion goes into the pavement instead of sitting on top of the pavement. In addition, thermoplastic striping can adhere better to treated areas, ensuring longer-lasting roads for the traveling public. |
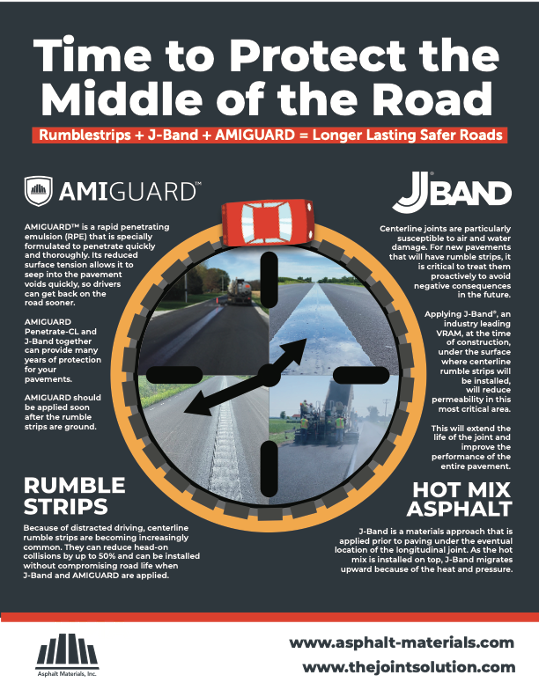
J-Band®, CCAP® and T-Bond® are registered trademarks of Asphalt Materials, Inc. AMIBIND™, AMIBOND™, AMICYCLE™, AMIGUARD™, AMISEAL™ are trademarks of Asphalt Materials, Inc.
J-Band® was created in the labs of the Heritage Research Group (HRG) and is a product of Asphalt Materials, Inc. (AMI).
www.asphalt-materials.com