Have you ever wondered why your longitudinal joint is cracking and deteriorating over time? It’s probably because the pavement joint is highly permeable, which allows elements such as water and air to seep into the pavement and break it down. Pavement joints are traditionally hard areas to obtain density, leading to high permeability.
A void reducing asphalt membrane (VRAM) such as J-Band can be used at the time of construction to create an impermeable barrier at the longitudinal joint.
How VRAM Works
VRAM is immediately applied prior to the paving process, as part of the normal hot mix asphalt construction process. It is applied using an inline parallel spray bar and covers a width of 18 inches wide on top of the existing pavement (existing surface, milled asphalt, concrete, etc.) but prior to paving, at the location of the longitudinal joint. The heat from the final lift HMA pavement application and the pressure of the roller causes the VRAM to migrate up into the voids. Air voids are filled by VRAM, so water doesn’t have space to enter and do damage.
The use of VRAM on your roadway creates an impermeable barrier at the joint that may otherwise deteriorate over time. It fills the voids from the bottom up, keeping water out of the mix. Therefore, creating that solid barrier in between.
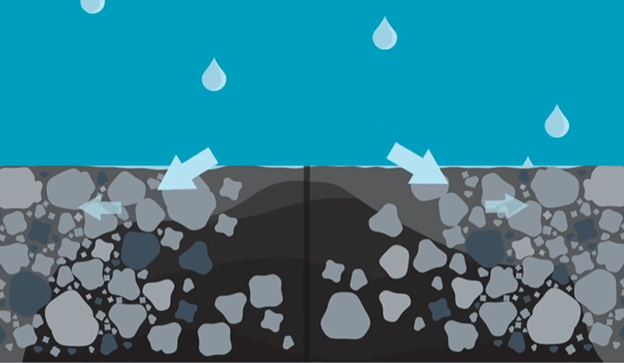
Permeability Measurement Techniques
There are several different techniques and tests to measure the permeability of your road. The most common tests are a falling head field permeameter and a falling head laboratory permeameter.
For a falling head field permeameter, the circumference of the base is sealed using putty. Then weights are placed on top of the permeameter to hold the seal as shown in the left photo below. Water is then poured into the top of the tube until it is filled to the very top. The tube has markings at centimeter intervals from the top to the bottom. The faster the water flows through the pavement, the higher the permeability.

Falling Head Field Permeameter
Falling Head Laboratory Permeameter
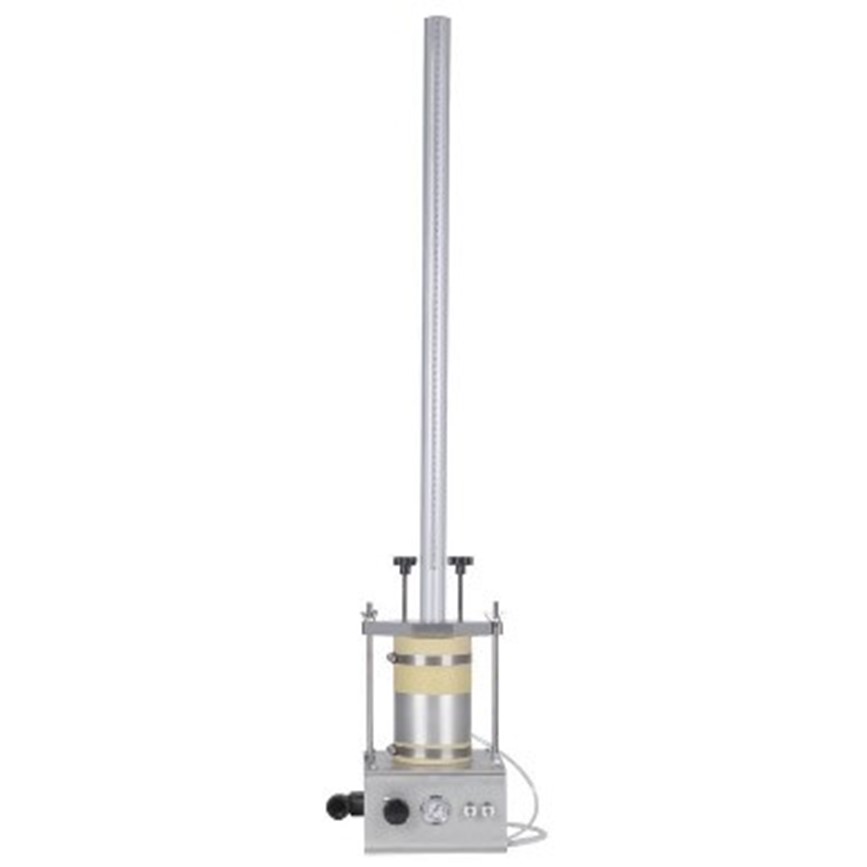
Testing the permeability in the field has pros and cons. It is a non-destructive technique and a convenient measurement tool to use. However, the results measure the water flow vertically and horizontally, which may lead to less representative results of the full pavement layer height permeability and the effect VRAM has on the pavement. This type of test can vary between the different mix types (e.g. fine vs coarse-graded) and has some environmental variables.
Lab testing also has its pros and cons. While a core must be cut from the pavement and transported to the lab for tests, the test results can be more consistent. Benefits include a higher accuracy rate, use of a sealed testing apparatus, and testing in a controlled environment. Lab testing measures vertical flow only and considers permeability for the full height of the core.
VRAM Field vs. Lab Permeability
When tested in the field, VRAM-filled voids in the bottom of the pavement layer are impermeable. However, the water may flow more easily outward or upward in the unfilled air voids near the top of the lift, which would show measurable permeability. Experience in the lab tells us something different.
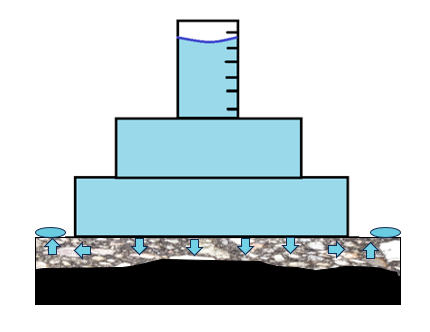
When tested in the lab, a VRAM-treated core will showcase the surface lift is impermeable. This is because horizontal water flow is prohibited by the testing device, and water cannot flow past the VRAM-filled voids. The test shows a more accurate representation of how the water flows through interconnected voids of an untreated mix. This testing method better explains why VRAM is a highly effective treatment to reduce pavement permeability.
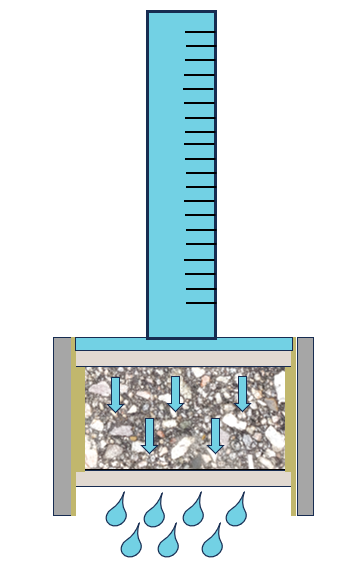
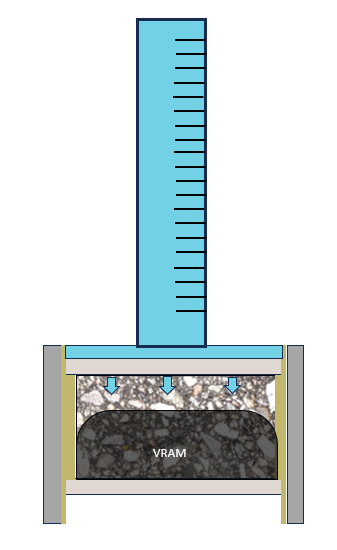
Live Demonstrations of J-Band
Our Product Innovation Engineers Andrew Eicher and Joe Finch recently created live demonstrations that showcase a pavement without J-Band vs. a pavement with J-Band. These demos show how effective a VRAM can be and are a visual representation of how VRAM creates an impermeable barrier compared to an asphalt pavement not treated with VRAM.
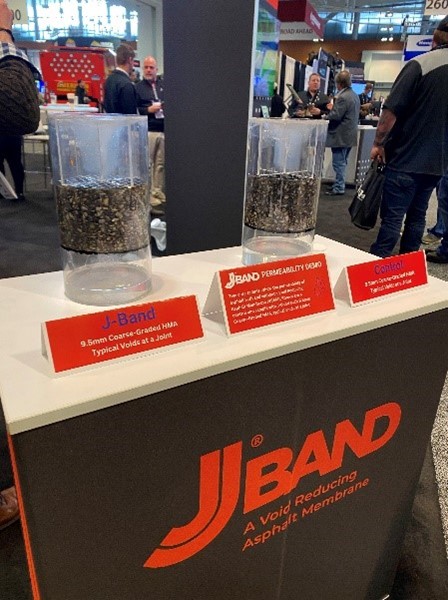
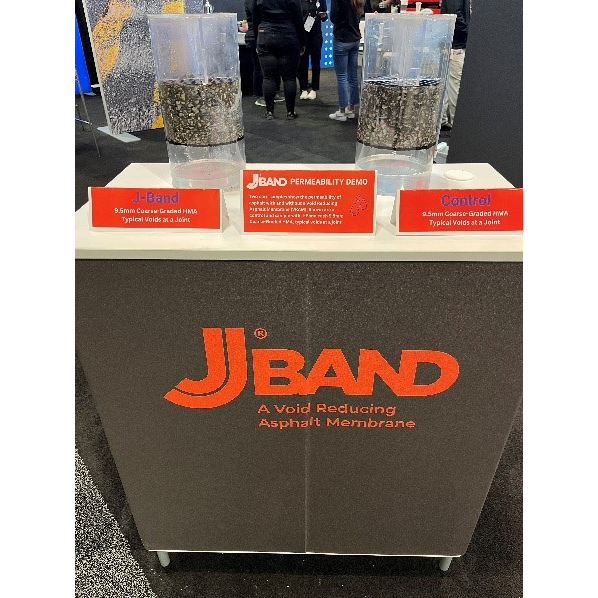
(Time lapse video of water permeability demonstration.)
To look at projects that have incorporated a VRAM during construction and to discover the benefits of longer-lasting roads in terms of cost savings, time efficiency, and safety you can explore our interactive map here.
Editor’s Notes:
J-Band®, CCAP® and T-Bond® are registered trademarks of Asphalt Materials, Inc.
AMIBIND™, AMIBOND™, AMICYCLE™, AMIGUARD™ and AMISEAL™ are trademarks of Asphalt Materials, Inc.
J-Band® was created in the labs of the Heritage Research Group (HRG) and is a product of Asphalt Materials, Inc. (AMI).