In 2023, the National Road Research Alliance (NRRA) issued a call for innovation for preventative roadway maintenance and this project answered: Materials-Based Methods to Improve Rumble Strip Durability.
The team of researchers behind this study began with the following questions: Does the installation of milled rumble strips in new pavement damage the pavement or cause the longitudinal joint to fail faster? If so, could the rumble strip area be treated with a material-based solution to mitigate the damage; and if treated, will the rumble strip maintain its essential safety functionality?
Background
The Federal Highway Administration recommends installing longitudinal rumble strips on two-lane roads for a reduction of roadway departure incidents. Milled centerline rumble strips (CLRS) can provide up to 50% (rural) and 91% (urban) reduction in injury-producing crashes on two-lane roads (source). As a result, transportation agencies are increasingly adding CLRS to highway projects for safety purposes (source).
Inciting Concerns
However, the public as well as transportation engineers have some worries about CLRS implementation. Rumble strips are usually cut over longitudinal paving joints, which are already prone to low density with increased air and water permeability. Furthermore, the milling process itself may compromise the pavement’s integrity. The recessed shape of CLRS also provides reservoirs for water or ice, which could further accelerate damage.
The following concerns are specifically addressed in the NRRA study:
- Nuisance noise (external noise pollution), especially in urban areas, from vehicles inadvertently drifting onto the CLRS or passing other drivers
- Accelerated pavement deterioration on or near CLRS from damage during installation and/or localized distress, such as from water held in the rumble strip grooves
These concerns necessitate further research to understand how to effectively preserve rumble strips while minimizing negative impact to functionality. This project evaluates the impact of material-based methods for improving or enhancing CLRS durability and functionality while maintaining safety, through the use of full-scale field projects.
Project Methodology
Three full-scale, live-traffic projects were built in Wisconsin during the 2023 season using both standard and sinusoidal rumble strip geometries. These three sites included eight test sections, including control sections with no rumble strips or material treatments.
Test sections were constructed with and without CLRS, and with and without the use of material treatments known to improve longitudinal joint durability: Void Reducing Asphalt Membrane (VRAM), Rapid Penetrating Emulsion (RPE) and a combination of the two.
Functionality (noise) testing was completed the same season, and the pavements were core sampled for laboratory investigation (a total of nearly 300 field cores taken from the centerline joints). The project review panel consists of DOT and industry personnel from six NRRA member states. Preliminary results are available now.
Material Treatments
VRAM – Void Reducing Asphalt Membrane
A VRAM is a unique joint treatment that fills pavement air voids from the bottom up, fending off air and water that cause joint deterioration. It is applied at the area of a longitudinal joint just prior to paving as part of the normal hot mix construction process. The hot asphalt and pressure from the rolling operation cause the VRAM to migrate up into the mat. By applying a VRAM below the joint, pavement permeability above the VRAM area reaches zero or near zero. J-Band® is the premier VRAM.
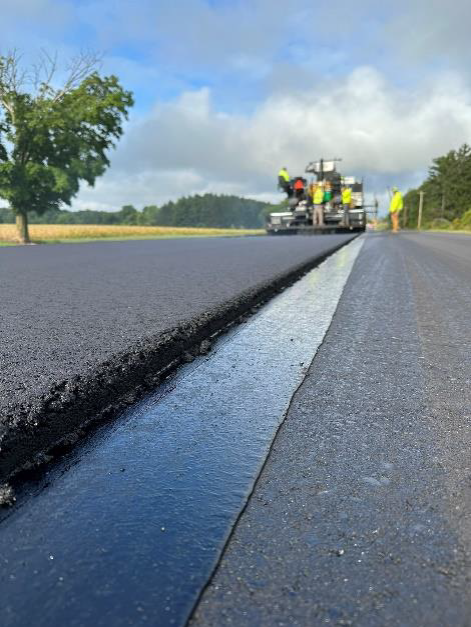
VRAM application, half-covered by the HMA mat, Rock County, WI
RPE – Rapid Penetrating Emulsion
RPE is a specially formulated asphalt emulsion that penetrates quickly and thoroughly into pavement surface-connected air voids. The resulting surface is nearly impermeable to water, and the added asphalt residue creates a lasting, darkened appearance, which may increase striping visibility and promote more rapid snow and ice melt. This study attempts to measure the effect of the added asphalt residue on performance at the joint area, although RPE can be applied across the full width of the pavement, ideally applied soon after paving or within the first 1-2 years of pavement life.
Preliminary Results
The field cores were evaluated in the lab, using a variety of non-destructive and destructive test methods selected based on the expected failure mechanisms of the longitudinal joint. A full description of the test methods and results can be found on the project website here.
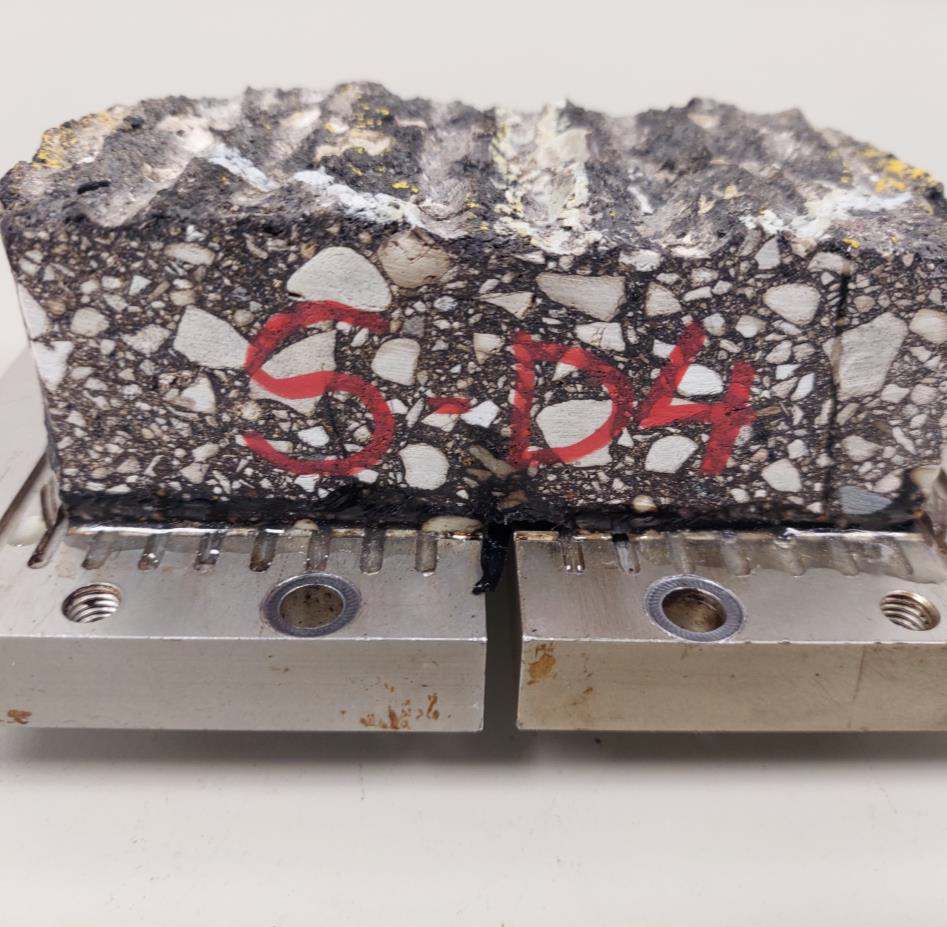
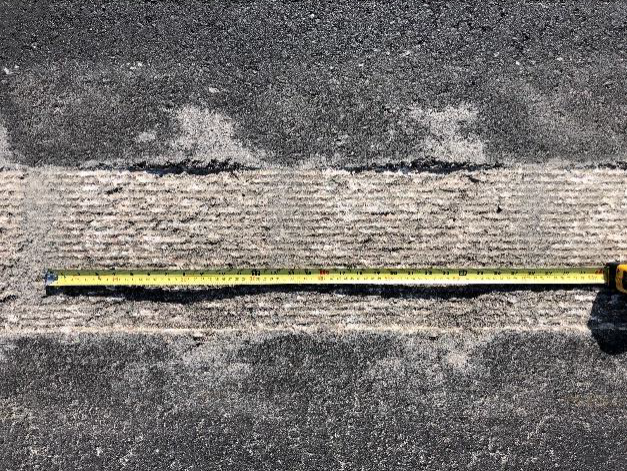
Below are the preliminary key findings identified through testing.
- Cracking behavior is driven by the presence of the longitudinal construction joint, highlighting the importance of constructing a high-quality joint. Milling of rumble strips can influence joint durability as evidenced by an increased crack propagation rate for cores with rumble strips.
- Application of VRAM at the joint is shown to significantly reduce the crack propagation rate with rumble strips, thereby increasing reliability of performance at the joint. RPE is shown to be less effective than VRAM, although the sealing effect of RPE may have long term positive implications that warrant further study.
- VRAM and RPE did not negatively impact the functionality (driver-alerting internal noise) of the rumble strips and may in fact reduce the external nuisance noise generated when vehicles drift onto the rumble strips. This might be useful in more urban environments where noise reduction is a design consideration.
Summary
This study highlights the importance of constructing a high-quality joint to drive performance. Milling of CLRS does appear to increase the air void content at the joint, but evidently not enough to significantly increase water permeability. Durability of the joint is controlled by the presence of the joint, not by the CLRS. Still, CLRS can impact durability, and the use of material treatments can offset these effects and likely increase the performance reliability at the joint.
Rumble strips are installed over already susceptible longitudinal joints. Therefore, the use of materials-based treatments to enhance joint durability is important.
The VRAM treatment addresses the vulnerability below the surface of the mat with an asphalt binder-rich interface, improving joint durability. Both VRAM and RPE treatments are found to minimally impact the driver-alerting qualities of rumble strips (internal noise), so no change to current practices is needed when installing rumble strips.
As the final step to this study, the research team will release a best-practice guideline for pavement owners, using the research findings to inform steps to ensure longevity of rumble strips.
Find the full study with available deliverables here.
This research was sponsored by the National Road Research Alliance (NRRA).
“NRRA is a Pooled Fund with the goal to improve the future sustainability of our roads through research and a commitment to cooperative implementation.”
Principal Investigators:
- Dan Swiertz, PE, Asphalt Materials, Inc.
- Katie DeCarlo, Ph. D., EIT, Heritage Research Group
- Signe Reichelt, PE, Behnke Materials Engineering
Key Takeaways
This project tested the impact of VRAM and RPE treatments on centerline rumble strip durability and functionality and found that longitudinal construction joints are the true weakness beneath rumble strips. While there is no need to change rumble strip installation methods when using these material treatments, the use of a VRAM beneath the longitudinal joint is beneficial to the durability of the pavement structure containing rumble strips.
Laboratory data of centerline cores informed the preliminary conclusions of the researchers. For an exploration of field data, the team behind the VRAM, J-Band®, has gathered project reviews demonstrating J-Band results after many years.
Over 27 states have used a VRAM on their roads as part of the normal hot mix asphalt construction process. With an efficient application process and quick return to traffic (sub 30 minutes), agencies specify a VRAM as a simple material solution to longitudinal joint failure. By preserving the centerline with VRAM, agencies save at least $2 in deferred maintenance and repairs for every $1 they invest.
Click to learn more about the cost-savings and proof behind VRAM.
Editor’s Note:
J-Band®, the premier VRAM, was created in the labs of the Heritage Research Group (HRG) and is a product of Asphalt Materials, Inc. (AMI).