Rumble strips play a critical role in keeping drivers alert and roadways safe. However, they are typically constructed over or near longitudinal joints, the part of the pavement that is already vulnerable to water intrusion and early deterioration. To reinforce rumble strips, their pavement foundation—the longitudinal joint area—needs to be strong.
The answer is a Void Reducing Asphalt Membrane (VRAM), which has been proven to significantly extend the life of longitudinal joints from the bottom up, saving agencies at least $2 for every $1 they invest. VRAM is already widely used to preserve centerline and shoulder rumble strips.
Unlike other joint treatments, VRAM is applied at the location of the future longitudinal joint before HMA paving. Due to the surface course’s heat and the pressure of the rolling operation, the VRAM migrates up into the asphalt mat, filling air voids that allow for destructive water intrusion. The result is a more durable joint area with reduced permeability.
Proof that VRAM Preserves Rumble Strips
J-Band®, the premier VRAM, is used by multiple state DOTs to extend the life of rumble strips. The J-Band team regularly reviews these VRAM projects. The following selection of project reviews demonstrates the preservation power of this innovative treatment.
Project Review: SR-26, Jay County, Indiana
- Owner: Indiana Department of Transportation (INDOT)
- Prime Contractor: Milestone
- VRAM Applicator: Evergreen Roadworks
- Date Constructed: November 2016
- Date Reviewed: February 2024
Summary: This 9-year-old state route project was constructed with a control section (no VRAM), which contrasts the performance of the test sections (with an 18” wide VRAM application). Centerline rumble strips were milled over the longitudinal joint.
The control section joint has 95% cracking ranging from ¼” – ½” wide, whereas the VRAM-treated centerline showed a 1/8” opening on 80% of the project with a ½” on just the first 100’. In 2022, the condition of the control section warranted crack sealing and was double crack sealed in some places in 2023.
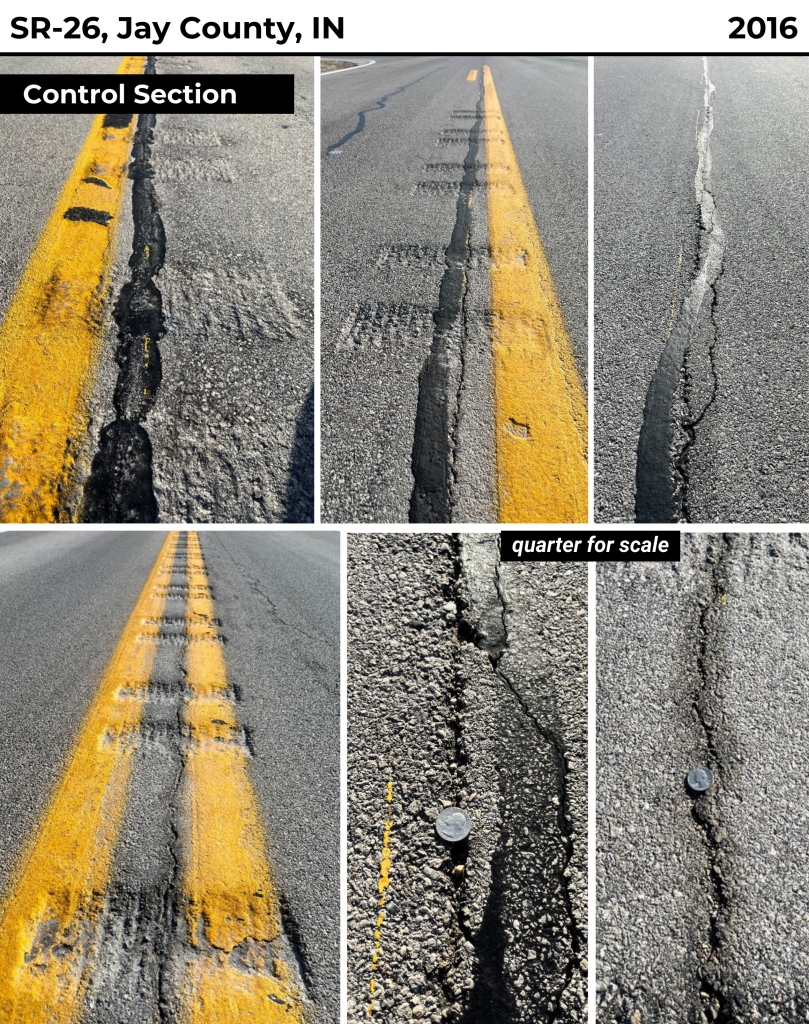
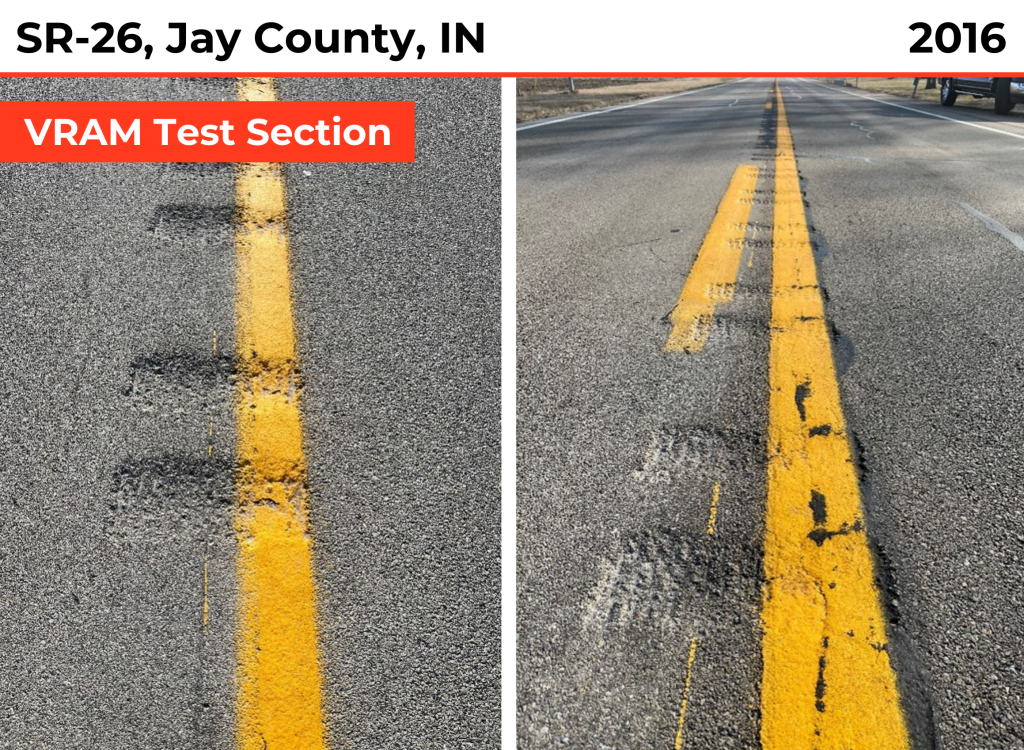
Project Review: US-250, Wayne County, Ohio
- Owner: Ohio Department of Transportation (ODOT)
- Prime Contractor: Kokosing Construction Company, Inc.
- VRAM Applicator: Specialized Construction, Inc. (SCI)
- Date Constructed: August 2017
- Date Reviewed: November 2024
Summary: This 8-year-old, 8-mile test project shows an impressive performance contrast between the control and VRAM test sections on State Route 250. With centerline rumble strips, the control section is 100% cracked from ½” to 1.5” with double and triple parallel cracking along the centerline. Meanwhile, the VRAM section shows a small percentage of longitudinal cracking ranging from ¼” to ½”.
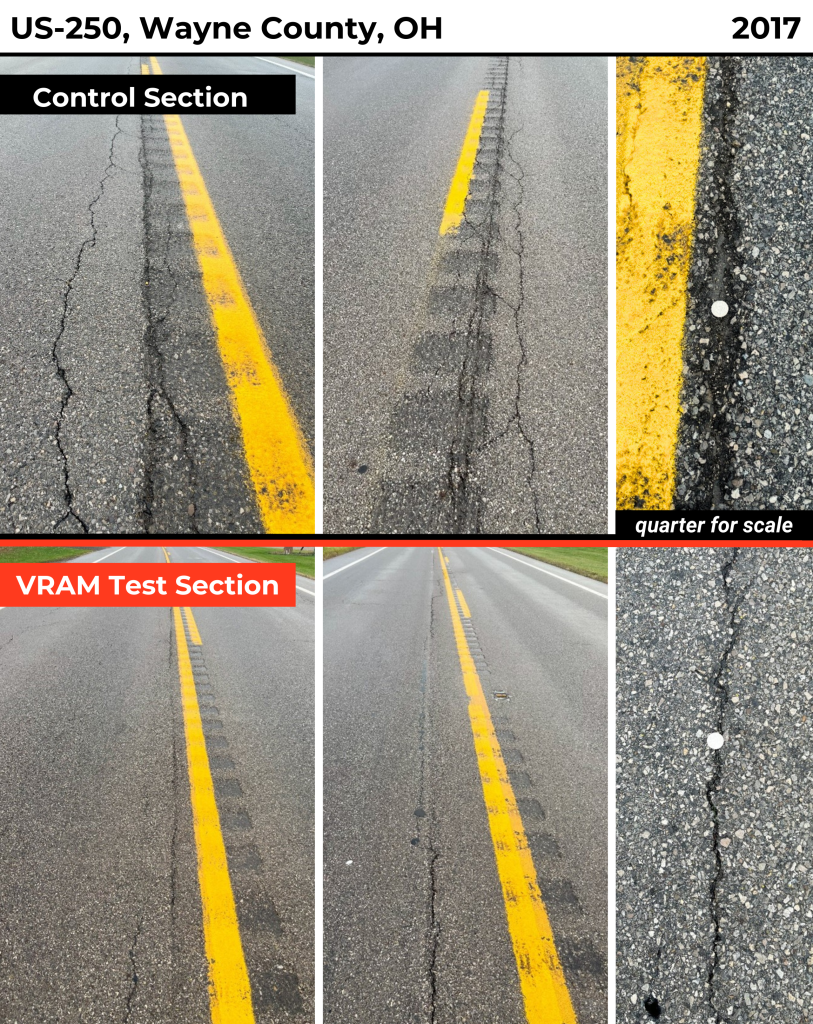
Project Review: IL-148, Williamson County, Illinois
- Owner: Illinois Department of Transportation (IDOT)
- Prime Contractor: ET Simonds
- VRAM Applicator: Evergreen Roadworks
- Date Constructed: June 2018
- Date Reviewed: March 2025
Summary: After 7 years, the centerline rumble strip on this state road is in good condition with help from its VRAM application. Just 20% of the project shows an expected 1/8”-1/4” joint opening for VRAM pavements of this age.
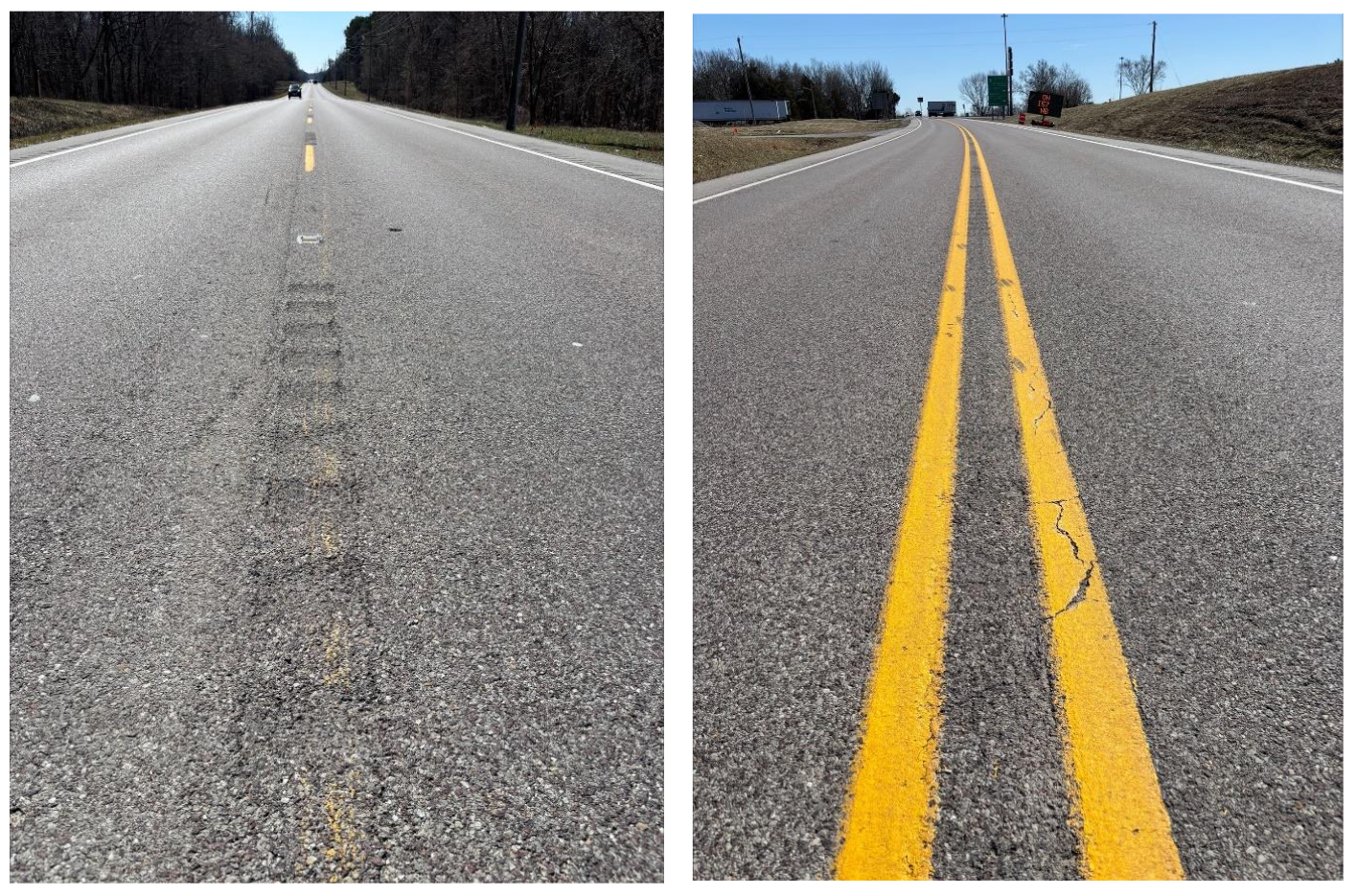
Project Review: US-52, Adams County, Ohio
- Owner: ODOT
- Prime Contractor: Brown County Asphalt
- VRAM Applicator: Specialized Construction, Inc. (SCI)
- Date Constructed: September 2021
- Date Reviewed: February 2025
Summary: This 8.11-mile ODOT project specified centerline rumble strips to be milled 5”-18” away from the longitudinal joint. The joint was treated with a 15” wide band of VRAM. Throughout the project, the centerline shows no signs of cracking.
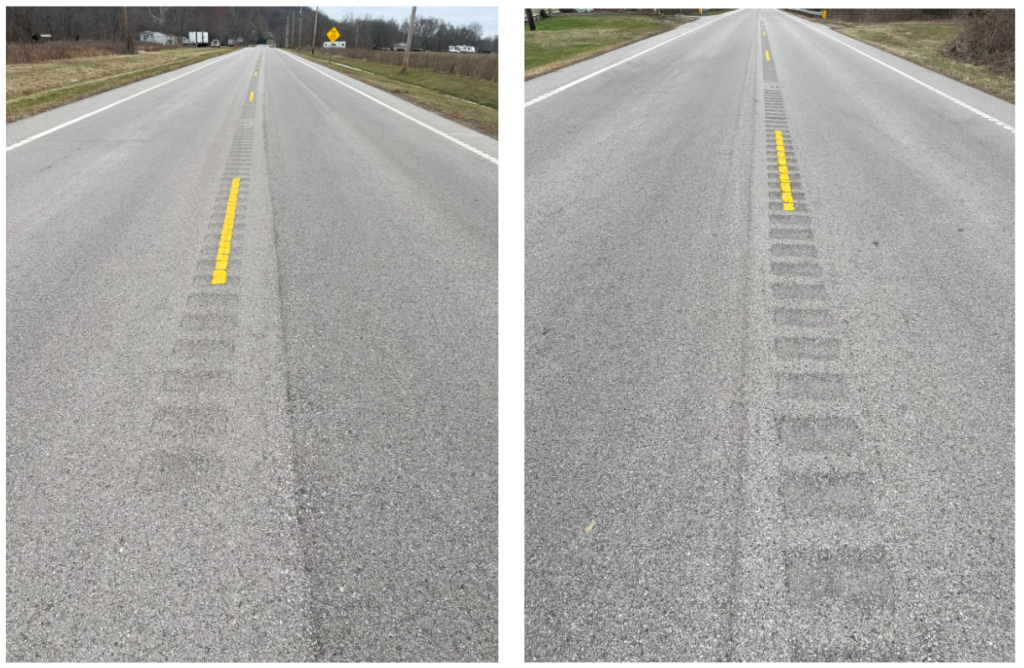
A small section at the end of the VRAM project shows cracking emerging in the rumble strip 18” off centerline where the 15”-wide VRAM band does not reach:
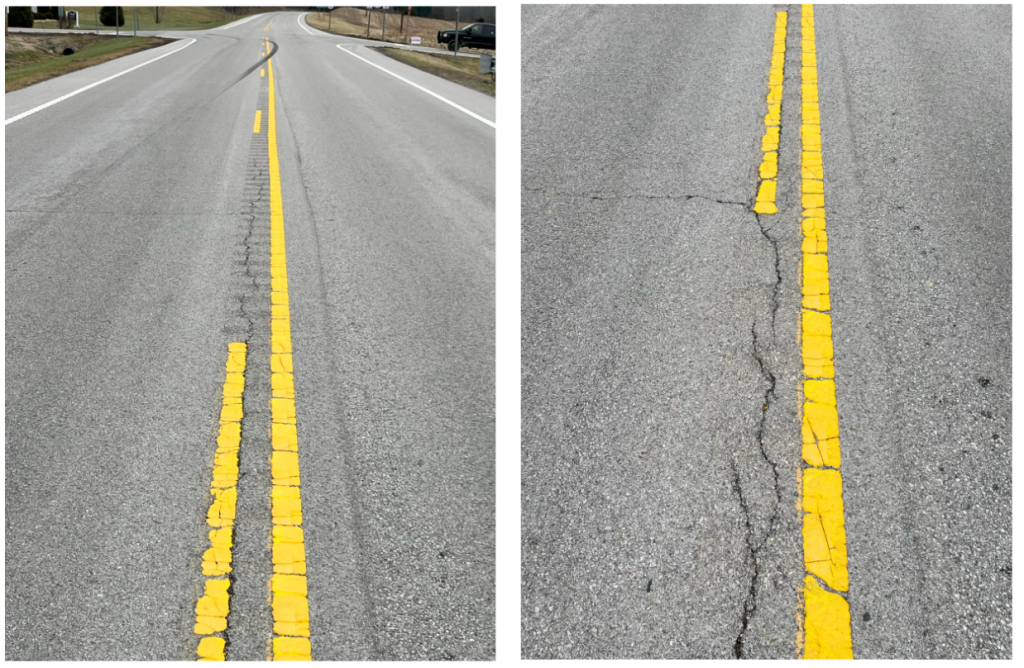
This cracking has emerged outside the reach of the VRAM application.
Project Review: SR-63, Vigo County, Indiana (Terre Haute)
- Owner: INDOT
- Prime Contractor: Milestone
- VRAM Applicator: Evergreen Roadworks
- Date Constructed: July 2021
- Date Reviewed: April 2024
Summary: On SR-63, INDOT specified shoulder rumble strips for motorist safety and reinforced them with a VRAM under the joint and at the centerline. The pavement is in great shape with minor hairline cracking on both centerlines and no cracking on the travel shoulder joints next to the rumble strips.
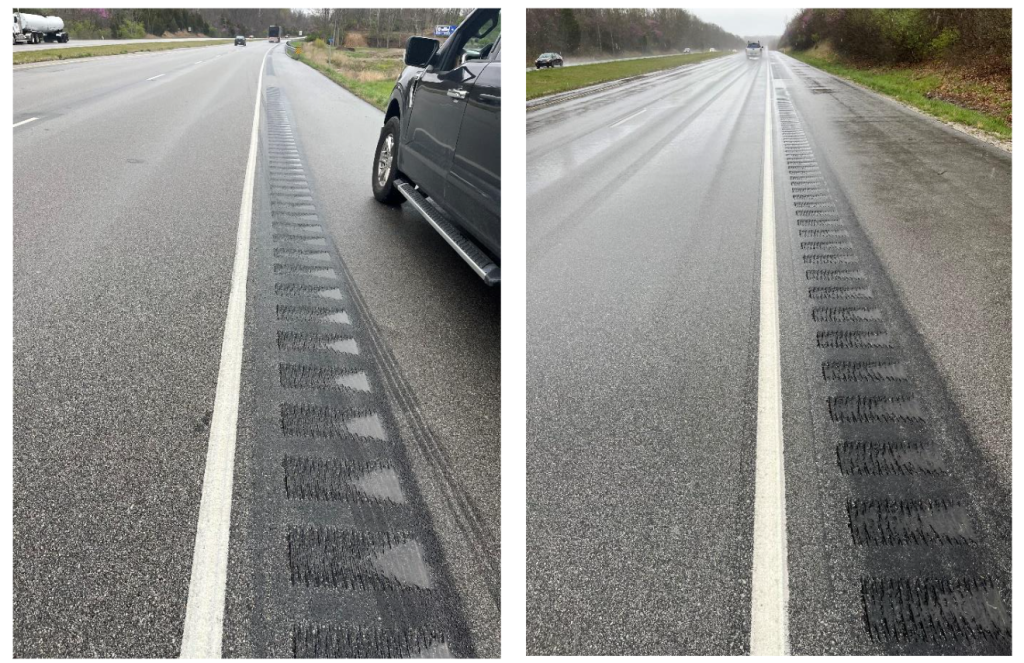
VRAM for Rumble Strips: Research and Studies
National Road Resource Alliance (NRRA)
A NRRA funded research study has investigated the impact rumble strips have on pavement performance. Furthermore, the study tested the use of the VRAM material treatment to mitigate rumble strip damage while maintaining safety functionality.
This research emphasizes that, while milling rumble strips does not significantly impact pavement permeability, the longitudinal joint presents a weakness in that area. Their testing shows that the VRAM treatment improves joint durability without interfering with the driver-alerting quality (internal car noise) of the rumble strips. Read more here.
Transportation Research Board (TRB)
TRB published this paper examining the impact of rumble strips on pavement life and joint durability. The study also determined that VRAM has a positive impact on longitudinal joint performance with and without the presence of rumble strips. VRAM effectively reduced permeability and improved cracking resistance in the tested cores. See the full report here.
Explore more proven results of VRAM treatments in longitudinal joint construction here.
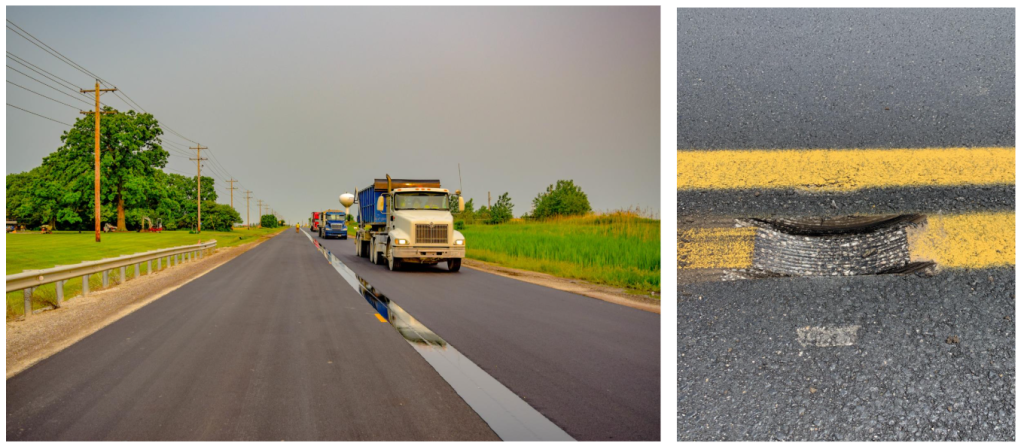
The True Benefit of VRAM: Saving Time, Money and Lives
Over 20 years after the inaugural VRAM application, 27+ states have used VRAM to protect their longitudinal joints as part of the normal HMA construction process.
IDOT was the first to adopt VRAM to its state specifications. In 2021, this TRB Research published study calculated that IDOT has seen a 3-5x return on its investment in VRAM (known as Longitudinal Joint Sealant (LJS) in Illinois) based on its cost at the time of installation.
VRAM continues to save agencies time and money by deferring typical joint maintenance and repair. By preserving rumble strips and keeping workers away from centerline maintenance, VRAM helps keep roads safe for everyone.
Contact our team today to discuss solutions for your road network.
Editor’s Notes:
J-Band® is the premier VRAM and a registered trademark of Asphalt Materials, Inc. J-Band® was created in the labs of the Heritage Research Group (HRG) and is a product of Asphalt Materials, Inc. (AMI).