Is it easy to find roads in poor condition in your county? Several factors can contribute to road deterioration over time, including the size of maintenance budgets, the extent of roadways an agency manages and the timing of preventative efforts. So how can different longitudinal joint construction methods help prevent road deterioration?
Along with disrepair over time of roadway conditions, the biggest culprit of joint deterioration is permeability through water, air and dust intrusion. Most agencies have density requirements for the main portion of the paving mat and the area at the longitudinal joint, with the goal being to close an optimal number of voids to prevent such permeability.
According to a Washington state study done a few years back, if the center of the paving mat is at 7% voids or less, but the joint is at 11% voids, the joint fails five years earlier than the rest of the pavement. The first nine inches on both sides of the joint is the most critical area to pay attention to.
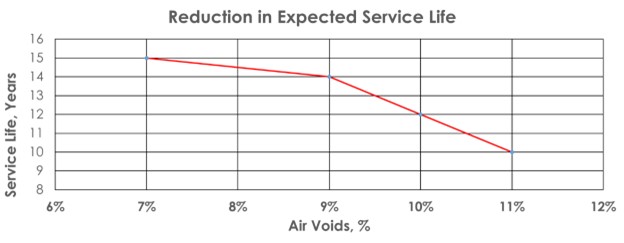
The next time you’re driving after a recent rainfall, look at the longitudinal joint. The drier side of the joint signals the lane that was paved first with the unconfined side. This added a greater probability for water and air intrusion.
Mechanical Methods to Improve Joint Performance
To improve longitudinal joint performance, there are several mechanical methods used to aid in the construction of joints.
- Full Width Paving
- Echelon paving (hot joint)
- Mill and inlay (confined joint)
- Notched wedge joint
- Cutting wheel
- Joint heaters
Full Width Paving
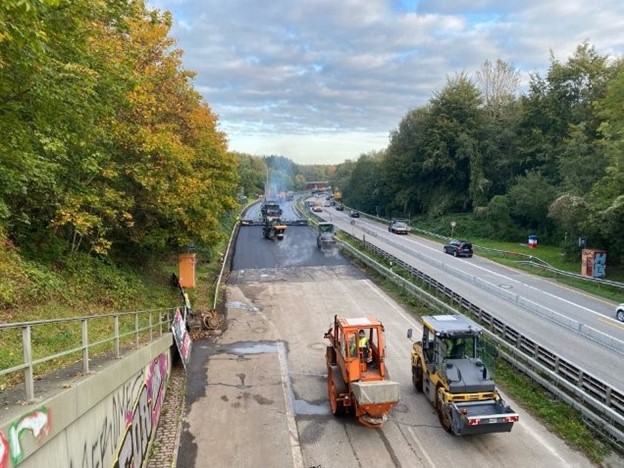
Full width paving helps eliminate all possible joint opportunities and is mostly reserved for brand new construction projects. This method is rare because construction is performed in a single lane closure, to allow uninterrupted traffic access.
Echelon Paving
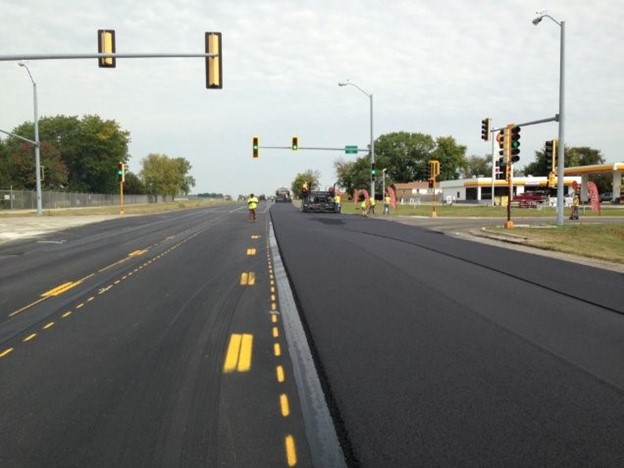
This paving method occurs when two pavers lay asphalt adjacent to each other, removing a longitudinal joint from the pavement by allowing the two laid mats to create a seamless finish. This paving method is as close to paving at full width as you can achieve without causing more significant traffic delays. Additionally, assets must be obtained at the hot mix asphalt plant, paving equipment, labor and trucking which will influence any contractor’s decision in pursuing.
Mill and Inlay
Milling involves grinding down into the upper pavement layer of the existing asphalt to remove any cracks, ruts and other deterioration. Once the first layer is milled, a layer of inlay paving is laid on the top of the milled surface. This method gives you the opportunity to work with a confined longitudinal edge of both sides of the joint. This method is often used on larger traffic volume highways. The key to this operation is to get a dust and moisture-free surface, allowing for a good standing full width tack coat. Once both lanes are completed, a tack coat on the vertical edge of the pavement is a necessity.
Notched Wedge Paving
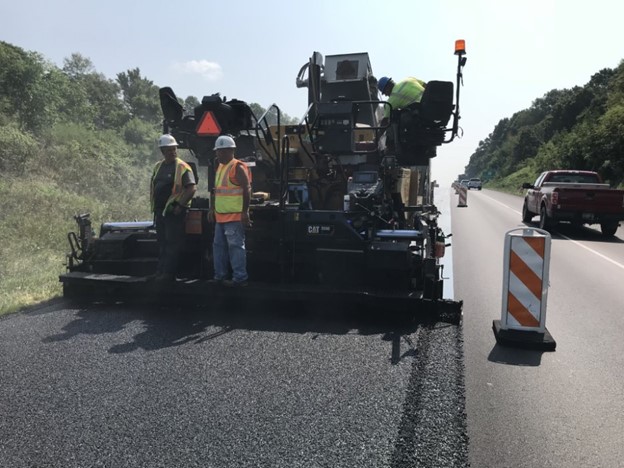
This paving method involves creating a tapered wedge at the longitudinal joint area to transition from an unpaved lane to a paved lane. This method has been gaining popularity in some areas of the U.S. due to notice of improved longitudinal joint density. Notched wedge paving has an additional device or plate that is bolted onto the edge of the screed on the unconfined side of the paver. The wedge acts as a keyway for the second paving pass to tie into it.
Cutting Wheels
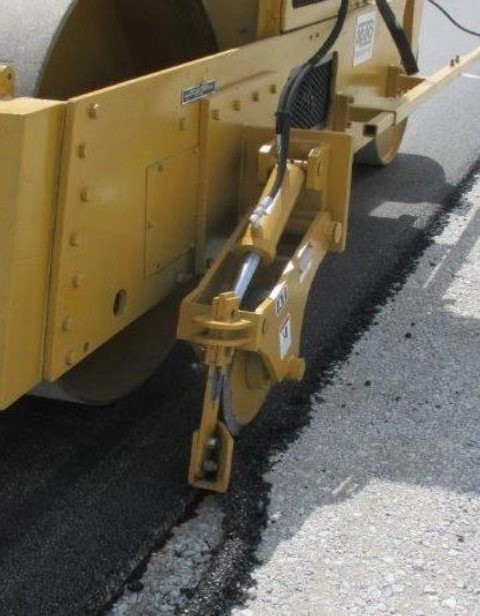
Cutting wheels are tools that have been around for a long while and mainly used in airfield and airport work. A cutting device can be attached to a roller drum, skid steer, grader or loader. It usually trims about three inches off the unconfined edge of the pavement.
Joint Heaters
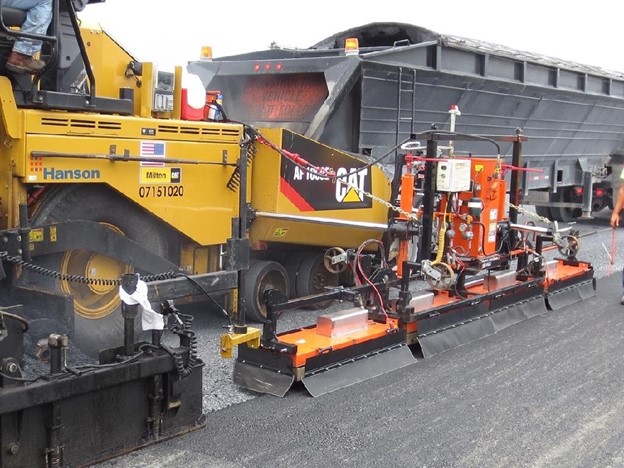
Joint heaters are used in colder climate areas in the U.S. Propane heaters are used on the second pass of paving to re-heat the unconfined edge of the first pass of paving to melt the hot mix asphalt at the joint together. This method follows the concept of echelon paving to work with hot mix asphalt that is hotter than a typical cold joint.
A Materials Solution to Improve Longitudinal Joints
While these joint construction options can help decrease permeability in some ways, there is a materials approach that is proven to decrease voids in pavements and reduce permeability. Asphalt Material’s void reducing asphalt membrane (VRAM) product, J-Band®, is a polymer modified asphalt that fills voids from the bottom up.
J-Band is applied as an 18’’ band before hot mix asphalt paving where the eventual location of the joint will be. By filling voids from the bottom up, air, water and dust particles are trapped outside of the pavement and therefore protecting the joint from permeability. J-Band is the materials solution to prevent longitudinal joint failure.
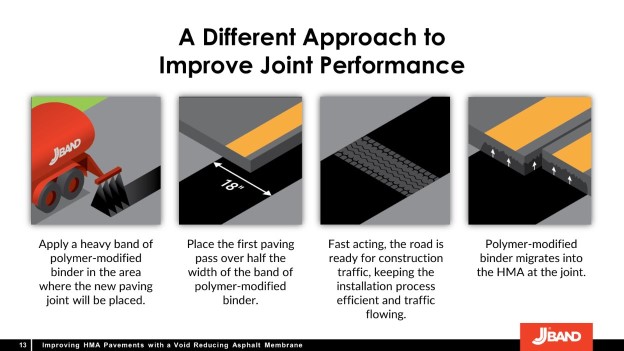
Paving operations with J-Band do not change at all. The first paving pass should cover about half of the band’s width. The roller operators should take care not to cut the edge of their drum directly on the VRAM and should always overhang the joint at least 3-6” or stay away from the joint at least 10” to prevent a stress fracture on the inside edge of the VRAM. It is important to clarify that the rolling pattern you normally use for the mix you are laying should not change.
Interested in learning more about J-Band? You can watch Jim Cunningham, field support manager from Asphalt Materials, and Cullen Hesterberg, operations manager at Evergreen Roadworks talk more about these topics by clicking here.
For a closer look at projects that have incorporated a VRAM during construction and to discover the benefits of longer-lasting roads in terms of cost savings, time efficiency, and safety, you can explore our interactive map here.