The Problem
Miles of existing roads are plagued with longitudinal joint distress, especially if they have milled rumble strips. Centerline joint distress often needs re-paving far sooner than the rest of the pavement. There is a need for a better longitudinal joint repair system.
The Current Practice for Repairing Centerline Joints
This recent NCHRP Synthesis discusses methodologies for wide crack and joint repair, including “crack patching by milling the crack and repairing it with asphalt (also referred to as slot paving or mill and replace)”.
After crack sealing is no longer sufficient, agencies can address severe joint damage by milling out the joint area and filling it with hot mix asphalt (HMA) followed by compaction. The milled area is typically a 2’ wide, 2” deep trench, filled by slot paving.
However, this results in two new joints that will continue to fail faster than the remaining pavement areas. ODOT data* reports getting just 4.3 years of service life from this technique. The limited life extension from trench mill and fill can lead to increased maintenance costs (more crack filling) and repeated worker exposure to dangerous working situations.
Essentially, the common practice of trench mill and fill may not provide the expected joint life extension and can be cost inefficient due to the need for additional repairs in less than 5 years.
Improved Practice for Longitudinal Joint Repair
When longitudinal joints have already failed, VRAM can be added to the post-construction milling and slot paving process to add 3-5 extra years to the life of the joint repair. VRAM, or Void Reducing Asphalt Membrane, is a proven asphalt technology that fills air voids in the mixture, extending the life of the joint area.
The 3-5 years of life extension from VRAM equals savings 4-7x the initial cost for the VRAM used in trench mill and fill. This is because VRAM use under slot paving will reduce the need for maintenance treatments over the life of the inlay.
Proven Technology. Lower-Lifecycle Cost. Enhanced Safety.
One such project was recently completed in Montana, on Highway 200.
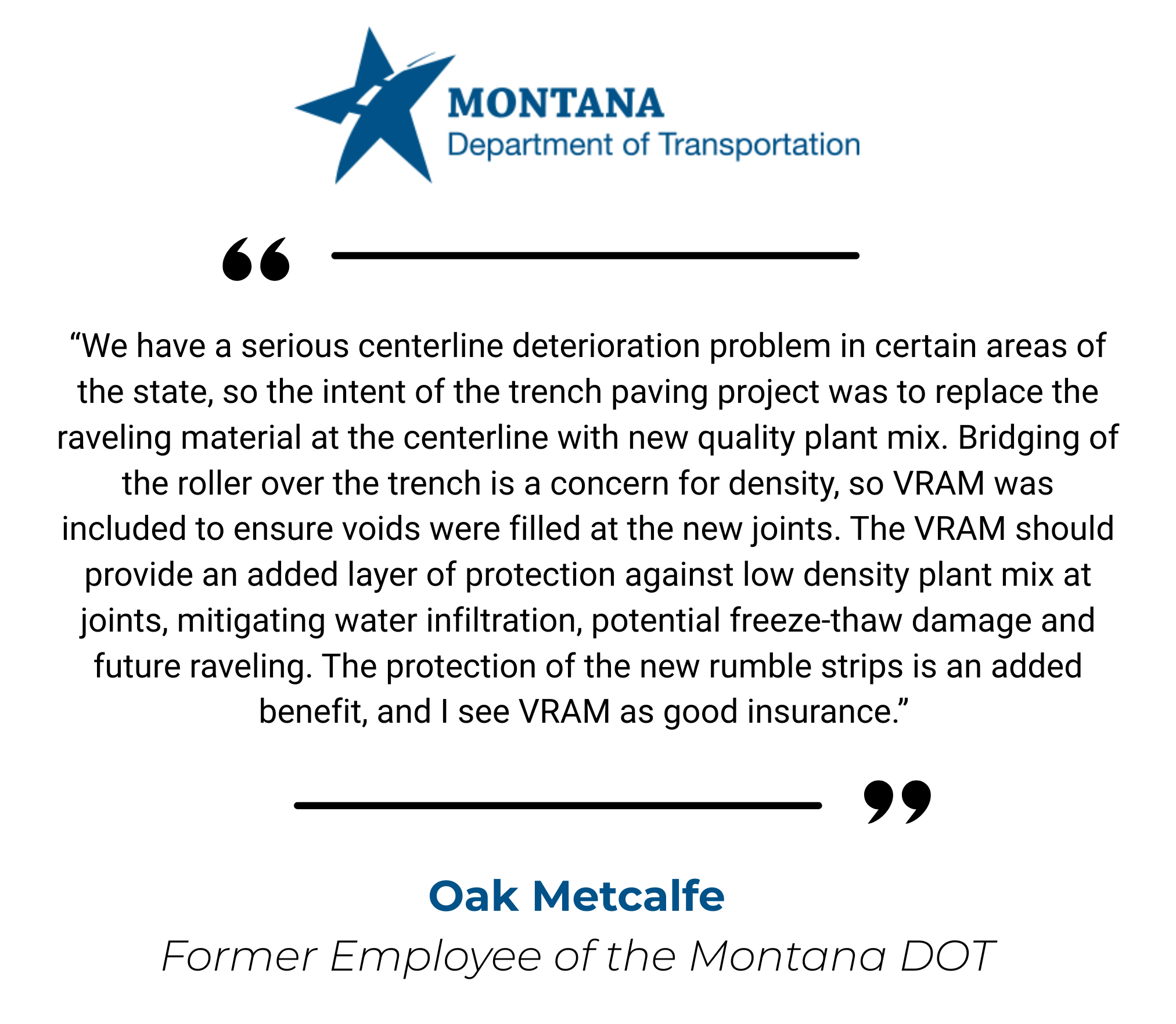
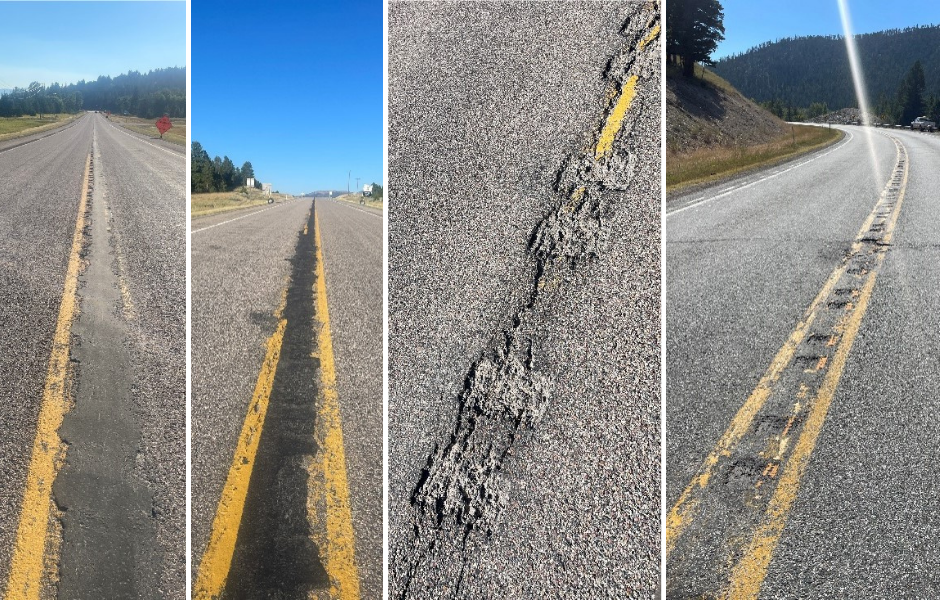
Montana Highway 200 Project Background
The Montana DOT elected to use a trench mill and fill technique to remove and replace the joint area 2’ wide on 85,000 linear feet (~16 miles) of Montana Highway 200 in 2023. This remedial action was due to failure at the joint area, likely accelerated from the 2016 rumble strip installation. VRAM was applied to the width of the trench prior to paving to protect the new HMA joints and rumble strips.
Project Details
- Owner: Montana Department of Transportation (MDT)
- Prime Contractor: Knife River
- VRAM Applicator: Z&Z
- VRAM Supplier: Seneca Petroleum
- Location: Montana Highway 200 in Lewis and Clark County, MT
- Date Constructed: August 14-17, 2023
Slot Paving Construction Summary
For this project, VRAM was applied using a specialized kettle, a Cimline MA4 with 8’ spray bar. Z&Z heated up blocks of VRAM in the kettle while Knife River milled the centerline joint 2’ wide and 1.8” deep to remove and replace the existing rumble strips. VRAM was sprayed at a rate of up to 1.50 lb./ft. and covered the bottom and sides of the trench, for a 28” wide total application.
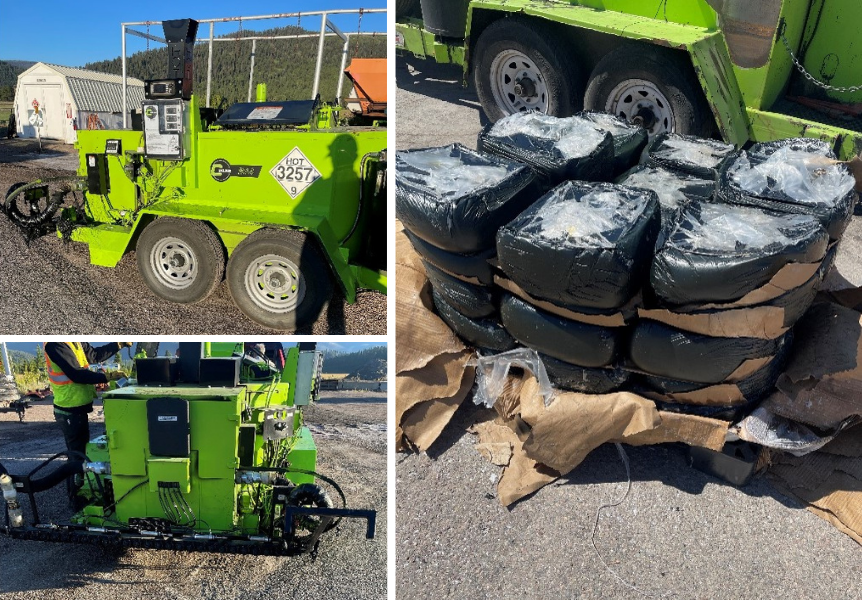
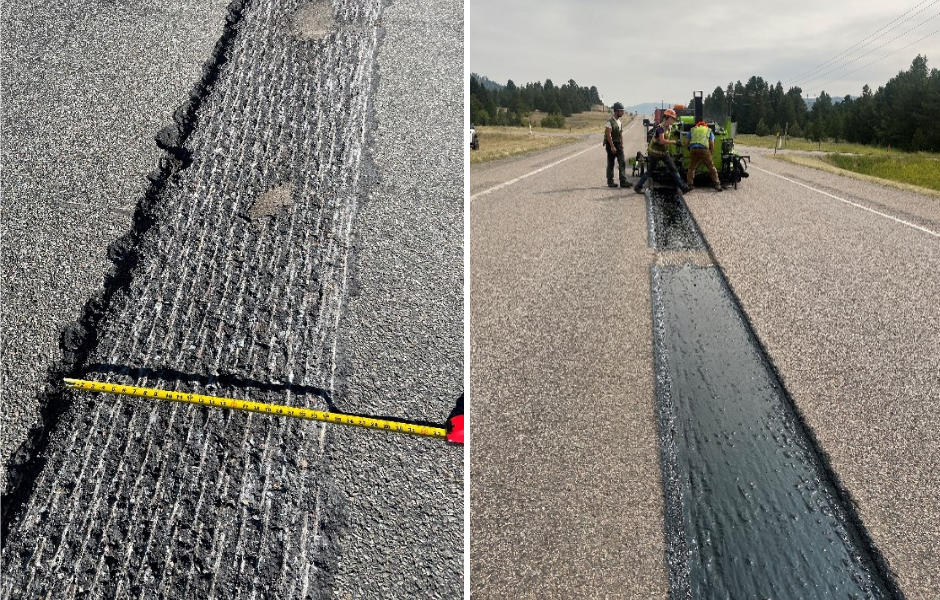
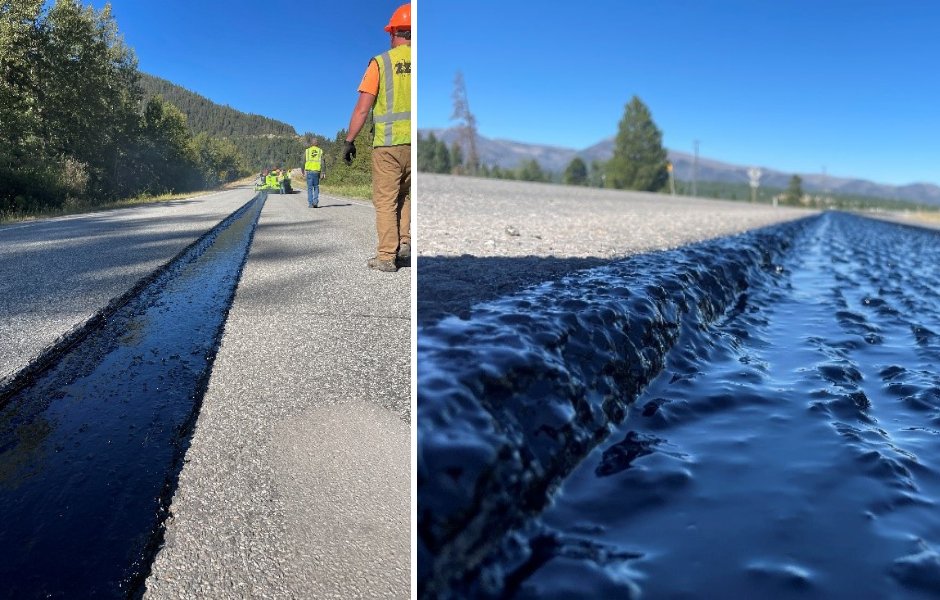
5 minutes after VRAM application, trucks were able to cross the VRAM without any pickup, and paving began shortly after. The mix was laid slightly wider than the trench width, matching the VRAM application. The first steel drum roller was used to compact the edges of the trench and match the existing surface. The second roller used pneumatic rear tires to compact the middle of the trench further without bridging. No flushing was noticed.
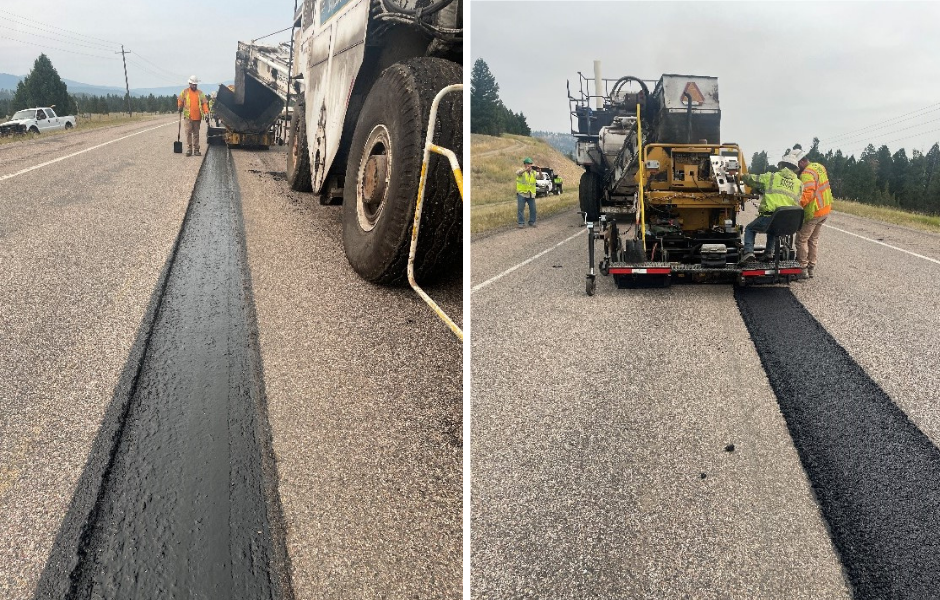
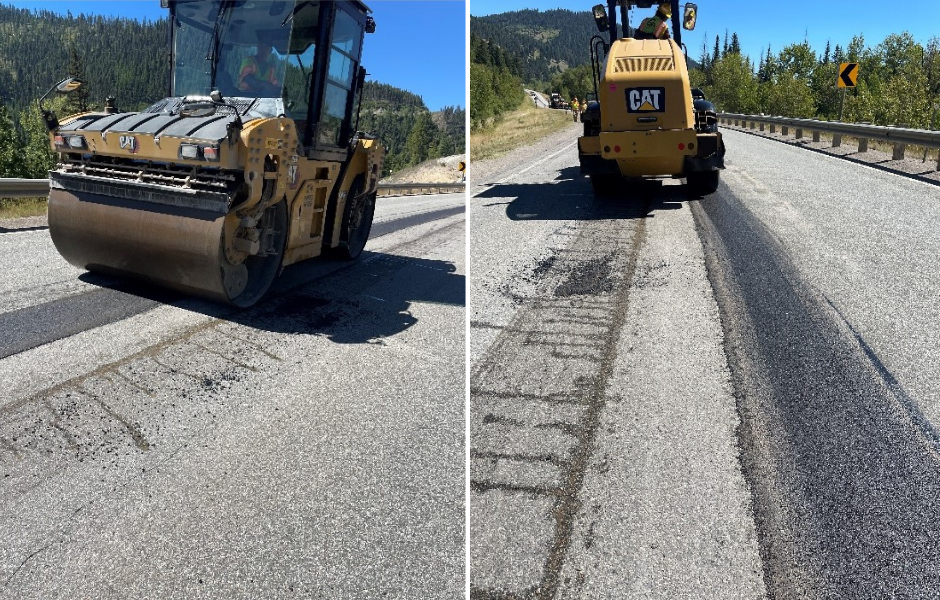
A ~100 ft. control section was sprayed with conventional tack coat instead of VRAM to be used as a comparison of the VRAM to conventional trench paving practices. After paving was complete, new rumble strips were ground into the trenched material. Lastly, the project received a full-width chip seal.
Trench Mill & Fill with VRAM: Results
In summary, centerline joints often fail faster than the rest of the pavement, especially if they contain rumble strips. Milling a trench and filling it with HMA (a.k.a. slot paving) is an effective technique for repairing centerline joints without removing the entire mat. However, this creates 2 new joints, which can also deteriorate quickly.
This is where a VRAM can help. VRAM has repeatedly demonstrated its ability to extend the life of longitudinal joints an additional 3-5 years by filling air voids that allow for destructive water intrusion.
While a VRAM is typically applied at the time of full lane re-paving, slot paving offers an opportunity to install a VRAM under the trench fill, reinforcing the new joints so they last as long as the rest of the new pavement.
The table below uses actual project bid prices from Montana to calculate the savings and corresponding return on investment 5 years after using a VRAM with slot paving. With an anticipated 5 years of extra life due to VRAM, the savings from VRAM twice exceed the initial cost (2.12 times).
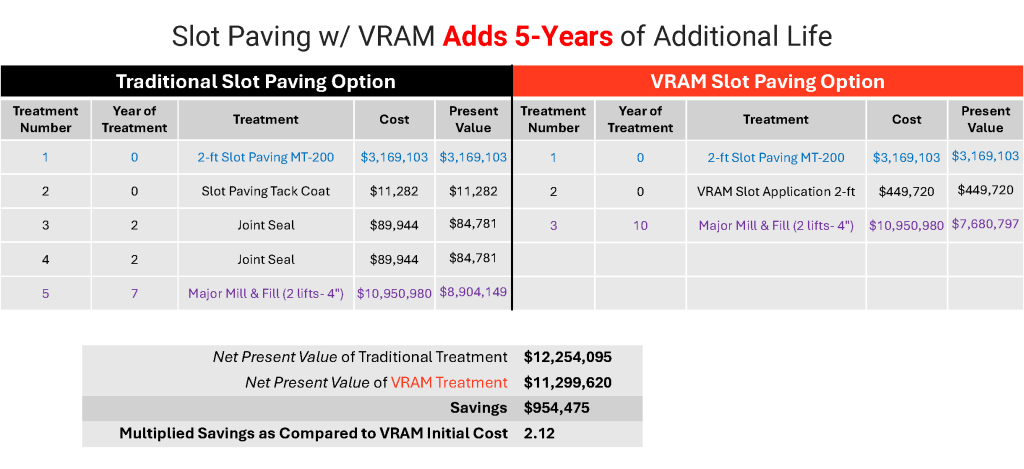
By adding a VRAM to trench mill and fill plans, the life expectancy of the slot paving section can be extended from sub-5 years to 10+ years, at which time the VRAM has provided maintenance savings more than double its cost.
VRAM has proven its ability to save time and money on hundreds of projects across the U.S. (see this project, which lasted over 20 years). For this unique application, it can protect centerline joint repair far beyond the typical design life.
Asphalt Materials, Inc. is a supplier of the premier Void Reducing Asphalt Membrane called J-Band®. You can learn more about our product by clicking here and exploring our interactive map that showcases projects that have utilized J-Band at the time of construction.
To learn more about the use of a VRAM with slot paving, please reach out: jbandinfo@thgrp.com. We’re happy to discuss your upcoming projects.
*Longitudinal Joint Repair Best Practices for the Ohio Department of Transportation, July 2017 Final Report