Written by Naarah Holloway
I-65 Whitestown, Indiana
Road managers know that the longitudinal joint is the first part of the pavement to fail. As a road’s most permeable part, this joint is susceptible to the elements. Air and water work down through this gap causing the joint to deteriorate, crack, and pothole. And when the longitudinal joint fails, the rest of the road soon follows — triggering the need for even more maintenance.
Roads that are reinforced with a Void Reducing Asphalt Membrane (VRAM) have proven to be more economically, socially, and environmentally sustainable than roads without VRAM. VRAM is applied prior to paving under the eventual location of the longitudinal joint and makes roads less vulnerable to damaging environmental elements.
Our team works hard to monitor the performance of VRAM on projects across the 23 states where VRAM projects have occurred. Over the past 20 years, observations show that pavements utilizing VRAM last 3-5 years longer than those not constructed with VRAM.
This is a recent review of a project completed along an 11-mile stretch of I-65 in Whitestown, Indiana. This is a heavily traveled interstate northwest of Indianapolis.
2023 Project Review
- Owner: InDOT Boone County
- Applicator: Road Fabrics Inc.
- Prime Paving Contractor: Rieth-Riley Construction Co. Inc.
- Location: Whitestown, Indiana (Interstate 65)
- Date Constructed: Construction began just after Labor Day 2018 and was completed spring of 2019
- Date Reviewed: 2-14-2023
- Weather Conditions on the Day of Review: 57°F and overcast with light sprinkle at 2:35 p.m.
2023 Project Observations
Asphalt Material’s Field Support Manager Jim Cunningham reviewed the I-65 project, a four-lane interstate in Whitestown, IN. This interstate contains rumble strips on the right shoulder and has reflective pavement markers (RPMs) on the centerline. Detailed below are observations and images from this year’s review.
The VRAM sections still look relatively the same as they did in 2019.
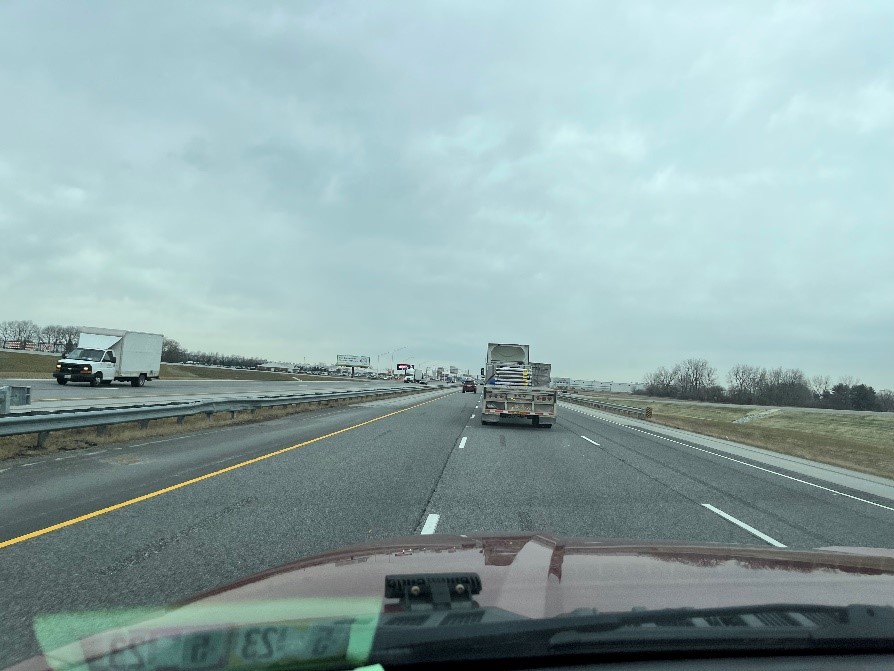
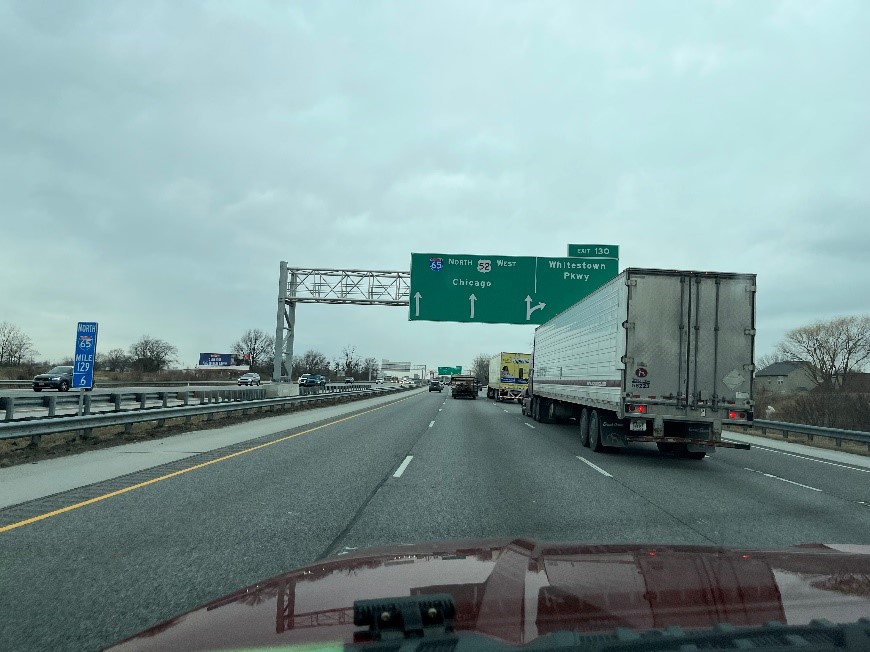
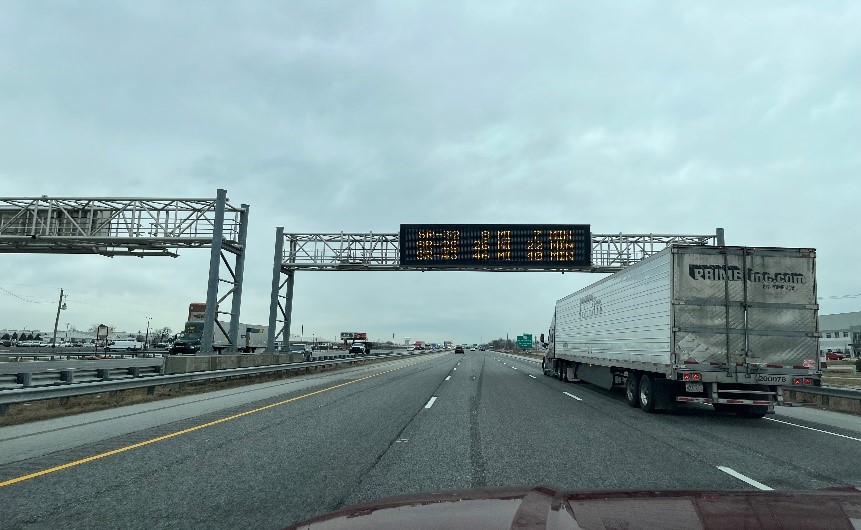
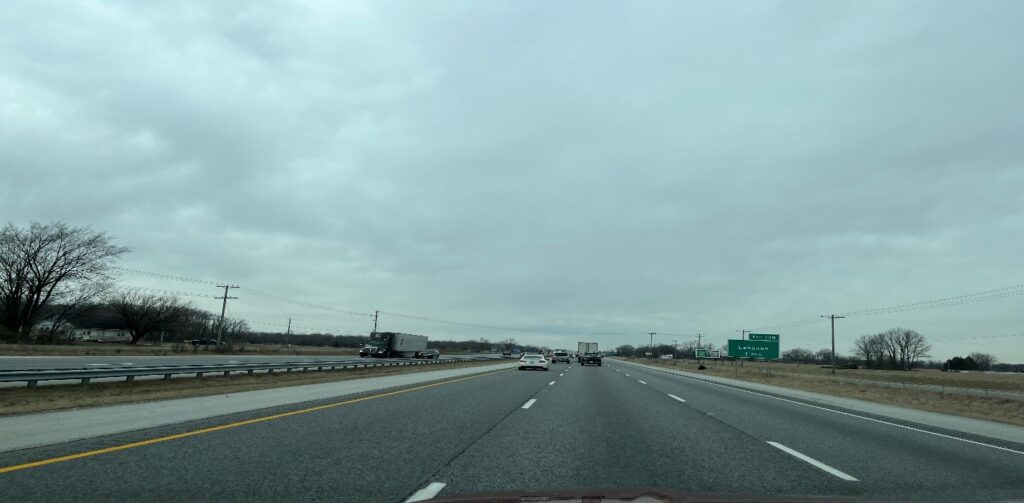
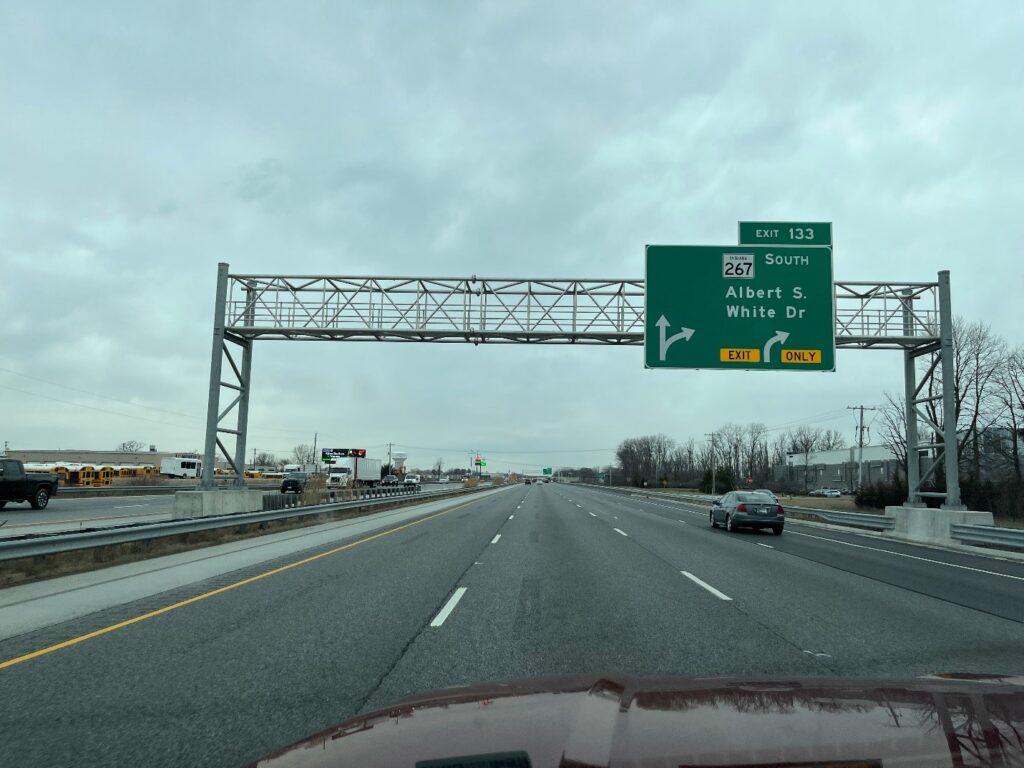
Importance of Protecting the Middle of the Road
When the center of the road deteriorates, other key pieces will follow including rumble strips and RPMs, which makes the centerline the most expensive section of the road. VRAM allows the centerline to last 3-5 years longer, mitigating additional road maintenance needs for longer.
Utilizing a VRAM, such as AMI’s J-Band®, will protect that most important and expensive section of the road. J-Band® has reduced air voids and connected voids in longitudinal joints for more than 20 years. When applying VRAM, it must be under the eventual location of the longitudinal joint. The VRAM under the longitudinal joint allows it to migrate upwards after the hot mix is poured and reduces the permeability.
You can explore our interactive map to see more projects that have utilized VRAM at the time of construction and learn more about how longer-lasting roads saves time, money and lives here.
From the Labs of Heritage Research Group
At Asphalt Materials, we understand that longitudinal joint deterioration has long been a problem for engineers, applicators and the communities we live in. Through collaboration between state transportation agencies, industry experts, and the laboratories at Heritage Research Group, VRAM was developed to help create longer-lasting, safer roads.
Unlike other treatments, VRAM, a Void Reducing Asphalt Membrane significantly reduces air voids in longitudinal joints. J-Band® is Asphalt Materials’ VRAM product. J-Band is a materials approach, applied prior to paving under the eventual location of the longitudinal joint. It migrates upward, fills voids, and reduces permeability as the hot mix is installed on top of it. Since 2002, this approach has improved the performance of centerline joints and entire pavements in more than 23 states.
J-Band® is a product of Asphalt Materials, Inc. and was created in the labs of Heritage Research Group. To learn more about J-Band, or to connect with our team, you can email us at: Marketing@Asphalt-Materials.com.