By applying a Void Reducing Asphalt Membrane (VRAM) at the time of construction to longitudinal joints, local and state Department of Transportations (DOTs) can ensure their roads are less vulnerable to elements, such as water and air. VRAM fills pavement voids in the longitudinal joints and helps create stronger, safer, and more sustainable roads. Over the past 20 years, observations have shown that pavements utilizing VRAM last 3-5 years longer than those not constructed with VRAM.
On July 11, 2023, our specialty products team assisted, applied, and observed a VRAM application in LaGrange County, Indiana. VRAM was sprayed on the centerline joint and shoulder joint on the eastbound lanes of US-20 from SR-5 Shipshewana to 0.35 miles west of SR-9 in LaGrange. Personnel that were present on this job site were two members from Illiana, a paving supervisor from Brooks, and Chad Crosby from Asphalt Materials Inc. (AMI).
Primer: Brook Brothers Driveways
Applicator: Illiana Construction Co.
VRAM Observations
VRAM application began at 8:10 a.m. on the eastbound travel lane heading west. The ambient temperature recorded in the morning was 67 F. While the milled temperature was 77 F, the Illiana team shot the centerline joint first and then proceeded to the shoulder joint.
The band width on this project was targeted at 18” inches wide with a rate of 0.95 lb./ft or a 9” band with a rate of 0.47 lb./ft. The surface course was a 2.0” hot mix asphalt (HMA), with a 70 9.0mm fine grade mix. The total gallons that were applied for the day were 10,560 lbs., applied over 21,348 feet for an average of 0.49 lb./ft.
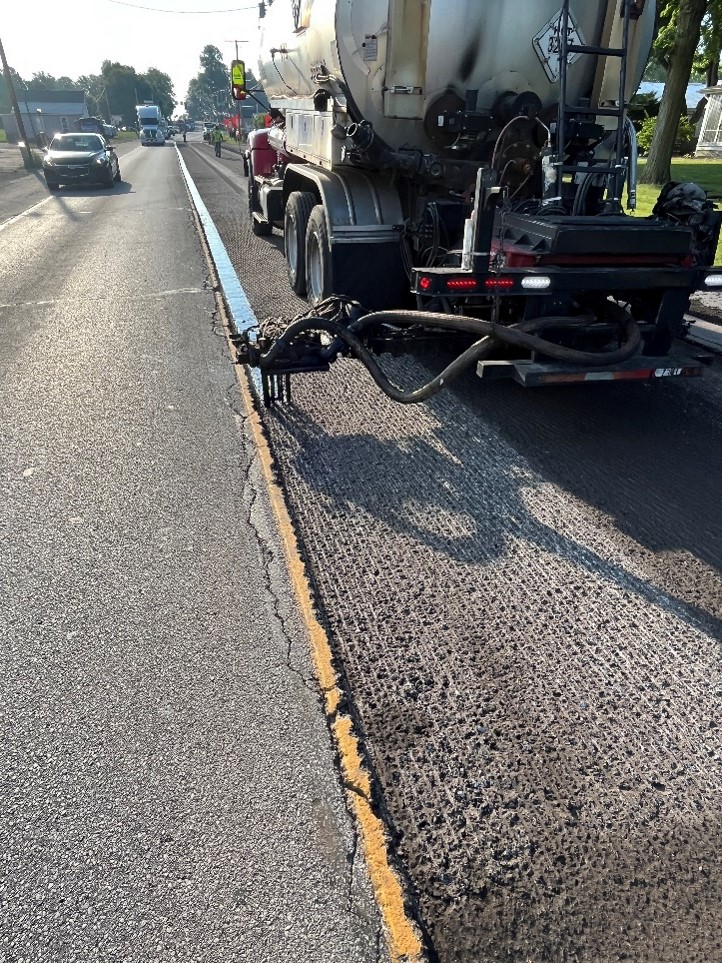
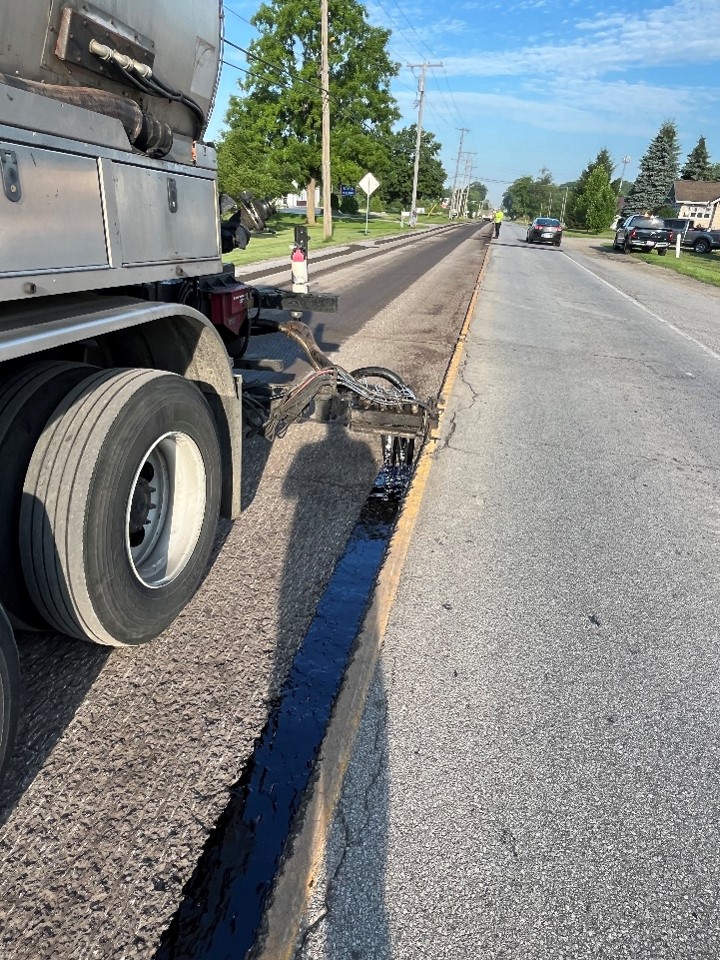
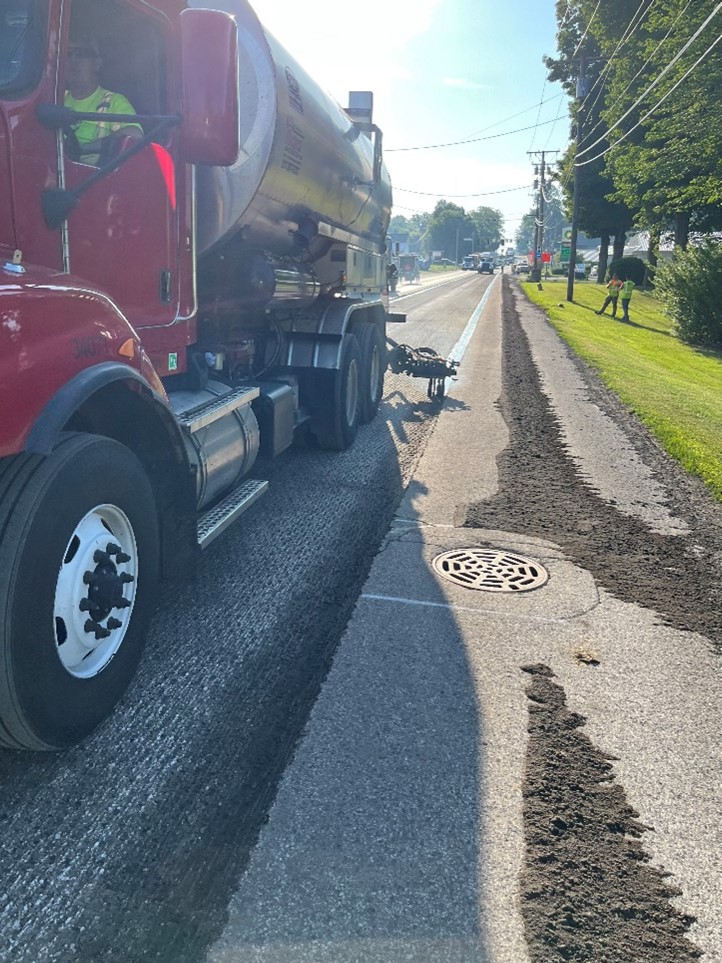
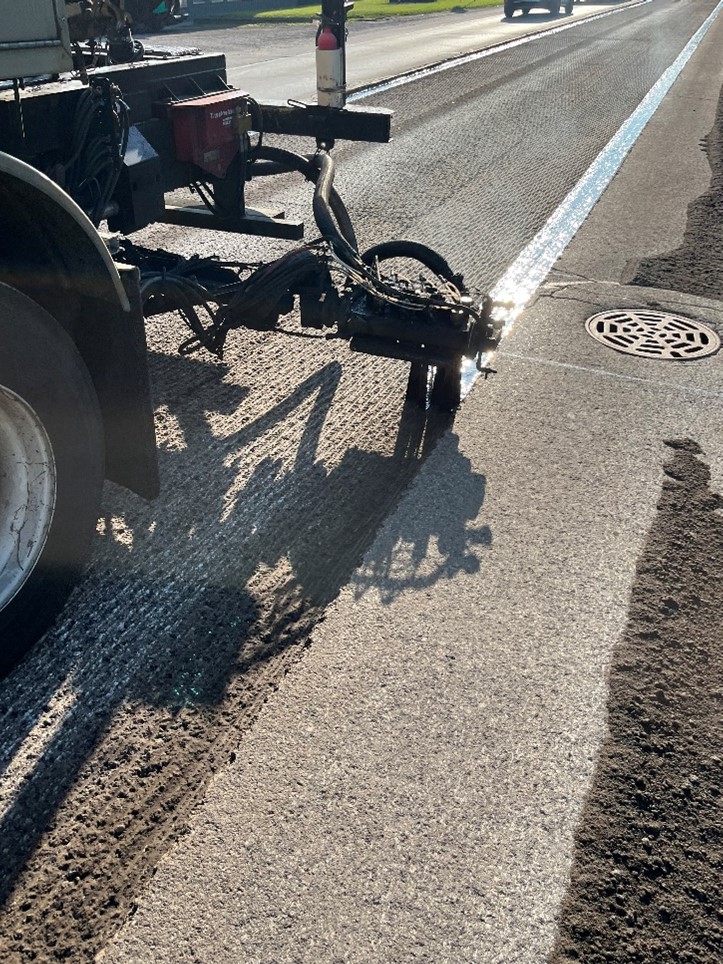
Paving Observations
After the VRAM application, paving began on the same day around 8:40 a.m. The equipment that was used was a Vogele Super 2000 3i paver, Weiler E2850c shuttle buggy, Hamm HD120i steel drum roller, Volvo DD140C steel drum roller, and a DynaPac CC7200 steel drum roller. The ambient temperature in the morning was 69 F and climbed to about 80 F around 11:30 a.m. The weather conditions were sunny with a strong breeze.
The VRAM temperature was around 115 F, with the surface temperature averaging to be 273 F with a ½” migration rate. The HMA was being hauled in from the Brook’s Auburn, Indiana, plant with a round trip of 1.5-2 hours.
The rolling pattern consisted of using two breakdown rollers with the first roller staying around 6 to 8’’ off the centerline joint in a vibratory mode. The second breakdown roller was overhanging the centerline joint also in a vibratory mode. Both breakdown roller drums were overhanging the shoulder joint on their first pass. The rollers worked from high to low making five passes in a vibratory mode. The finish roller worked in a static mode across the mat.
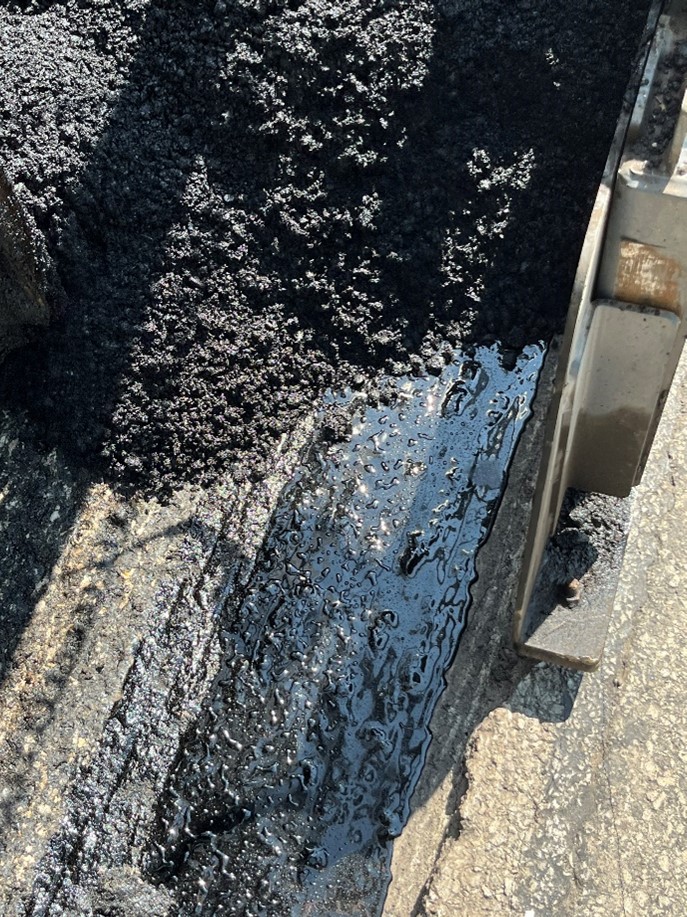
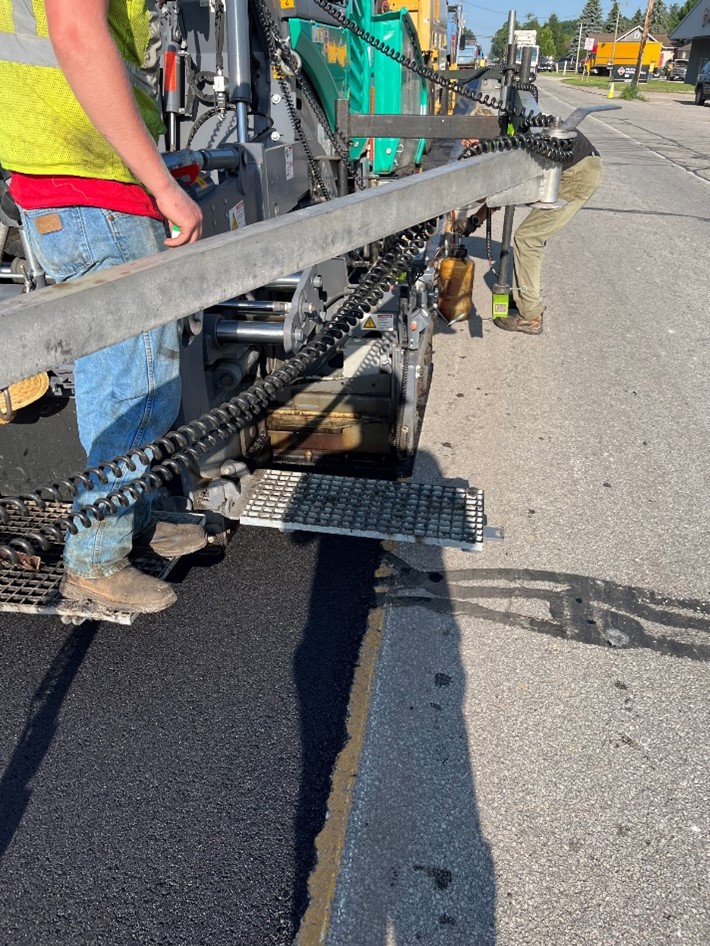
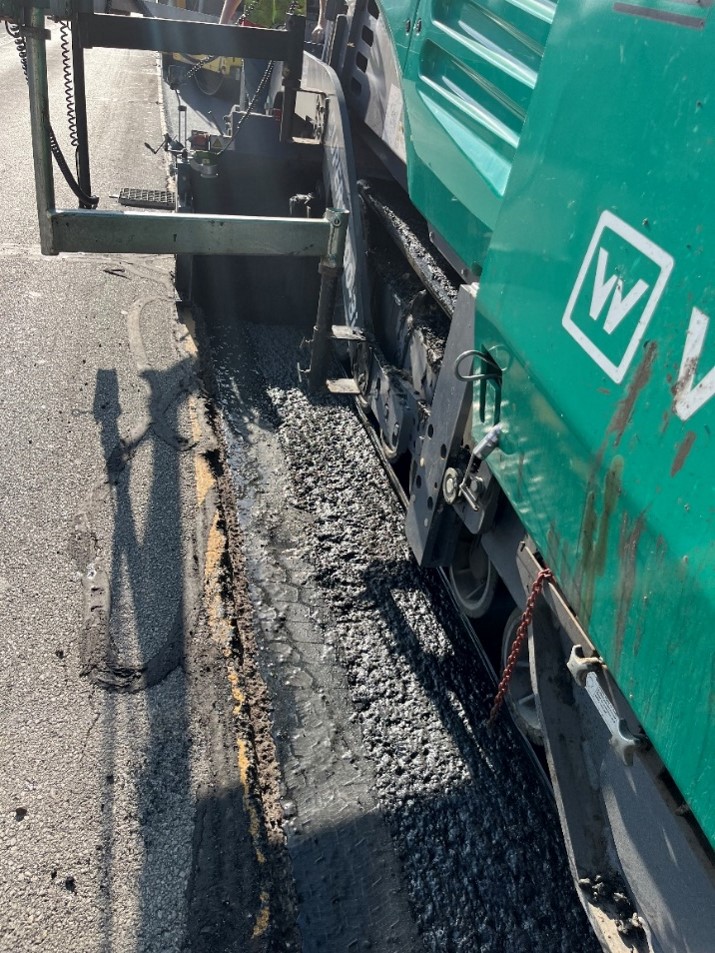
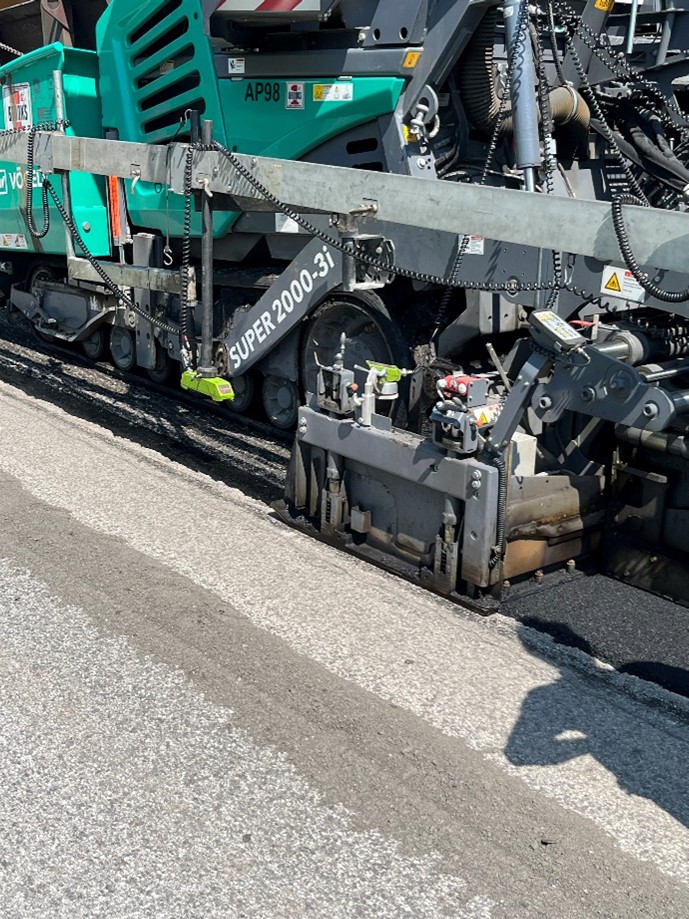
Conclusion
Because VRAM delivers long-term economic, social, and environmental benefits to road construction projects, it is important that we continue to monitor the performance of VRAM on specific projects across the 24 states that have utilized this sustainable technology. Our specialty products team will continue to review projects like this one in LaGrange County to ensure long-term success.
Utilizing a VRAM, like Asphalt Materials Inc.’s J-Band®, protects the most important and most expensive 18″ of your roadways: the centerline. J-Band has a track record of over 20 years and significantly reduces air voids and connected voids in longitudinal joints.
You can explore our interactive map to see more projects that have utilized VRAM at the time of construction and learn more about how longer-lasting roads saves time, money and lives here.