Asphalt Material’s Latest Innovation.
Anyone who travels knows the importance of a smooth, safe drive—which is why cracks and potholes can ruin a journey. These obstacles can be caused by issues below the exterior, but applying the right formula to the surface of a road can have a much deeper impact.
Pavement Joints. Where the Damage Begins.
Drivers will recognize the cracks that surface on longitudinal joints, the areas where two lanes of pavement meet. Those joints tend to have a lower density and higher permeability due to the presence of tiny air voids in the pavement. When left untreated, those small areas of weakness can cause big problems. Water can seep past the surface to permeate the voids, causing pavement degradation over time through stripping (when water separates asphalt binder from the surface of aggregates). Freeze-thaw cycles may accelerate pavement degradation.
Various solutions are available to address the issues that come with low density, high permeability pavements. Most commonly, a fog seal is applied to asphalt after paving to keep water out. The layer of sealant covers the road, but the deeper issue remains.
“The asphalt film left on the surface when you have a fog seal reduces the macrotexture of the road,” commented Dave Henderson, Vice President of Specialty Products at Asphalt Materials, Inc. (AMI). With reduced macrotexture comes reduced friction, which can cause safety concerns for drivers. The connection between rubber tires and a road’s macrotexture ensures a safe grip when cars turn or come to a stop. In addition, when a highway lacks macrotexture, there can be added expenses incurred because thermoplastic traffic markings will wear off sooner. Sealants will not address the voids below the surface, since sealants are a coating the underlying air voids remain, and the overall pavement’s lifespan will not be extended.
Innovation and The Heritage Research Group
If cracks begin to appear in the road, one costly option is to remove and replace the pavement. Bill Pine, Quality Control Director at Heritage Construction + Materials (HC+M), described the need for a more sustainable alternative. “We asked in the early 2000s what can be done to pavements to reduce permeability and keep air and water out,” he remembered. Heritage Research Group rose to the challenge: pavers needed something that would go deeper into the pavement than the typical fog seals that had been in use for decades.
Originally developed for highway applications, Rapid Penetrating Emulsion (RPE) was created to extend pavement life. A critical element of RPE is its ability to rapidly penetrate into a surface. Surface tension, the property that allows water to fill a glass above its rim, was key to formulating a product that could penetrate deep into the asphalt and get drivers back on the road more quickly and safely.
“The formula behind RPE allows it to break surface tension—that’s the reason the liquid can move into and through smaller, interconnected voids within the pavement. It moves down into and below the surface of the road,” said Andrew Eicher, Specialty Products Research Engineer.
The penetrating nature of the emulsion is important because it carries additional residue, asphalt into the voids and therefore filling the voids and reducing permeability. Andrew began working with Heritage Research Group in 2016 when RPE was in its early stages of development. Since then, he has focused on optimizing the product not just for specified longitudinal joints but for potential full-width applications as well. “We’re doing a lot of upfront testing on various pavements to make sure they’re good full-width candidates,” Andrew said, “and make sure we’re able to monitor all the surface and pavement characteristics before and after the application.”
Case study: Rumble strips.
Rumble strips milled at center lines and edge lines are becoming more and more common across the country as a proven strategy for improving driver safety. Their presence, though, can accelerate typical pavement degradation. Using a traditional fog joint to strengthen rumble strips reduces the pavement’s macrotexture by pooling in rumble strips and creating a film over the road. This reduction in macrotexture spells trouble for traffic: the thermoplastic stripes used to mark lanes cannot adhere to the pavement without macrotexture on the surface of the road. Both joint degradation and detached striping pose a serious risk to the driving public. Striping is also very expensive to install and equally expensive to replace.
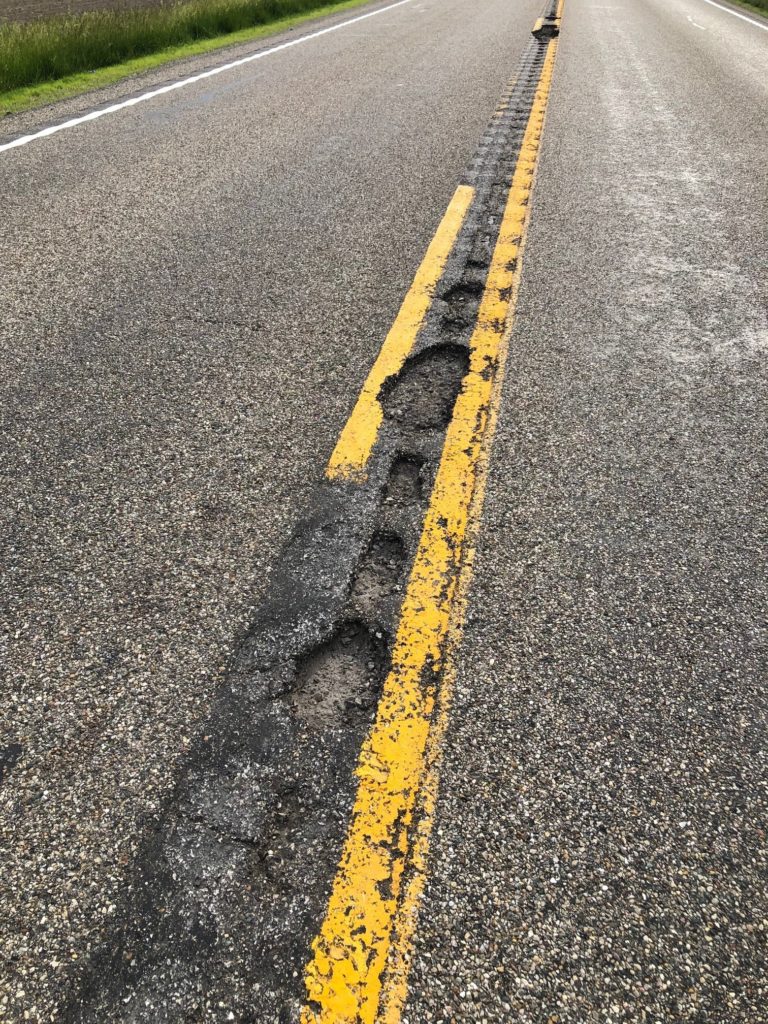
By utilizing RPE for rumble strips, roads and drivers can receive the best of both worlds. The emulsion penetrates deep into the pavement, filling the air voids that traditional fog seals simply cover over. For vulnerable areas like rumble strips, the effect of a penetrating emulsion treatment is a longer pavement life with less time and fewer resources dedicated to patching—or repaving—the road. RPE’s protection, though, doesn’t compromise the macrotexture of the rumble strips, which are milled for texture. Because a penetrating emulsion goes into the pavement instead of sitting on top of the pavement, thermoplastic striping can adhere better to treated areas, ensuring longer-lasting roads for the traveling public.
“Every pavement is different,” said Bill. “The permeability of a longitudinal joint is variable from one end of the job to the other. And the same can be said about a full-width pavement, regardless of where it is. RPE will do a great job immediately when you apply it of telling you where you don’t have density and where you do.” When applied over a low density, high permeability area, RPE will absorb into the pavement like water through a sieve. In fact, the rate of penetration is higher with RPE than with water.
After RPE penetrates a road and cures, access to air voids for harmful moisture and oxidation is cut off. “Just improving the life of the road and reducing the maintenance cycle is a form of pavement preservation,” commented Todd Thomas, Technical Director of Specialty Products at AMI. “Exposure to water and air over time is going to age a pavement or diminish its durability. RPE is reducing that effect.”
What‘s Next: AMIGUARD™ a Rapidly Penetrating Emulsion
AMIGUARD™ has been in development for more than two decades through collaborations at Asphalt Materials, Heritage Construction + Materials, and Heritage Research Group. During this time, the chemical package has been refined to perform well on multiple pavement types and under a variety of conditions. In fact, both centerline joints and full-width applications in various Indiana counties have already demonstrated durability compared to non-treated roads. In Hendricks County, County Road 200E showed a 95% reduction in permeability when treated with RPE, which should translate to years of additional road life.
AMIGUARD™ is AMI’s line of RPE products that are already developed or are in development. As AMI works to bring AMIGUARD™ to additional roads across the Midwest, opportunities to help roads as both a preventative and as a remedial application seem very promising. One area of current interest is as a treatment on rumble strips.
“Measurements are essential at this point,” Mr. Pine added. “As we proceed to the commercialization stage, we’ll continue to learn more as we tailor the application process.” Validating results both in the lab and in the field has been a priority for the AMIGUARD™ team, whose research includes testing the emulsions’ absorption in asphalt and how much compressed air can pass through RPE-treated asphalt cores.
As careful research and monitoring continue to drive AMI’s innovations, AMIGUARD™ is emerging as the next chapter in the story of creating longer-lasting safer roads that began in 1956.
If you’re interested in learning more about AMIGUARD™ or using it in a project, contact Vice President of Specialty Products Dave Henderson at specialtyproducts@thgrp.com.
J-Band® and CCAP ® are registered trademarks of Asphalt Materials, Inc. AMIBIND™, AMIBOND™, AMICYCLE™, AMIGUARD™, AMISEAL™ are trademarks of Asphalt Materials, Inc.