What if you could reduce transportation-related pollution and build a more resilient and sustainable transportation system that will benefit and protect communities?
What if you could help accelerate the adoption of innovative infrastructure technologies in 2022? What if you could protect travelers and communities from safety risks?
What if you could invest in a proven innovation that helps to meet the challenge of the present and will modernize your transportation system of the future for decades to come. Would you invest in it?
If you had access to a proven technology that protects the centerline joints of your roads, AND creates a return on investment of 3 to 5 times its cost . . . would you use it?
In 2022, most state and municipal organizations will be confronted with these challenges. In 2022, there will be new questions and directions to consider as well. So what should you do?
The Federal DOT will provide most of this direction, or guidance, as a precursor to funding from the IIJA, or the Infrastructure Investment and Jobs Act. The following are some examples of this direction.
- Build more resilient and sustainable transportation systems to benefit and protect communities
- Improve the state of our infrastructure, enhance resiliency, and expand to new projects that are beneficial to all communities
Safety
- Provide long-term benefits for residents, travelers and workers
- Improve the resilience of infrastructure
- Advance a sustainable transportation system
- Prioritize worker safety in work zones
Innovation
- Foster breakthrough discoveries and the deployment of innovative pavement technologies
- Experimentation: Identify new ideas, new innovation, and new possibilities
- Accelerate the adoption of innovation and technologies
How Can Agencies Achieve These Objectives?
Through our long history serving the asphalt industry, we understand that longitudinal joint cracking has long been a problem for not just engineers and applicators, but the communities they live in. Thanks to collaboration between state transportation agencies, industry experts at Asphalt Materials, Inc., and the leading-edge laboratories at Heritage Research Group, it’s easier than ever to preserve your investment.
J-Band® sets the standard as a Void Reducing Asphalt Membrane (VRAM). Unlike other treatments, it significantly reduces air voids in longitudinal joints from the bottom. J-Band is a materials approach and is applied prior to paving under the eventual location of the longitudinal joint. It migrates upward as the hot mix is installed on top of it. This not only extends the life of the joint, but improves the performance of the entire pavement.
When pavements last longer, time, money and lives are saved. When roads last longer, they are more resilient and sustainable. When pavements last longer, many of the objectives outlined above can also be achieved.
We have 20 years of experience with a technology that has been proven to save time, money and lives. How much money? An investment in protecting the longitudinal joint helps roads last up to 5 years longer and typically delivers a return on investment of 3 to 5 times its cost.
What is VRAM Technology?
The year 2021 was another important year for VRAM, as we added several states to the list of those with VRAM experience. It is now 21 states and The District of Columbia. The year 2021 was also important from the perspective of how well roads constructed with VRAM continue to perform. Since 2002 VRAM treated roads continue to be longer-lasting, safer and more economical that roads that are not utilizing VRAM at the time of construction.
We are reviewing a number of different case studies of VRAM treated roads across our network.
Protect The Longitudinal Joint. Protect The Entire Road.
Road managers know that the longitudinal joint is the first part of the pavement to fail. As a road’s most permeable part, this joint is susceptible to the elements. Air and water work down through this gap causing the joint to deteriorate, crack and pothole. And when the longitudinal joint fails, the rest of the road soon follows—triggering the need for even more maintenance.
By filling a substantial portion of the voids at the longitudinal joint with a Void Reducing Asphalt Membrane (VRAM), you are able to reduce permeability in this most critical area. As the following project will show, when you place VRAM under the hot mix asphalt at time of construction, you are protecting your investment for years to come. It’s down. It’s done! You can focus on the next set of new construction projects without having to worry about repeated repair and maintenance events along the longitudinal joint. Utilizing a lifecycle cost analysis shows the investment in VRAM helps roads last up to 5 years longer and delivers a return on investment of 3 to 5 times its cost.
Owner: ODOT
Applicator: SCI
Prime: Gerken
Location: US-6 and SR-191 Williams County, Edgerton Ohio
Date Constructed: 2018
Date Reviewed: 11/15/2021
Weather Conditions Day of Review: Sunny and Cold
The control section had visible cracking through the crack seal of 1/2” while the test section showed no visible cracks.
No Snow Plow Damage was observed.
No Rumble Strips were installed.
Raised Pavement Markers were installed.
If there is a Control Section on the project without VRAM how is it performing? Yes, the control section has cracking throughout with a width of 1/2”-5/8”, noticeable through sealant.
Other Project Observations such as Raveling or Flushing: No raveling or flushing is observed.
Has the project received any maintenance work including crack sealing or patching? Yes, the entire project has been cracked sealed. VRAM portion performing excellent (there was no need to seal this portion) for three years old with no signs of cracking.
Scope: Control: SR49 (Mile marker 3) to CR6 (Mile marker 5.02)
Test: CR6 (Mile marker 5.02) to CR8 (Mile marker 7.22)
Control: CR8 (Mile marker 7.22) to US127 (Mile marker 13.79)
Asphalt Materials’ Reviewer: Chad Crosby
Other Project Reviews
By reviewing other projects, you will see that these results are consistent with the results we have experienced over the past 20 years. We believe investing in VRAM at the time of construction can help state and local DOTs achieve many strategic objectives during 2022 and beyond. Contact us to learn more about specifications of VRAM, to conduct a webinar for your team or for insight into how best you and your team can utilize the Lifecycle Cost Calculator by emailing us at Marketing@Asphalt-Materials.com.
Test Section Centerline Exposed (no visible cracking)

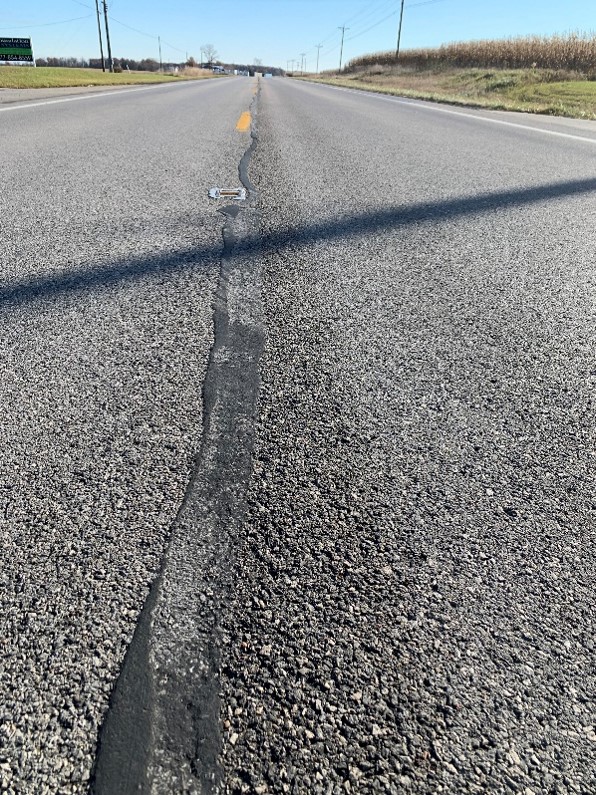
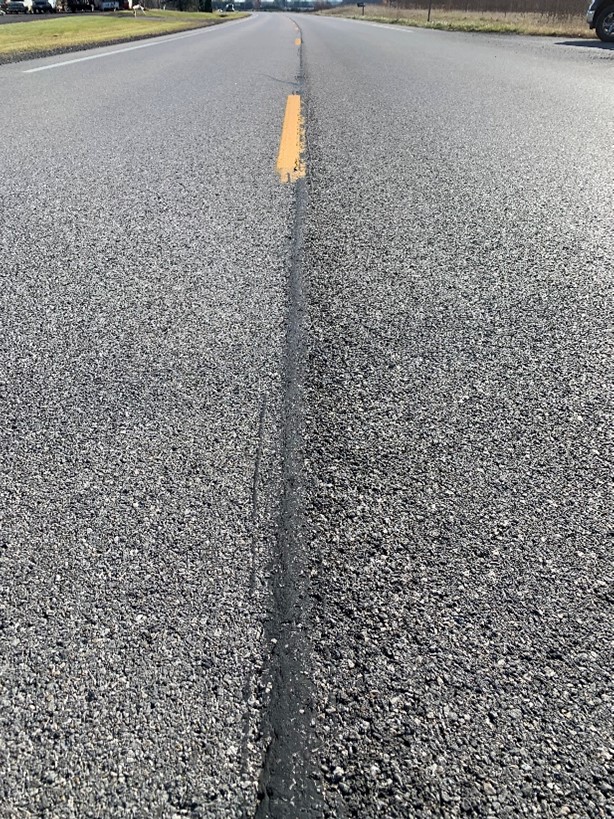
Control Section in Village Limits (not sealed)
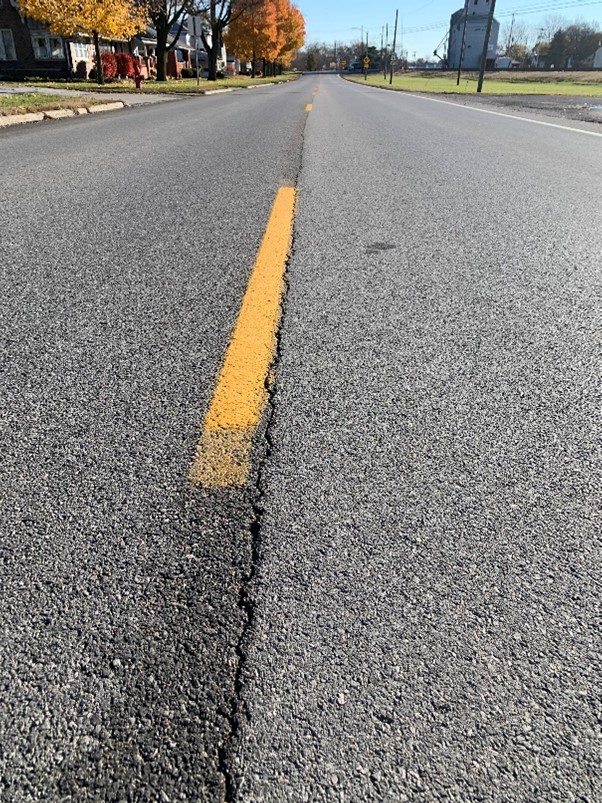
Control Section Centerline Seam Crack Sealed after cracking (noticeable even with sealing)
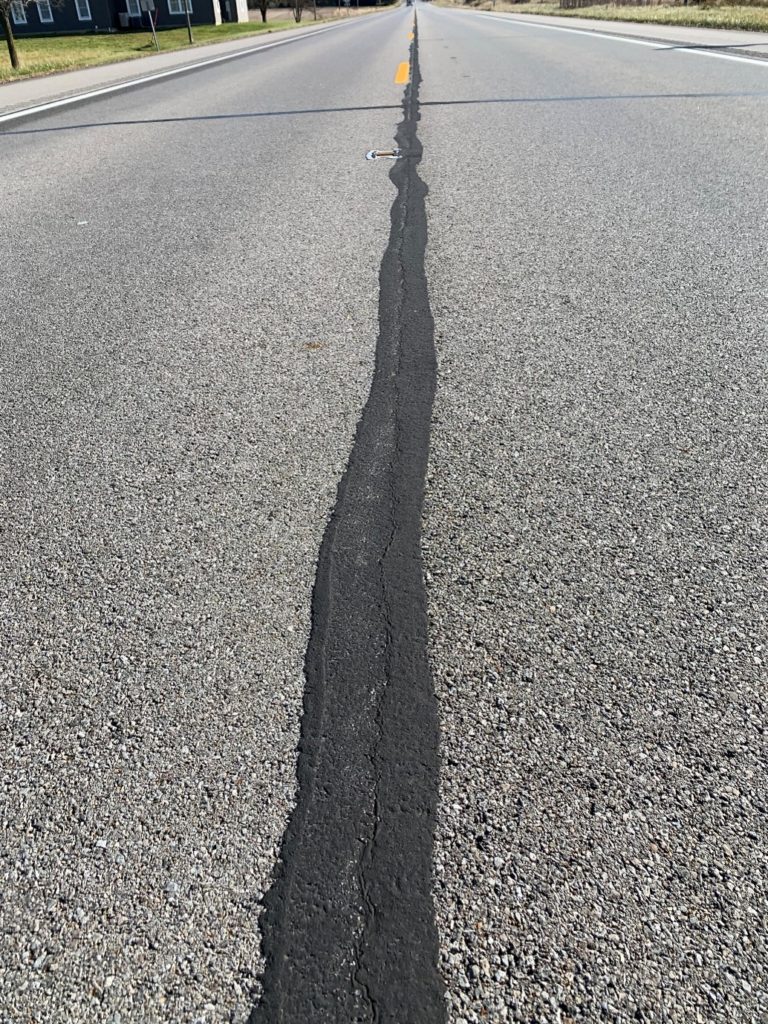
Other Pictures Showing 4+ Year Old Projects (VRAM vs Control)
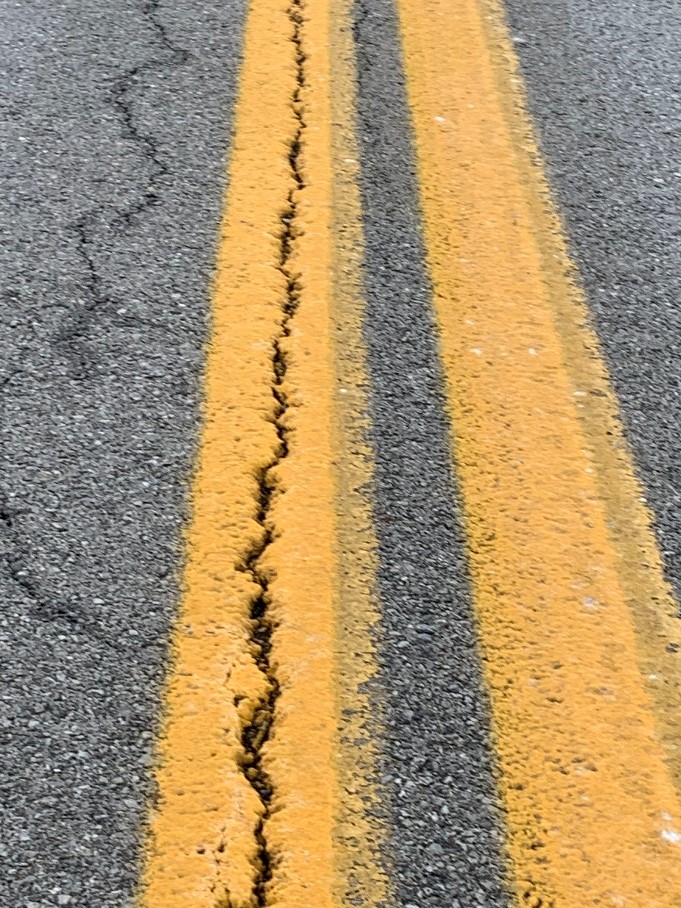
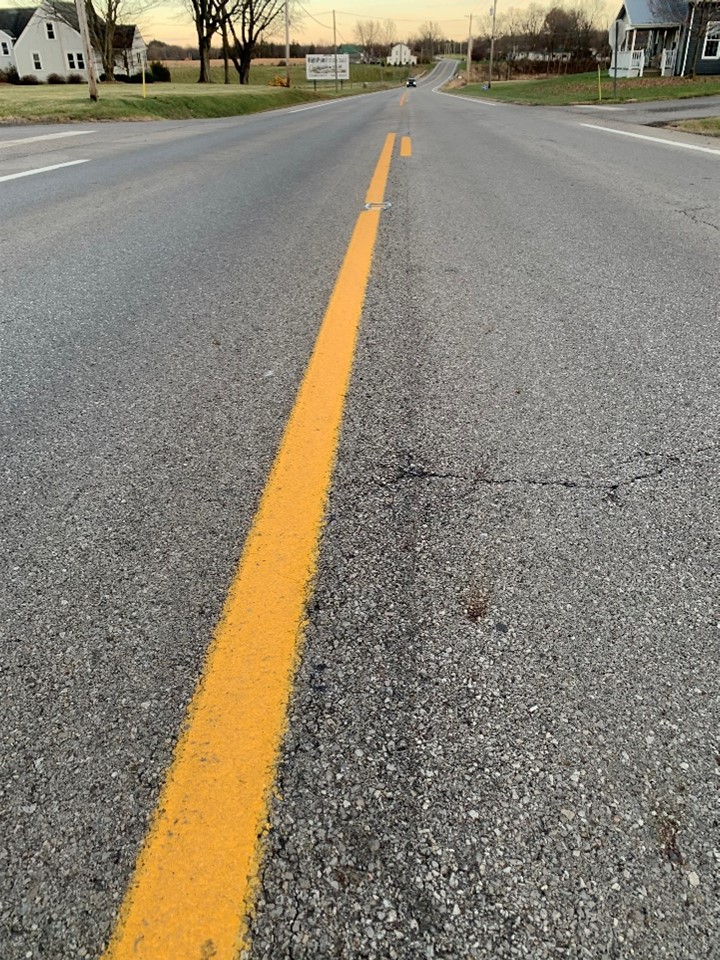
These pictures below are from another Test vs Control Project. Note: these pavements are OVER 15 Years Old!!
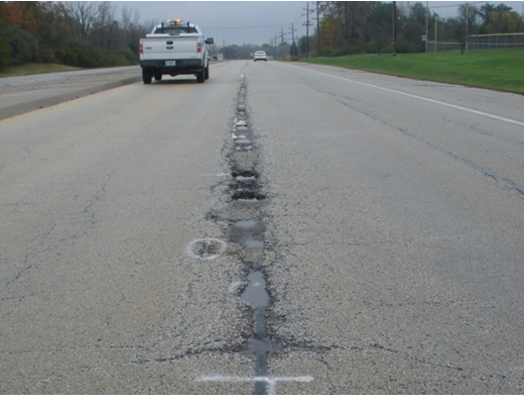
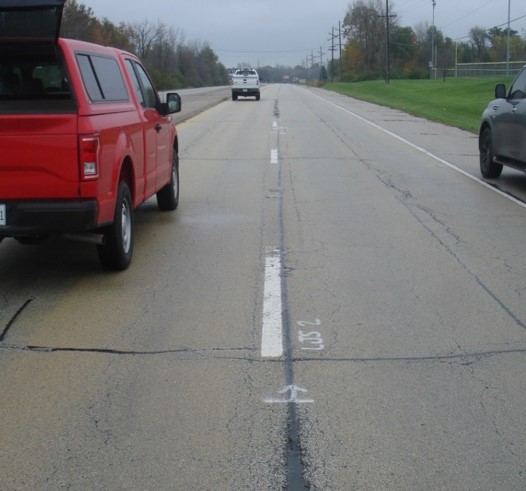