Rumble Strips Are Becoming More Popular, But They Also Need To Be Protected
It is important to plan ahead when protecting the infrastructure investments made for our streets, roads, and highways. Reducing air voids is critical to improving pavement life. When air voids are higher, permeability is higher, and this will adversely affect pavement life.
How can distracted driving accidents be reduced?
We know the dangers of workzone-related accidents. As we reported in April, over 700 people die in work zone crashes annually.1 And now because of the issues from distracted driving, centerline rumble strips are becoming increasingly common. Centerline rumble strips can reduce head-on collisions by up to 50%.2 So it’s more important than ever to invest in this proven source of safety.
Centerline Joints are Most Susceptible to Damage
Centerline joints are already particularly susceptible to water damage. Road managers know that the centerline or longitudinal joint is the first part of the pavement to fail. As a road’s most permeable part, this joint is susceptible to the elements. Air and water work down through this gap causing the joint to deteriorate, crack, and pothole. And when the longitudinal joint fails, the rest of the road soon follows—triggering the need for even more maintenance.
EDITORS NOTE: Centerline joints and longitudinal joints are used interchangeably throughout this article.
KEY INSIGHT: Since rumble strips are milled directly into the pavement, they make this area even more susceptible to water damage. For new pavements that will have rumble strips, it is critical to treat them proactively to avoid negative consequences in the future.
Rumble Strips CASE STUDY: What can happen if rumble strips are not adequately protected from the long-term effects of air and water infiltration?
Project Details: Recent pictures of rumble strips that have endured significant damage due to air and water infiltration at the centerline. This particular stretch of road is in west-central Indiana on the centerline joint of a US Highway. There are pictures from the fall of 2021 and pictures from May 2022.
Photos above from 2021 show the extensive damage that can occur at the longitudinal joint due to the additional stresses from rumble strips. Note the rest of the mat looks fine.
Photos above from May 2022 show what maintenance interventions are needed after centerline damage occurs. In addition to the patching of pot holes, also note the damage to centerline striping, which is expensive to install and even more expensive to replace.
What Can Be Done to Create Longer Lasting Roads?
So while rumble strips save lives, they can reduce the life and performance of the road. Industry researchers are looking for ways that can help ensure rumble strips can be installed without compromising road life. A recent study in Wisconsin noted:
The research team recommends that WisDOT continue its current standard practice regarding joint geometry and testing of joint density, but also consider the evaluation of other alternatives that show significant promise in reducing the risks of premature joint failures and minimizing the risk of accepting lower density at the joints relative to mainline of pavements.
Based on published data and review of case studies, implementing Void Reducing Asphalt Membrane (VRAM) during the construction process is recommended. Post-construction, it is recommended to use penetrating asphalt emulsions as a preventative and remedial treatment for longitudinal joints. 3
How Does VRAM Work?
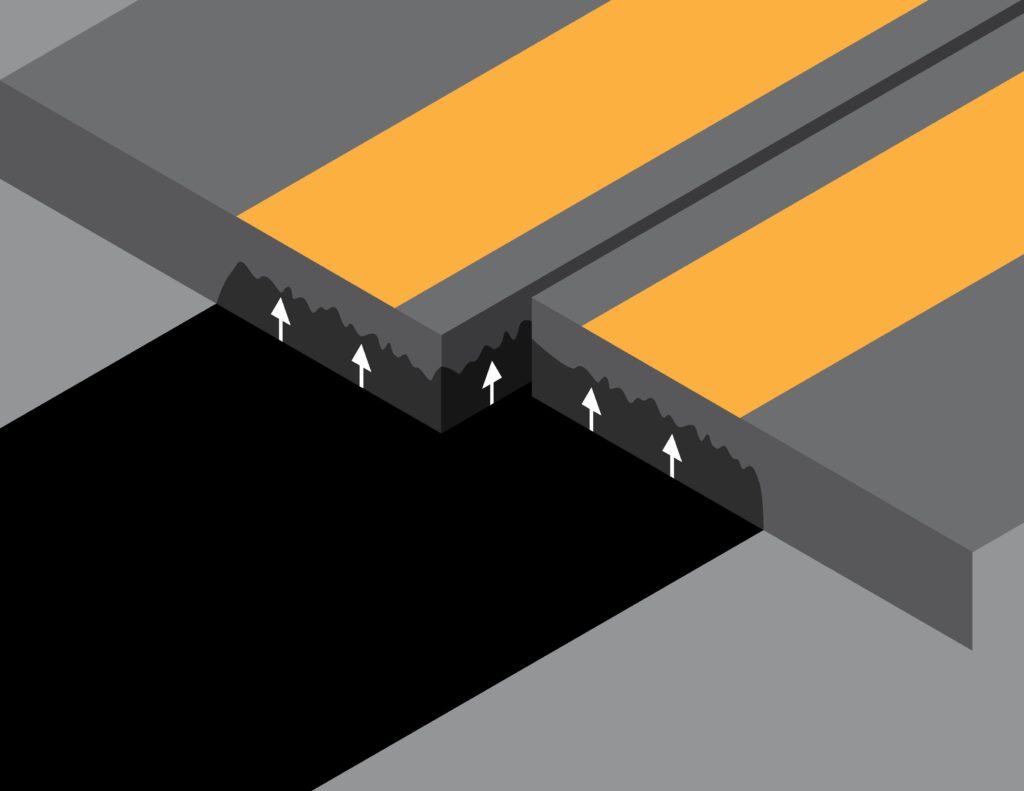
Applying VRAM at the time of construction, under the surface where centerline rumble strips will be installed, will reduce permeability in this most critical area. After placement of hot mix asphalt, the heat causes the material to migrate upward, filling voids and reducing permeability before the rumble strip is milled.
How can a Penetrating Emulsion Help Rumble Strips?
VRAM is a pre/during construction protection strategy and therefore helps fill voids from the bottom-up. Post-construction, it is recommended that a penetrating asphalt emulsion is used as a preventative and remedial treatment for longitudinal joints.3
What is a Penetrating Emulsion?
Originally developed for highway applications, Rapid Penetrating Emulsion (RPE) was created to extend pavement life. A critical element of RPE is its ability to quickly work its way into a surface to fill air voids. The rapid penetrating nature of these types of emulsions is a result of the formula’s low surface tension. Surface tension is what prevents water from going through the same sieve that RPE can penetrate through quickly. Into the surface of a road, not on the surface of a road is a critical component of an RPE and why it can be more beneficial to extending the life of the pavement and creating a safer surface for drivers.
How Well Does Your RPE Penetrate The Pavement?
An important benefit of what makes AMIGUARD™, Asphalt Material’s line of RPE products, particularly effective is its penetrating, air-void-filling capability. Unlike a fog seal that simply covers the pavement surface, AMIGUARD™ reduces permeability by penetrating into the pavement. AMIGUARD™ is a pro-active, preventative technology that can protect your pavements so you’re not spending more on repairs, maintenance, or repaving.
In addition to testing the emulsion in the lab, Asphalt Materials has measured permeability and texture depth in the field to verify that AMIGUARD™ is penetrating pavement surfaces, maintaining texture, and reducing pavement permeability.
The penetrating nature of the emulsion is important because it carries additional asphalt residue into the voids, therefore filling them and reducing permeability. In contrast to a VRAM which fills voids from the bottom up, RPE fills voids from the top down. VRAM must be placed along the centerline area where the two mats of asphalt will be laid. RPE is placed after the HMA and after the rumble strips have been installed.
“Creating and maintaining an impervious asphalt surface is imperative to the longevity of any asphalt roadway. Since 2016 I have been using a Rapid Penetrating Emulsion (RPE) produced by Asphalt Materials to seal the cold joints on my asphalt overlay and resurfacing projects.
What I like best about Asphalt Material’s RPE is that it penetrates the asphalt to fill any air voids that were left after a resurfacing project rather than sitting on top of the road like some other sealants.
– Curt Higginbotham Superintendent, Hendricks County Highway
Many Years of Research Contribute to Building Longer Lasting, Safer Roads
J-Band®, AMIGUARD™ and centerline rumble strips can work together to protect roads, drivers, and workers. Let’s have a discussion about how less frequent centerline maintenance can help save time, money, and lives by contacting one of our team members at Marketing@Asphalt-Materials.com.
“This (Wisconsin) research helps to confirm the direction the department has taken with recent changes to longitudinal joint specifications.”– Project Manager, Dan Kopacz, WisDOT3
To learn more about RPE and AMIGUARD™, you are encouraged to read this article: How Penetrating Emulsions Help Create Longer Lasting, Safer Roads. https://asphalt-materials.com/how-penetrating-emulsions-help-create-longer-lasting-safer-roads/
A Commitment to a Safe and Sustainable Infrastructure Since 1956
Asphalt Materials, Inc., formed in 1956, has been continually focused on the asphalt business. A core strength of our business is the formulation, manufacturing, and R&D of asphalt binders and emulsions. Our Asphalt Companies continually supply high-quality products and services around the United States, allowing us to excel in pavement preservation techniques and construction services.
We are a proud member of The Heritage Group and bring over 65 years of experience in the asphalt industry to road construction projects. Our teams of professionals are dedicated to creating longer-lasting, safer roads with quality, reliable asphalt materials.
We work closely with the Heritage Research Group team to ensure the highest quality asphalt materials and processes are brought to market. We are committed to building long-term relationships and mutual trust. We are excited to tackle our industry’s biggest challenges, looking for new and inventive ways to create solutions that will mean better, safer, and longer-lasting roads.
SOURCES:
1 National Workzone Safety Information Clearinghouse
2 U.S. Department of Transportation Federal Highway Administration, FHWA Home/ Safety / Roadway Departure / Center Line Rumble Strips (T 5040.40)
3 https://wisconsindot.gov/documents2/research/0092-21-05-research-brief.pdf
Editor’s Notes:
- Centerline joints and longitudinal joints are used interchangeably throughout this article.
- VRAM, Void Reducing Asphalt Membrane is referred to in Illinois as LJS, Longitudinal Joint Sealant.
- Depending on the situation VRAM can be sprayed at different width’s. It should be noted that 18” is a typical application width for centerline applications.
J-Band® is a VRAM product of Asphalt Materials, Inc. and was created in the labs of The Heritage Research Group. AMIGUARD™ is a rapid penetrating emulsion product of Asphalt Materials, Inc. and was created in the labs of The Heritage Research Group.