VRAM Continues to Pay Dividends Even Four Years After Initial Construction.
The year 2021 was another important year for VRAM, as we added several states to the list of those with VRAM experience. It is now 21 states and The District of Columbia. VRAM stands for a Void Reducing Asphalt Membrane.
The year 2021 was also important from the perspective of how well roads constructed with VRAM continue to perform. Since 2002 VRAM treated roads continue to be longer-lasting, safer and more resilient than roads that are not utilizing VRAM at the time of construction.
Over the coming weeks, we will review a number of different case studies of VRAM treated roads across our network.
The project we would like to report on is in Wayne County Ohio and was originally constructed in August of 2017. As you will note below, the performance between the VRAM Treated Section and the Control Sections are showing a drastic difference in centerline joint performance.
Owner: ODOT
Applicator: Specialized
Prime: Kokosing
Project: Wayne Co US-250
Location: New Pittsburg, OH
Date Constructed: 8-21-2017
Date Reviewed: 11-29-2021
Weather on Day of Review: Sunny, cool and 36°F
The VRAM test section started at mile marker 3.62 and continued to mile marker 5.48.
There are two control sections in this project; the west control section had 100% cracking with 1/2”-3/4” cracks. The east section also had 100% cracking with 1/2” crack. Both sections had multiple longitudinal cracks developing along centerline cracking back towards the centerline seam.
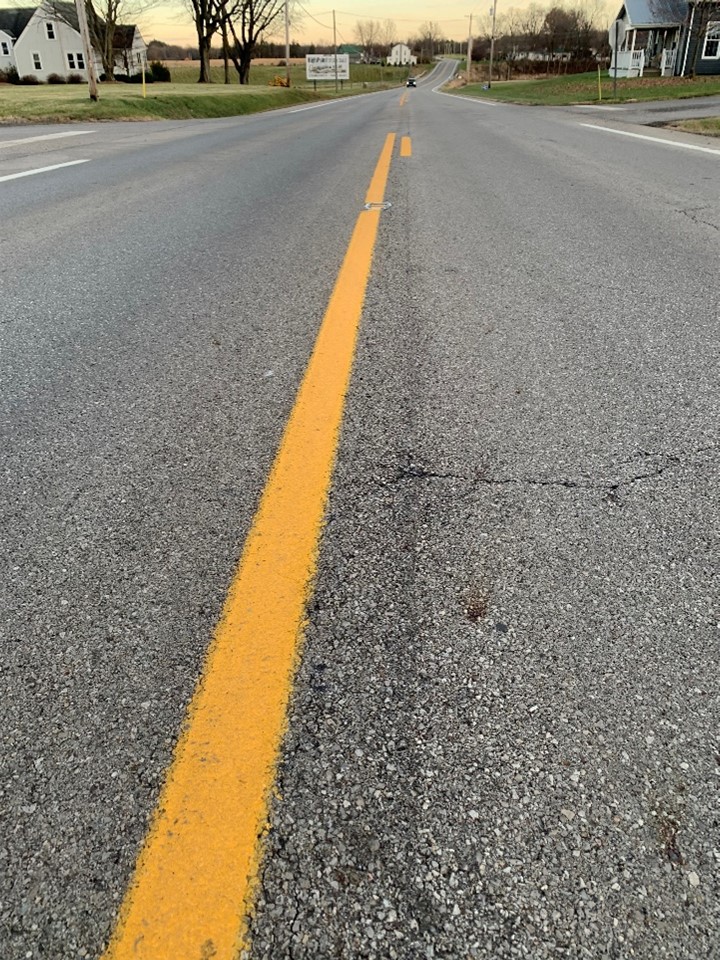
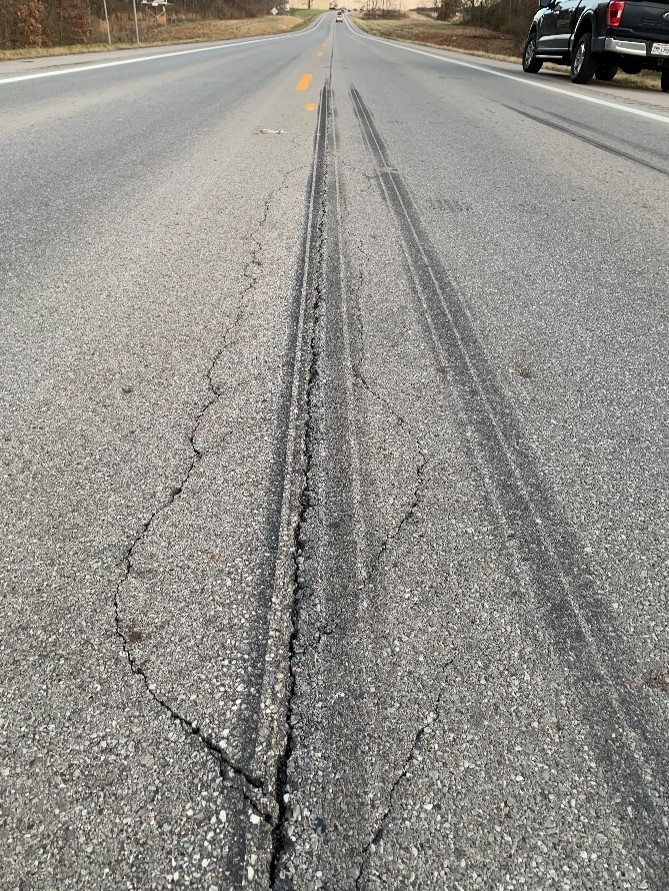
As Asphalt Materials’ Chad Crosby has noted in previous reviews, “the control sections would benefit from a crack seal soon.”
Scope: Mile 0.00 to 3.62 Control
Mile 3.62 to 5.48 Test
Mile 5.48 to 8.08 Control
Mix: 1 1/2” 12.5mm Type A (446) PG64-22
Road managers know that the longitudinal joint is the first part of the pavement to fail. As a road’s most permeable part, this joint is susceptible to the elements. Air and water work down through this gap causing the joint to deteriorate, crack and pothole. And when the longitudinal joint fails, the rest of the road soon follows—triggering the need for even more maintenance.
Since 2002, VRAM has been used successfully in 21 states and The District of Columbia to help create a more resilient infrastructure. Applying VRAM at the time of construction, under the surface where centerline rumble strips will be installed, will reduce permeability in this most critical area.
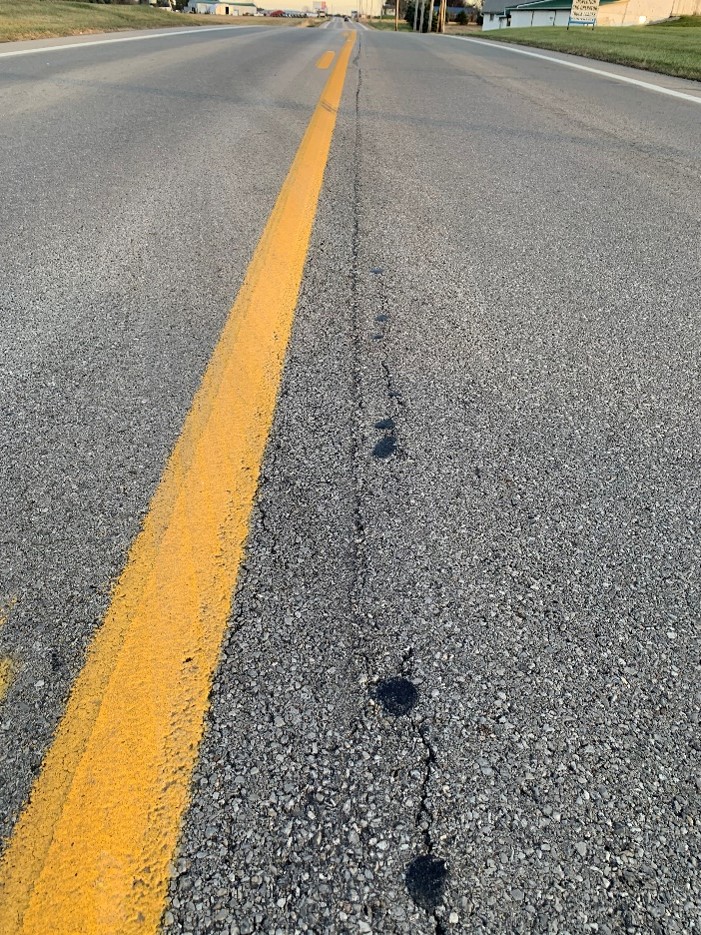
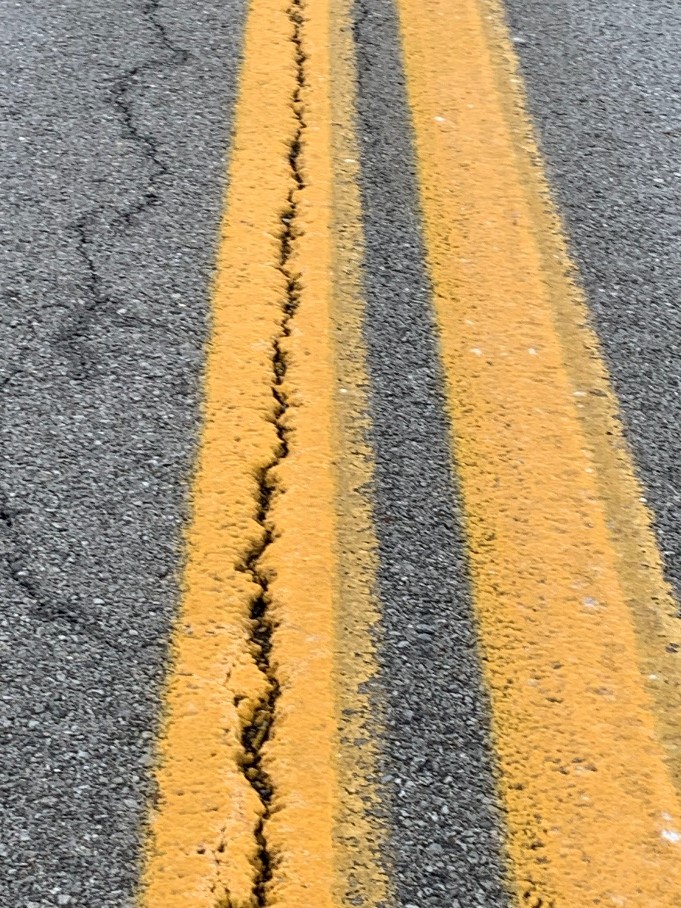
An investment in protecting the longitudinal joint helps roads last up to 5 years longer and delivers a return on investment of 3 to 5 times its cost. An Indiana DOT life cycle analysis showed that an investment of $12.5M in J-Band would result in a $39M in savings (approximately 3:1 ROI). While the use of J-Band adds initial cost to the road, it delivers a significant return on investment of up to five times its cost.
A road is more resilient when less maintenance is required. VRAM is a wise financial investment, and an investment in making roads safer and more sustainable. Wise infrastructure investments will also enhance tax-payer confidence that their money is being spent with their best interests in mind. We believe that these types of projects will motivate project teams to collaborate to achieve better outcomes. These pictures of the test and control sections should provide an objective measure of sustainable performance, which will draw attention to the good work being undertaken by counties like Wayne County Ohio.
As an added bonus, VRAM is the American-made solution to the longitudinal joint problem. Unlike other treatments, this Void Reducing Asphalt Membrane significantly reduces air voids in longitudinal joints. J-Band® is Asphalt Materials’ VRAM product and was created in the labs of Heritage Research Group. J-Band is a materials approach, applied prior to paving under the eventual location of the longitudinal joint. It migrates upward, fills voids, and reduces permeability as the hot mix is installed on top of it.
To learn more about J-Band, connect with our team by sending us an email at: Marketing@Asphalt-Materials.com.
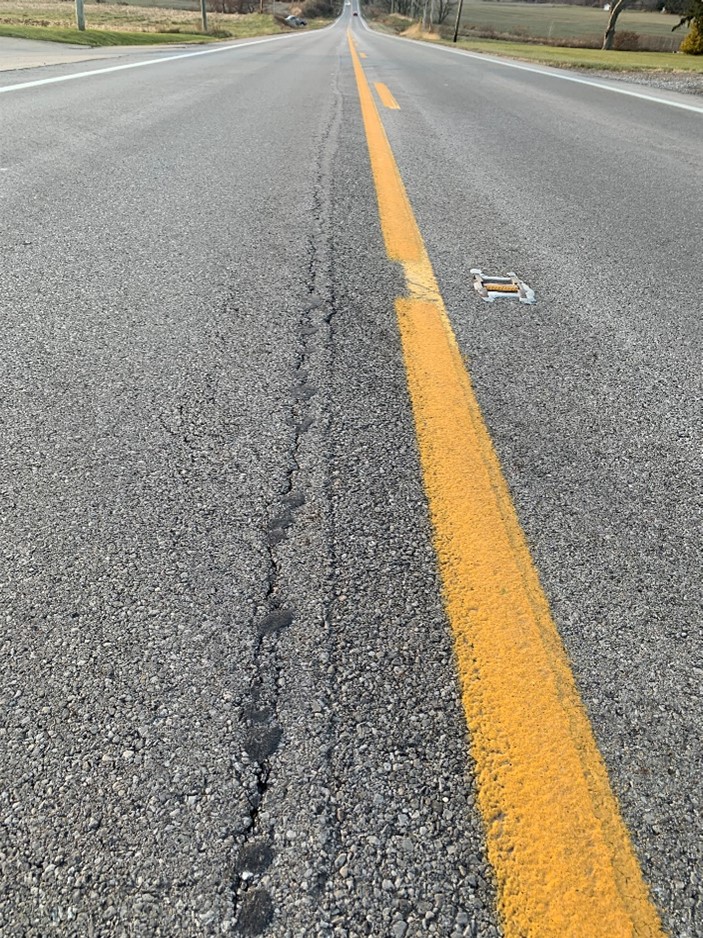
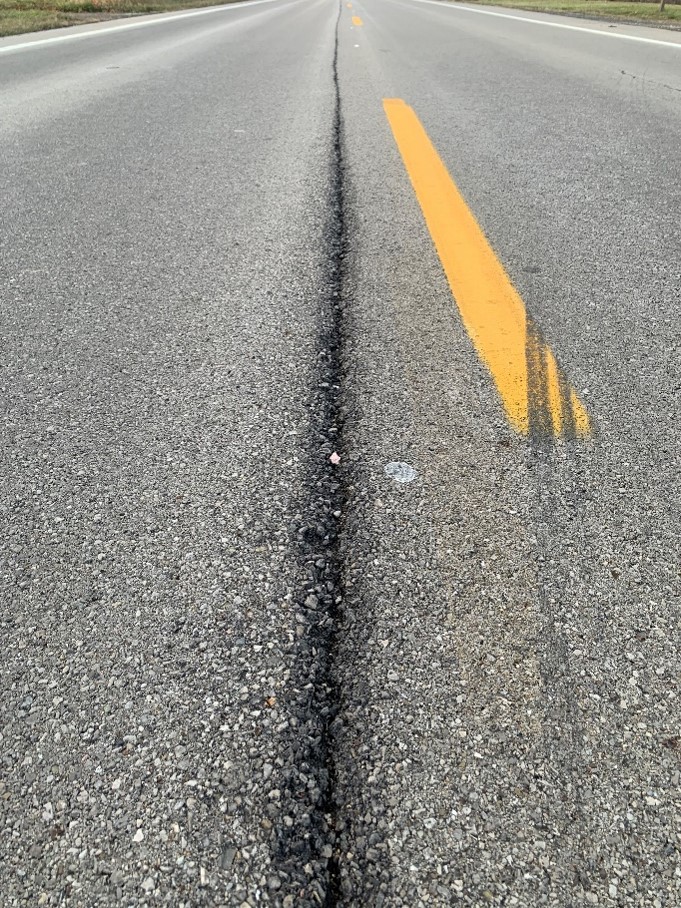