Why is Longitudinal Joint Damage Such an Important Issue for Roads?
A Minnesota DOT Field study from December 2020 reported that higher air void contents at the longitudinal joint can expose pavements to premature deterioration and, as a result, compromise pavement integrity and performance. In Minnesota, the report indicates their primary concern during asphalt pavement construction is the achievement of high density in the mixture, especially for the longitudinal joints.
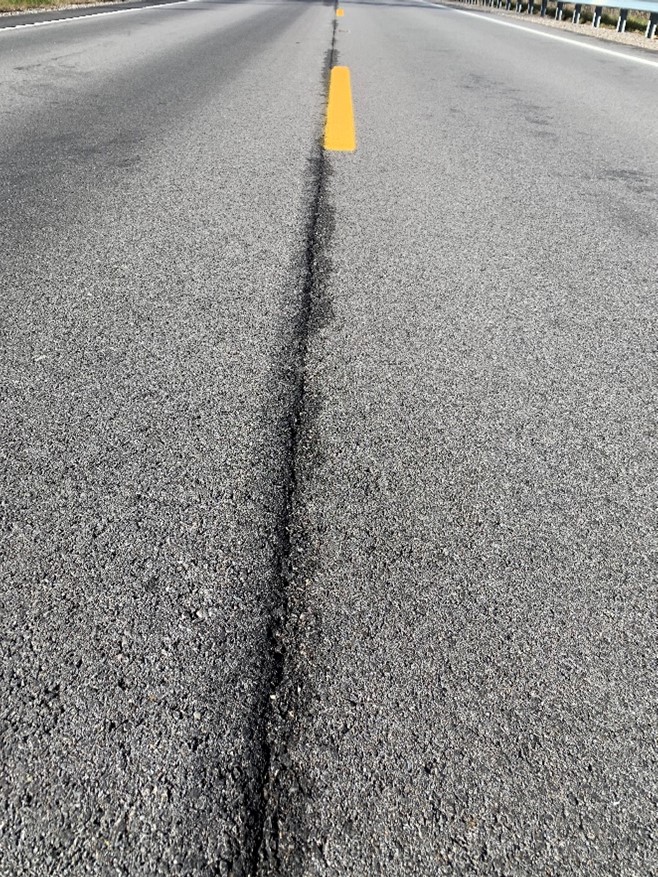
This very important issue will intensify as funding for new road construction and repairing of older pavements increases. In their December 2020 report, the State of Minnesota values their pavements as representing the largest replacement cost of all assets owned by the Minnesota Department of Transportation (MnDOT), with a value of $29.5 billion. (1)
What Approaches Have been Tried?
In Minnesota, the primary concern during asphalt pavement construction is the achievement of a sufficiently high density in the mat, especially at the longitudinal joints. A longitudinal joint is located at the interface between two parallel asphalt pavement mats. (1)
Historically, the main longitudinal joint construction techniques used in the United States include mechanical methods, such as the use of echelon/tandem paving, various rolling patterns, various joint types (butt, tapered, and notched wedge), edge restraining or pre-compaction devices, infrared joint heaters, cutting wheels, joint adhesives, and joint sealers. Researchers at Purdue University indicated that in 2011 only 12 state DOTs in the United States had specifications that included a longitudinal joint density requirement. (1)
Void-reducing asphalt membrane (VRAM) is a hot-applied, highly polymer-modified asphalt membrane that extends the life of HMA longitudinal joints by migrating into 50% to 75% of the HMA void structure after rolling, thus reducing permeability at the joints and improving the mechanical performance of the mix at the joints through increased durability.
Unlike other treatments, VRAM, a Void Reducing Asphalt Membrane significantly reduces air voids in longitudinal joints. VRAM is a materials approach and is applied prior to paving under the eventual location of the longitudinal joint. The best way to eliminate voids in your pavement is to fill them with asphalt content at the time of construction. If you are able to have VRAM specified in your region, you can use a VRAM to help fill voids at the centerline at the time of construction, to reduce or eliminate permeability.
What has been VRAM’s Track Record?
The reduction in permeability minimizes water and air intrusion into the joints, resulting in reduced cracking and stripping and improved pavement performance. The improved mechanical performance is the result of increased amounts of polymer-modified asphalt within the mix at the longitudinal joints, which makes the mix more durable and less prone to cracking due to better recovery from loadings and increased bond strength. Extending the pavement life by one year saves MnDOT 5% per year in life-extension costs.
The laboratory specimens containing VRAM showed good performance in terms of having the highest joint bond energy, fracture energy, and work of fracture and good surface bond energy compared to the specimens without VRAM. The use of VRAM also reduces permeability and air void content, which reduces the intrusion of water into the pavement. The field surveys did not show any distress that is of concern. Based on the laboratory testing results, the use of VRAM improves the performance of the asphalt pavement mat at the longitudinal joints by protecting against deterioration caused by water and air infiltration. (1 – MnDOT Study)
As of 31 December 2021, there are now 21 states and The District of Columbia that have experience using VRAM on their roads.
How long has VRAM been Used?
VRAMs have been helping fill voids in longitudinal joints of pavements since 2002. Because of the quantity and engineered properties of a VRAM, it flows into and fills voids with asphalt, which helps to preserve pavements and longitudinal joints from premature failure.
The J-Band Team. A Leader in VRAM Experience.
J-Band is an industry leading VRAM that has been helping fill longitudinal voids in pavements since 2002. Because of the J-Band VRAM unique binder properties, it is able to help preserve pavements and longitudinal joints from premature failure!
How can I Learn More about VRAM?
Through our long history serving the asphalt industry, we understand that longitudinal joint deterioration has long been a problem for not just engineers and applicators, but the communities they live in. As you look at some of the pictures below, it is important to note that a joint opening can occur over J-Band, but it’s the lack of damage due to the protection of this joint that is what matters to the long-term ‘life’ of this area of the road. The VRAM adds durability to the joint area where these two mats come together.
Thanks to collaboration between state transportation agencies, industry experts at Asphalt Materials, Inc., and the leading-edge laboratories at Heritage Research Group, it’s easier than ever to preserve your infrastructure investments. J-Band® is a product of Asphalt Materials, Inc. and was created in the labs of the Heritage Research Group. To learn more about J-Band and to connect with one of our team members, you can email us at Marketing@Asphalt-Materials.com.
We have been reviewing many projects that were completed in the past five + years, here within the News Section of our website. The following pictures help illustrate some of the longitudinal joint issues we have observed and how well VRAM is still protecting the centerline from air and water infiltration, 2, 5, 10 and even more than 15 years later.
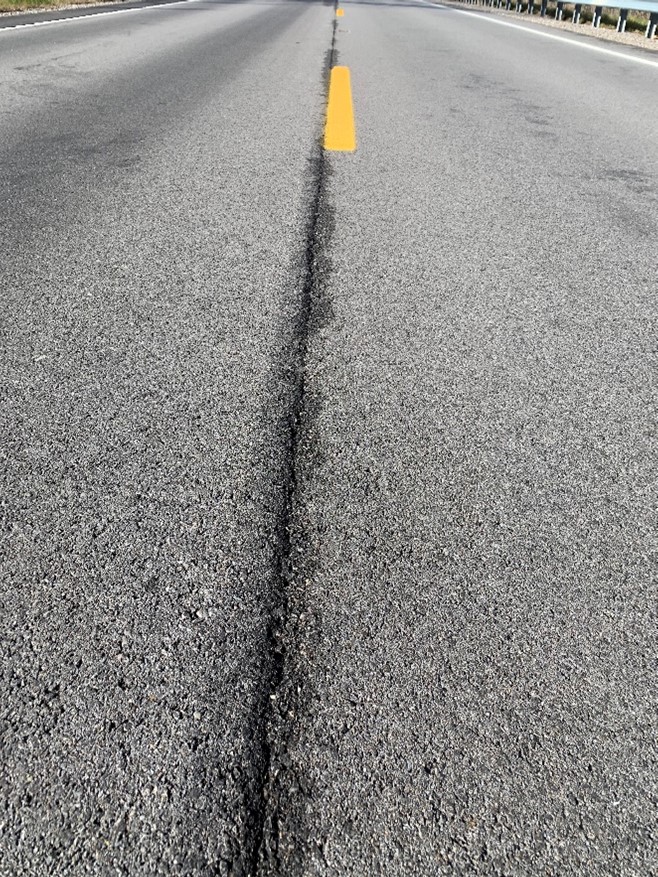

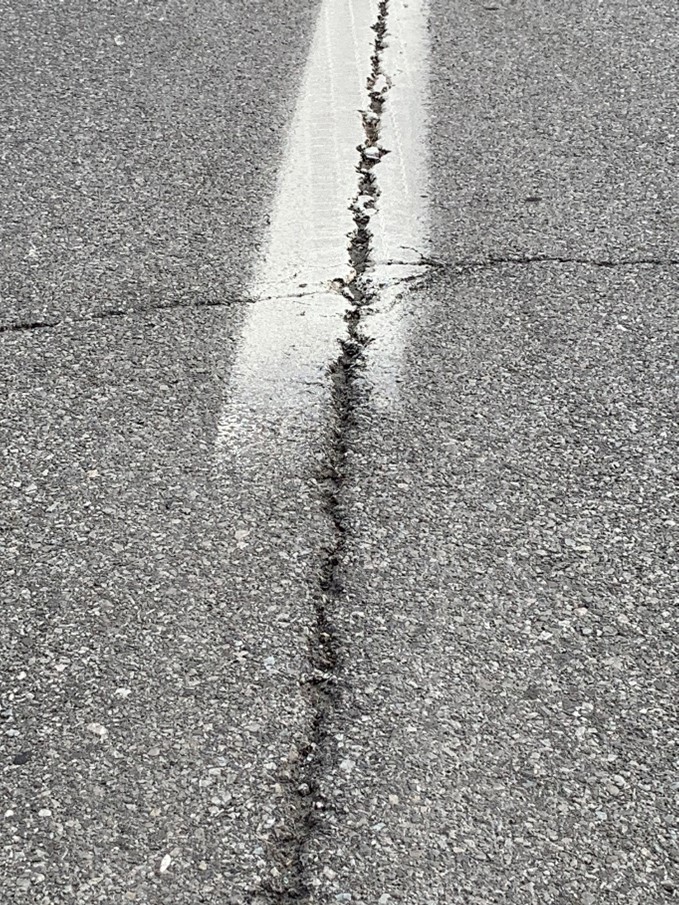
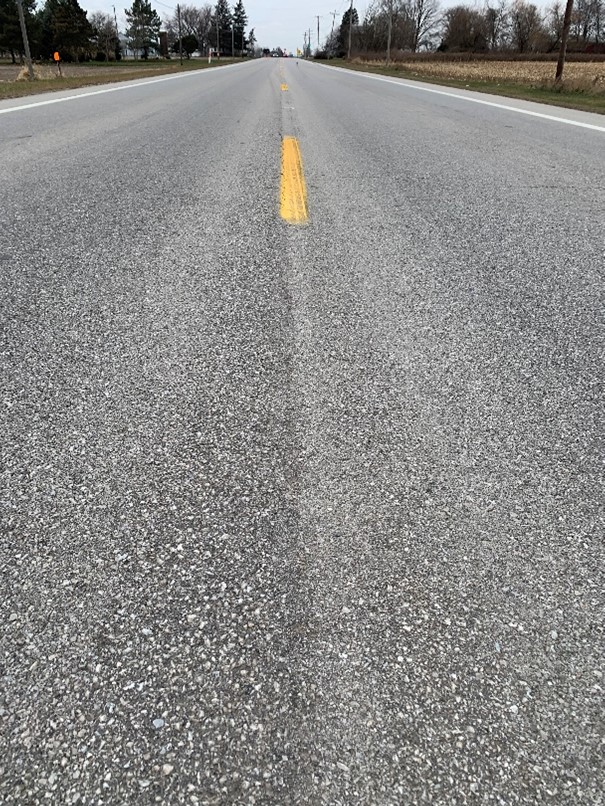
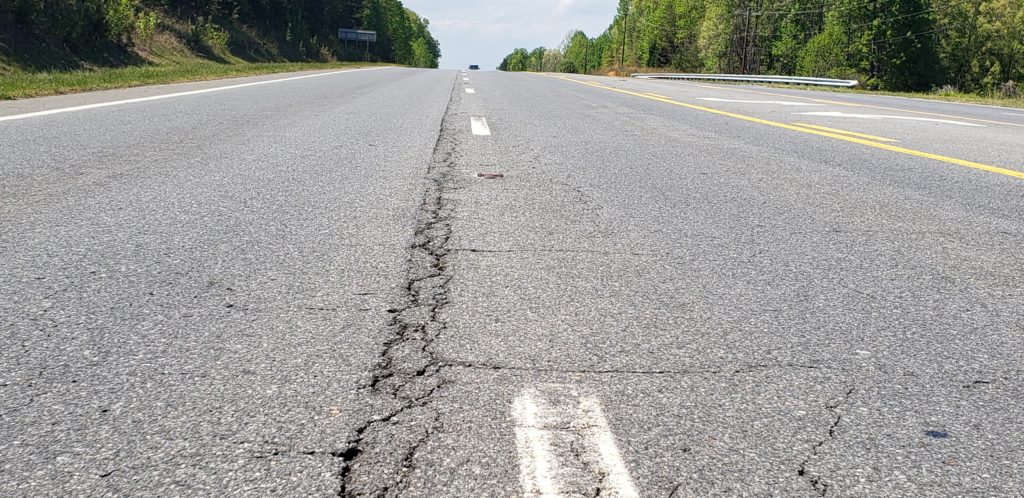

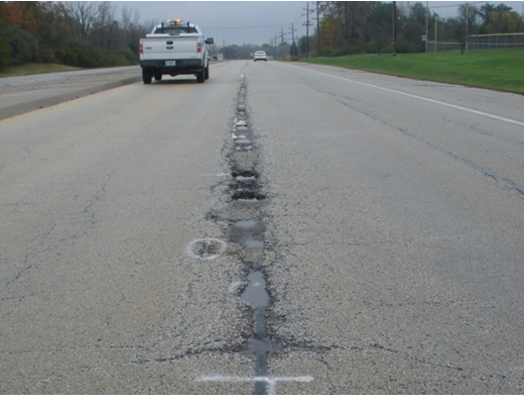
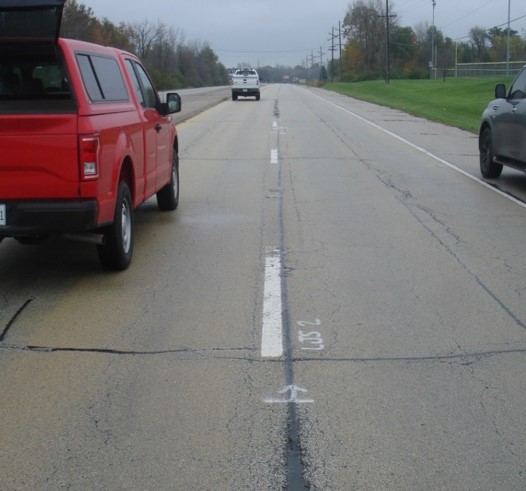
1 – Use of J-Band to Improve the Performance of the HMA Longitudinal Joint. R. Christopher Williams, Principal Investigator Asphalt Materials and Pavement Program Institute for Transportation at Iowa State University, DECEMBER 2020 Research Project Final Report 2020-33.
http://mndot.gov/research/reports/2020/202033.pdf